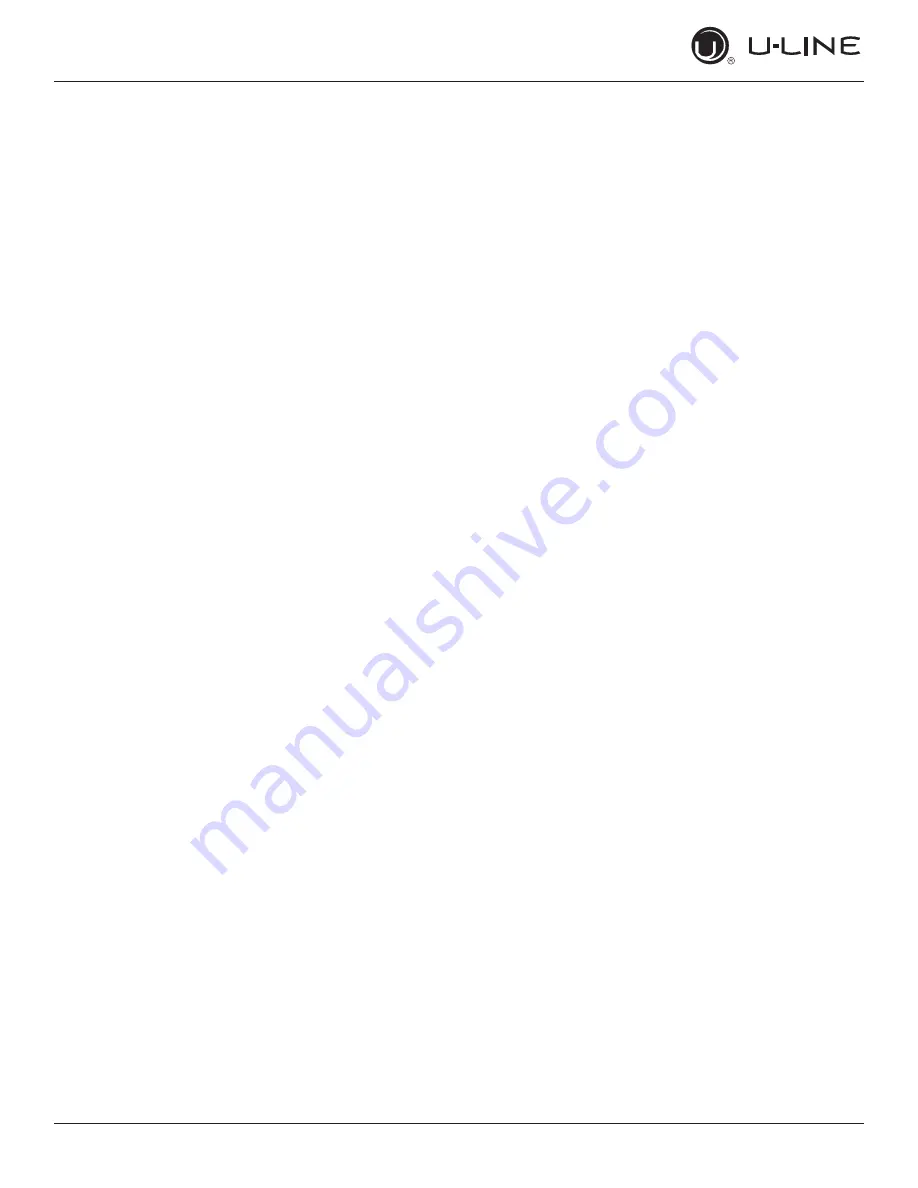
USER GUIDE
u-line.com
Troubleshooting Extended
b. If unit fills, the float switch is malfunctioning and
needs to be replaced (part # 80-55538-00).
4. If unit is 3 Class product, enter service mode and
activate relays 1 and 4 to determine if unit fills with
water.
a. If it does not fill, check water valve for power
during sequence.
• If there is power, check valve resistance to
determine if coil is shorted.
• Check valve to ensure it is not blocked with
debris.
b. If unit fills, the float switch is malfunctioning and
needs to be replaced (part # 80-55538-00).
E13: Float switch in reservoir not dropping
quickly enough
This error is designed to detect insufficient ice product due
to overheating or poor water quality. Failure to address
this error can cause permanent damage not covered under
warranty. The user may notice deteriorating ice quality
prior to the error.
Steps to check and correct - remember it is
necessary to power cycle after making the
corrections.
1. Ice is slushy and user noticed deterioration in quality
prior to the error.
a. Check condenser and toe kick. Fan must be
operating and clear of debris.
b. Check TDS level. High levels of TDS will result in
this error.
2. In more severe conditions, not covered above, the unit
may run up to an hour prior to generating this error,
resulting in very slushy ice or no ice production at all.
a. High TDS. High TDS restricts ability to produce ice
and causes excessive buildup of minerals on the
ice-making mechanism. A single cleaning may not
resolve this condition.
b. General cleaning has not been performed. A single
cleaning may not resolve this condition.
c. If customer has unit connected to a water
softener, have them consult a plumber to
disconnect from the softener.
d. Check compressor operation.
• If unit is not cooling or compressor is not
operating, diagnose and fix system problem.
• If unit is cooling, check auger for rotation. If
not rotating, check the motor and electrical
connections to auger.
3. If the ice has been solid and appears solid after a
power cycle check it is possible the float switch is not
operating properly and should be replaced.
P1: Drain related error
This error is designed to prevent water related issues due
to a failure of the unit to drain water. In most cases this
error is not related to the unit and related to improper
installation or restriction of the drain line.
1. If the unit does not have a drain pump this error is
generated by a missing jumper on the power harness.
Inspect and install jumper.
2. If the unit does have a drain pump.
a. Check the installation to ensure the drain line is
not restricted leaving the unit.
b. Inspect the drain pump to determine if the motor
is operating. A slight noise should be heard if the
pump is full of water.
Ice Level Issues
If there is a complaint regarding the unit filling too full with
ice.
1. Check the thermistor to ensure it is installed properly
and any holes through the rear of cabinet are
completely sealed with sealing compound. Warm
air that can make its way to the thermistor will give
improper readings and cause the bin to overfill.
2. The bin thermistor offset may be changed via
service mode option #5. Be careful to adjust in
small increments to suit customer preferences.
42