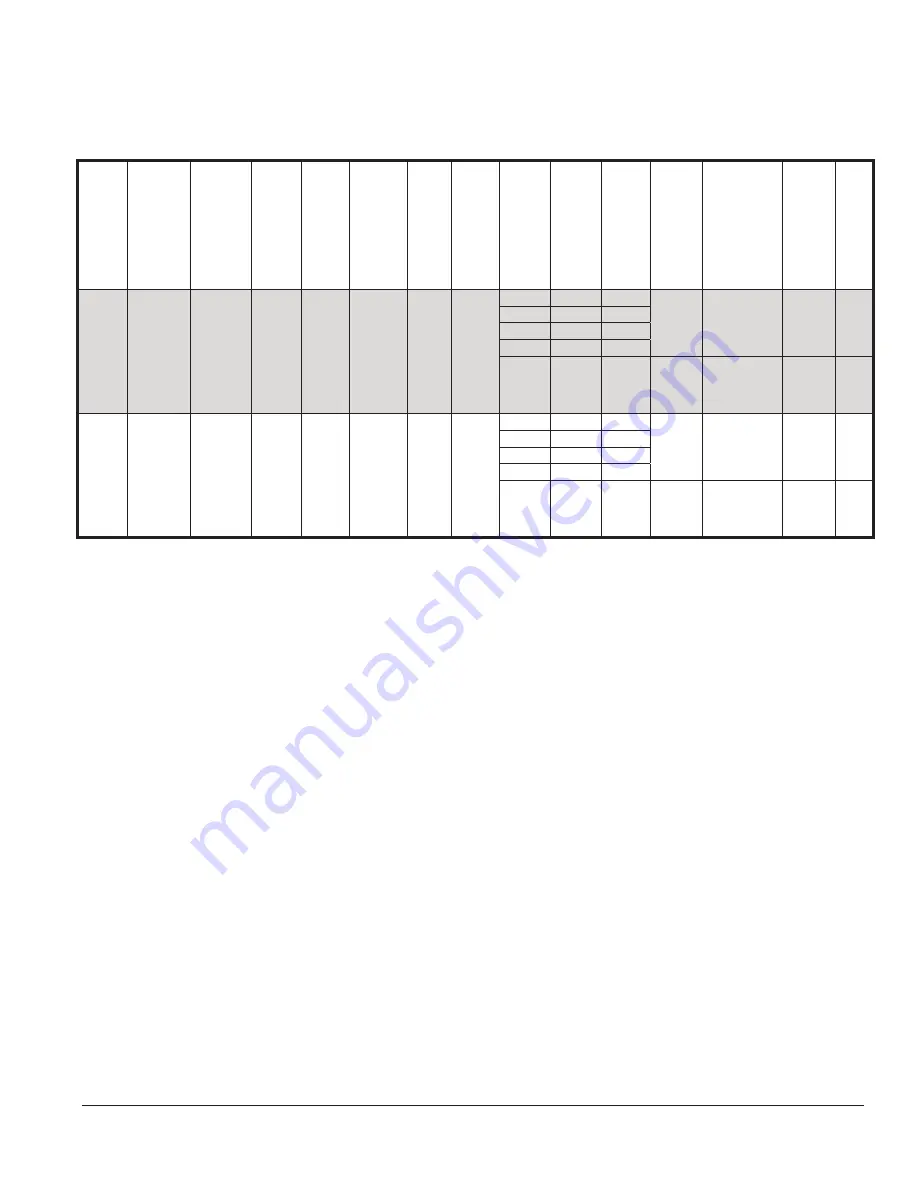
103448-10 - 6/18
69
Boiler
Model
Boiler
Supply
Connection,
Inch, FPT
Boiler
Return
Connection,
Inch, FPT
Near-
Boiler
Piping
Supply
Pipe
Size,
Inch
Near-
Boiler
Piping
Return
Pipe
Size,
Inch
Max
Allowable
Flow
through
Boiler,
GPM @
20°F DT
Flow,
GPM
@ 25°F
DT
Min
Req’d
Flow
through
Boiler,
GPM
@ 35°F
DT
Alliance
SL
Models
to be
installed
As Part
of Near-
Boiler
Piping
Alliance
SL
Coil
Required
Flow
Rate,
GPM
Alliance
SL Coil
Head
Loss,
Ft @
Required
Flow
Rate
Combined
Boiler,
Alliance SL
& Piping
Loop Head
Loss, Ft
*Recommended
Circulator
Make & Model for
Alliance SL installed
as Part of
Near-Boiler Piping
Reference
Figure
Notes
ALP080B
1
1
1
1
7.3
5.8
4.2
SL27
6
9
19.3
Taco 0014
Grundfos UPS26-99
FC (second speed)
25B
SL35
6
9
19.3
SL50
6
9.5
19.8
SL70
6
10
20.3
SL119
14
17
NA
Not Recommended
NA
Note 1
ALP105B
1
1
1
1
9.6
7.7
5.5
SL27
6
9
19.3
Taco 0014
Grundfos UPS26-99
FC (second speed)
25B
SL35
6
9
19.3
SL50
6
9.5
19.8
SL70
6
10
20.3
SL119
14
17
NA
Not Recommended
NA
Note 1
ALP150B
1
1
1
1
13.8
11
7.9
SL27
6
9
25B
Note 2
SL35
6
9
SL50
6
9.5
SL70
6
10
SL119
14
17
36
Taco 1400-45
Grundfos UPS 32-
80/2 (max speed)
25B
Table 16: Recommended Circulator Models for Alpine Boilers and Alliance SL Indirect Water Heaters
Installed as Part of Near-Boiler Piping Up to 75 Ft. Equivalent Length - Domestic Hot Water Circulator
VI. Water Piping and Trim
(continued)
Table 16 (continued): Recommended Circulator Models for Alpine Boilers and Alliance SL Indirect Water Heaters
Installed as Part of Near-Boiler Piping Up to 75 Ft. Equivalent Length - Domestic Hot Water Circulator
Boiler
Model
Boiler
Supply
Connection,
Inch, FPT
Boiler
Return
Connection,
Inch, FPT
Near-
Boiler
Piping
Supply
Pipe
Size,
Inch
Near-
Boiler
Piping
Return
Pipe
Size,
Inch
Max
Allowable
Flow
through
Boiler,
GPM @
20°F DT
Flow,
GPM
@ 25°F
DT
Min
Req’d
Flow
through
Boiler,
GPM
@ 35°F
DT
Alliance
SL
Models
to be
installed
As Part of
Near-
Boiler
Piping
Alliance
