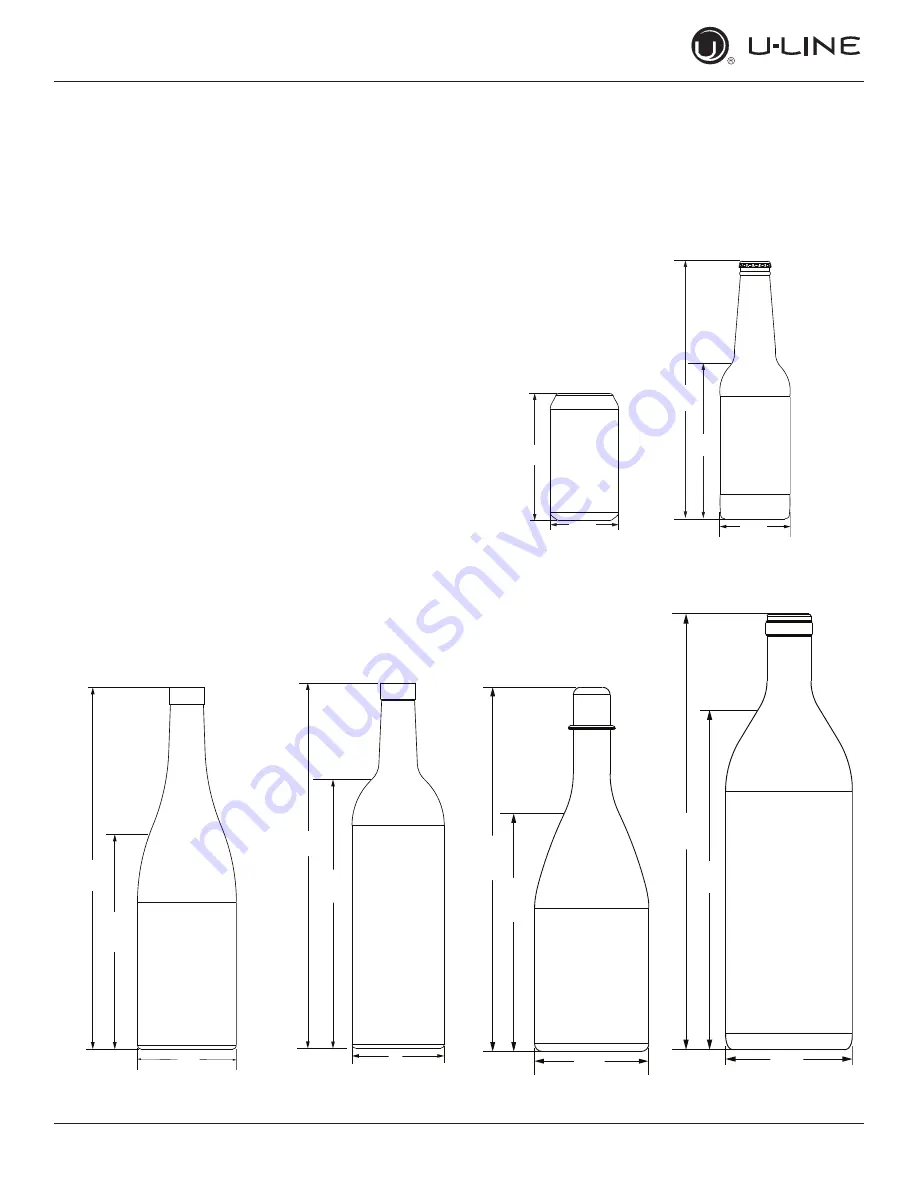
USER GUIDE
u-line.com
Airflow & Product Loading
Restricting airflow may result in poor product
performance, product failure, and uneven internal
temperatures and may freeze contents.
• Do not block the front grille - no additional clearance
around sides, top or rear of unit is needed for ventilation
• Do not install behind a closed door
• When loading, leave space between internal fans, vents,
and side walls to allow air to circulate freely
NOTICE
AIRFLOW
External
PRODUCT LOADING
Bottles and cans come in many shapes and sizes. Not
all bottles and cans will fit on every shelf and wine rack.
Larger diameter champagne and Magnum bottles only fit
on wine racks when noted on the product specifications.
When determining capacities U-Line uses typical 12 oz.
cans, 12 oz. bottles, 750 mL white wine and red wine
bottles shown below.
Airflow and Product Loading
Typical Can
(12 oz)
4
(123 mm)
(66 mm)
2
27⁄32”
19⁄32”
Typical Bottle
(12 oz)
9”
5
2
7⁄16”
5⁄16”
(135 mm)
(64mm)
(229 mm)
Typical White
Wine Bottle
11
(298 mm)
(750 mL)
3
¾”
(184 mm)
(82 mm)
11
¼”
¼”
Typical Red
Wine Bottle
11
(302 mm)
8
3”
29⁄32”
¾”
(222 mm)
(750 mL)
(76 mm)
Typical
Champagne Bottle
(750 mL)
3
11⁄16”
7
¾”
11⁄16”
(299 mm)
(94 mm)
(195 mm)
11
Magnum Bottle
(1.5 L)
13
10
3
1⁄8”
(334 mm)
11⁄32”
(263 mm)
27⁄32”
(98 mm)
Internal
23