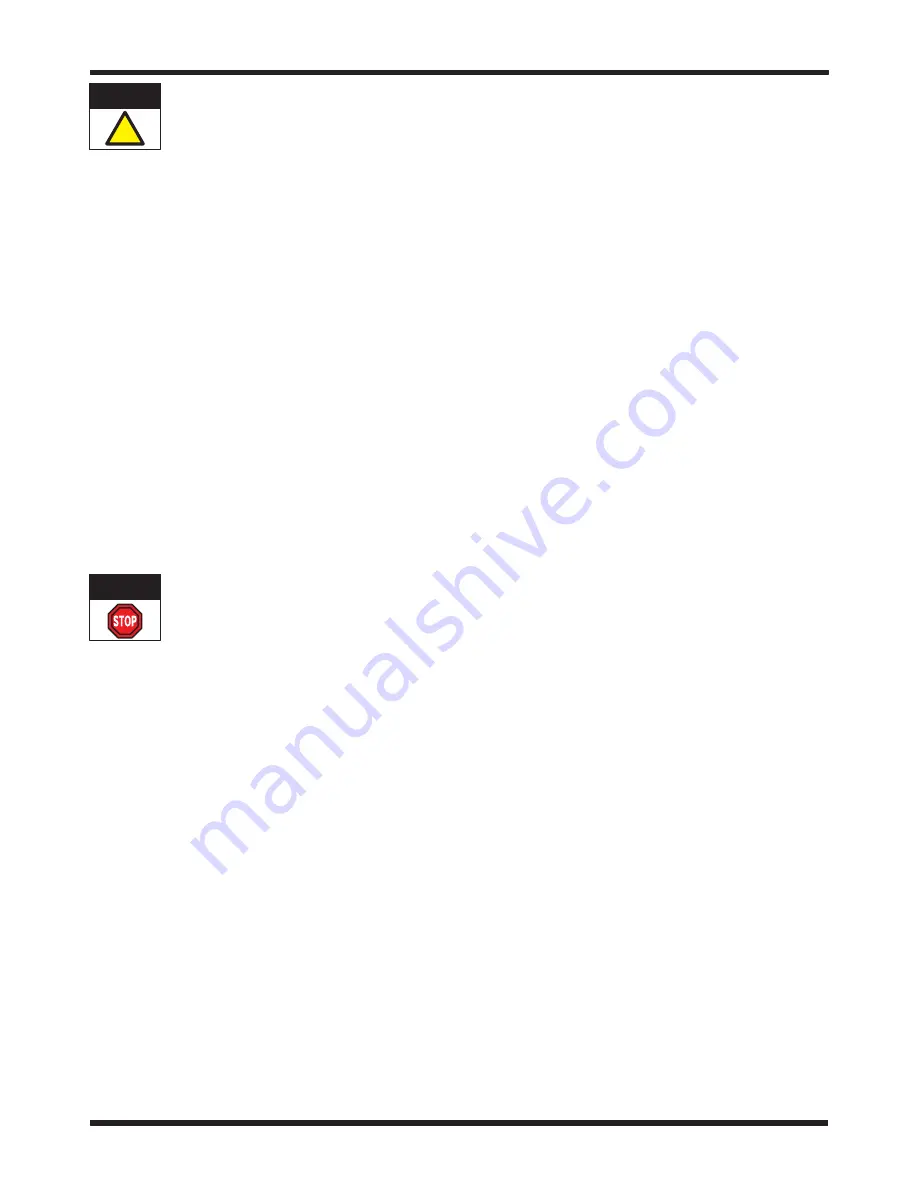
408-10111
Hydraulic Crimping Head 1901820-1
3 of 4
Rev B
Tyco Electronics Corporation
Operating the head WITHOUT the crimping dies
installed will damage the C"-Head or ram.
Install the dies as described in the appropriate die
instruction sheet. Refer to Figure 2.
4. CRIMPING PROCEDURE
The following procedure provides only general
information concerning crimping. Refer to the
instructions packaged with the dies (see
Figure 2) and power unit for detailed information,
including wire stripping dimensions and instructions
for positioning terminals and splices in the dies.
1. Insert terminal or splice in the stationary die
according to the instructions packaged with the
dies.
2. Activate the power unit to advance the dies and
hold the terminal or splice in place.
3. Insert stripped wire into the terminal or splice.
4. Activate the power unit to complete the crimp.
5. INSPECTION/MAINTENANCE
Make sure hydraulic pressure is released and
power supply is disconnected before following
inspection and maintenance procedures, unless
otherwise specified in the procedure.
Each crimping head is assembled and inspected
before shipment. It is recommended that the crimping
head be inspected immediately upon its arrival at your
facility, and at regularly scheduled intervals, to ensure
that the crimping head has not been damaged during
handling. Frequency of inspection depends upon the
following:
S
Care, amount of use, and handling of the head;
S
Type and size of products crimped;
S
Degree of operator skill; and
S
Environmental conditions.
Once a year, or every 7,500 cycles (whichever comes
first), the hydraulic head should be returned to Tyco
Electronics for magnetic particle inspection.
Additionally, inspect and service the head (as
described in Figure 3) every month or 1,000 cycles,
whichever comes first. Refer to Figure 1.
5.1. Cleaning
Remove accumulations of dirt and grease on the
crimping head, especially in areas where dies are
installed and terminals are crimped. Clean the entire
head frequently with a clean, lint–free cloth.
5.2. Visual Inspection
In addition to the inspections listed in Figure 3,
inspect the head for nicks, scratches, and cracks.
Inspect for cracks especially at the corners of the
“C”–head and around the top of the cylinder. Refer to
Figure 4.
Inspect the metal surfaces for nicks, cracks,
scratches, and excessive wear, especially where
sliding contact occurs.
5.3. Crimping Head Check-Out Procedure
If the ram fails to retract after completion of a
crimping cycle, the cause may be in the crimping
head. To determine whether or not the trouble is in
the crimping head, release pressure in the power unit.
If the ram retracts, the trouble is not in the crimping
head. If ram does NOT retract, refer to Section 6,
RETURN/REPAIR.
6. RETURN/REPAIR
Order replacement parts through your Tyco
Electronics representative, or call 1–800–526–5142,
or send a facsimile of your purchase order to
1–717–986–7605, or write to:
CUSTOMER SERVICE (38–35)
TYCO ELECTRONICS CORPORATION
P.O. BOX 3608
HARRISBURG, PA 17105–3608
Crimping heads may also be returned for evaluation
and repair. For tool repair service, contact a Tyco
Electronics representative at 1–800–526–5136.
7. REVISION SUMMARY
Since the previous release of this document, the
corporate logo was updated.
CAUTION
!
DANGER