SL
Coil
Required
Flow
Rate,
GPM
Alliance
SL Coil
Head
Loss,
Ft @
Required
Flow
Rate
Combined
Boiler,
Alliance
SL &
Piping
Loop
Head
Loss, Ft
*Recommended
Circulator Make
& Model for
Alliance SL
installed as Part
of Near-Boiler
Piping
Reference
Figure
Notes
ALP210B
1
1
1-1/4
1-1/4
19.4
15.5
11.1
SL27
6
9
NA
Not
Recommended
25B
Note 2
SL35
6
9
SL50
6
9.5
SL70
6
10
SL119
14
17
29.7
Taco 1400-45
Grundfos UPS
32-80/2 (max
speed)
25B
ALP285B
1-1/4
1-1/4
1-1/2
1-1/2
26.5
21.2
15.1
SL27
6
9
NA
Not
Recommended
25B
Note 2
SL35
6
9
SL50
6
9.5
SL70
6
10
SL119
14
17.0
27.0
Taco 1400-45
Grundfos UPS
32-80/2 (max
speed)
25B
Note 3
NOTES:
Note 1: Required Alliance SL Coil Flow Rate exceeds Max Allowable Flow Rate through Boiler; this Boiler/Alliance SL combination may result in boiler heat
exchanger erosion and noise.
Note 2: Required Alliance SL Coil Flow Rate is below Min Required Flow Rate through Boiler; this Model can only be installed as separate heating zone off
system header - see Figure 24A for alternate IWH
piping. Indirect Water Heater Circulator must be selected by an installer based on Alliance SL required coil flow and corresponding coil head loss
shown as well as total equivalent length of such
separate zone.
Note 3: Combined Head Loss shown corresponds to Min Required Flow Rate through Boiler.
* Circulator Models shown are not equipped with internal flow check valve (IFC).
When selecting Circulators with IFC contact Circulator Manufacturer for sizing information.
Near-Boiler Piping Size shown is based on 2 to 5.5 Ft/sec velocity range to avoid potential noise and pipe erosion.
VI. Water Piping and Trim
(continued)
Summary of Contents for Alpine ALP080B
Page 76: ...76 103448 10 6 18 VIII Electrical continued...
Page 77: ...103448 10 6 18 77 VIII Electrical continued Figure 27 Wiring Connection Diagram...
Page 78: ...78 103448 10 6 18 Figure 28 Ladder Diagram VIII Electrical continued...
Page 146: ...146 103448 10 6 18...
Page 147: ...103448 10 6 18 147...