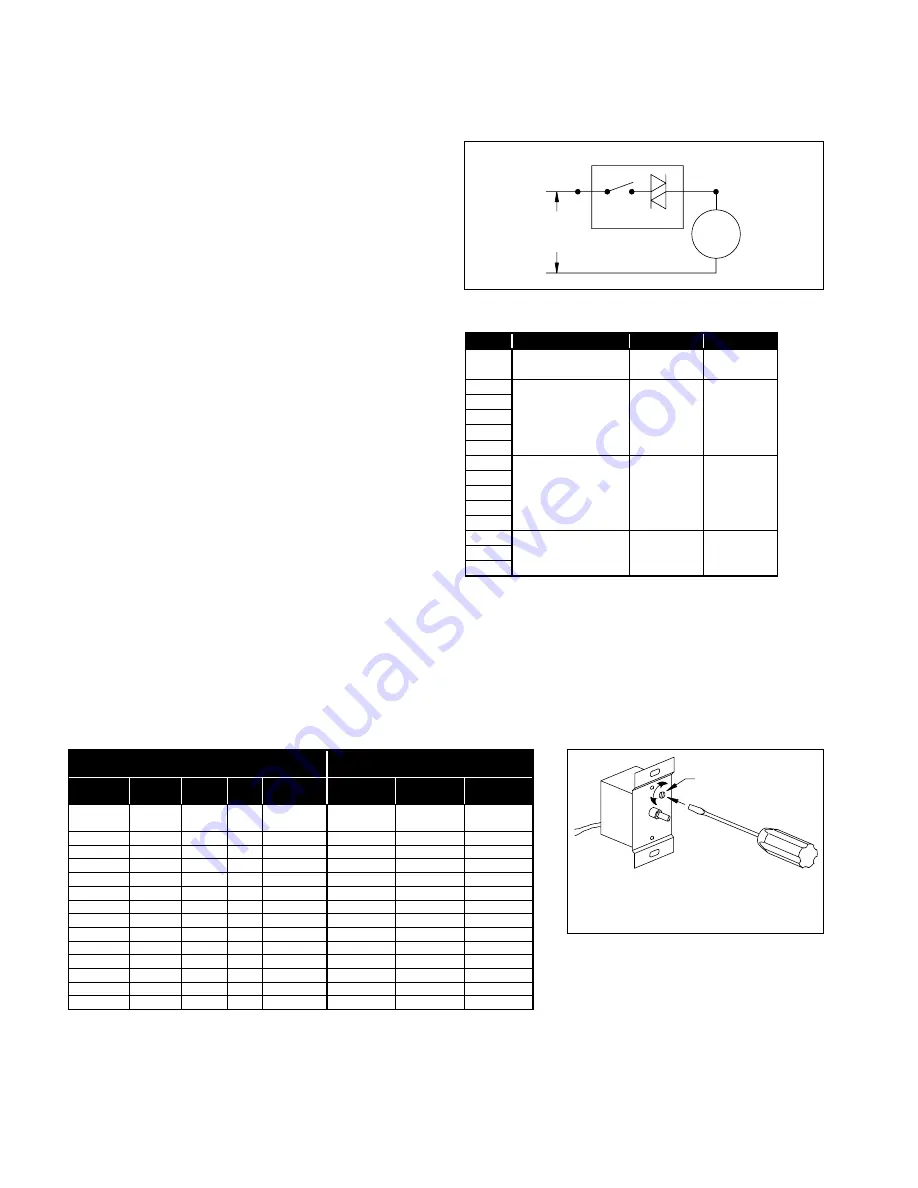
4
Twin City IM-4050
Figure 3. Low End Setpoint Adjustment
NOTE:
5 amp model shown. On 10 and 15
amp models, adjustment is made through clear-
ance hole in heat sink.
SETPOINT
ADJUSTMENT
SCREW
Table 4. Speed Controller Size
Speed Control Installation
(Models DCLH, DCLP, DCRD, DCRU, DCRUR, DCRW, DCRWR - optional)
Speed control is available using
115/60/1 open
type
PSC or shaded pole motors.
Installation
Connect control in series with motor and line voltage
(
115V only
). Never connect across line. See Figure 2.
Minimum Speed Setpoint
All controls are factory set to 65V±3V output as stan-
dard with an input voltage of 120V. If different minimum
speed is desired, the control may be adjusted by turn-
ing minimum speed pot clockwise to decrease minimum
speed and counterclockwise to increase minimum speed.
Refer to Figure 3.
Warning:
If minimum speed is readjusted, verify unit
ampere draw does not exceed motor nameplate amps.
Do not operate unit in range where amp draw exceeds
motor nameplate.
Caution:
These motors operate more efficiently in the
ranges set from the factory. Operating motor outside
these ranges (see Table 3) may cause motor to run
hotter and substantially shorten motor life.
Note:
Lowering the minimum speed setpoint may
adversely affect motor start-up characteristics.
Warning:
Certain failure modes of solid-state controls
such as half-waving can cause high levels of DC, motor
overheating and motor burn-out. Therefore, a thermal
overload protection (integral with motor) is required to
limit the maximum motor temperature under such a
failure.
Note:
Do not allow any sleeve bearing motor to operate
below 500 RPM. Operation below 500 RPM will sub-
stantially shorten bearing life.
Figure 2. Connection Diagram, Speed Control
SPEED CONTROLLER
AC
LINE
(115V)
SWITCH TRI-AC
MOTOR
Table 3. Speed Controller RPM Range
HP
RPM
MAX. RPM
MIN. RPM
1/30
1650/1500/1350
2,3
1650
4
1300
4
1/8
1500
5
950
5
1/15
860
860
500
1/8
1/6
1/4
1/2
1/8
1140
1140
900
1/6
1/4
1/2
1
1/3
1725
1725
1200
1/2
3/4
NOTES:
•
Speed control available
only
with 115/60/1 open motors (thermally
protected).
•
Three-speed motor (multiple tap winding).
•
Speed control
should not
be connected to low speed tap on motor
because of starting characteristics.
•
Speed control connected to high speed tap on motor.
•
Speed control connected to medium speed tap on motor.
MOTOR
SPEED CONTROLLER
DESIGNATION / FLA
PART
NUMBER
ENCLO-
SURE
VOLT-
AGE
HP
RPM
KBWC-15K
5 AMP
KBWC-110
10 AMP
KBWC-115
15 AMP
66543600
Open
115V
1/8
1650/1500/
1350
X
66804500
Open
115V
1/15
860
X
66543700
Open
115V
1/8
860
X
67123100
Open
115V
1/6
860
X
66543800
Open
115V
1/4
860
X
66543900
Open
115V
1/2
860
X
66804600
Open
115V
1/8
1140
X
67125100
Open
115V
1/6
1140
X
66544000
Open
115V
1/4
1140
X
66544100
Open
115V
1/2
1140
X
66544200
Open
115V
1
1140
X
66544300
Open
115V
1/3
1725
X
66544400
Open
115V
1/2
1725
X
67122500
Open
115V
3/4
1725
X