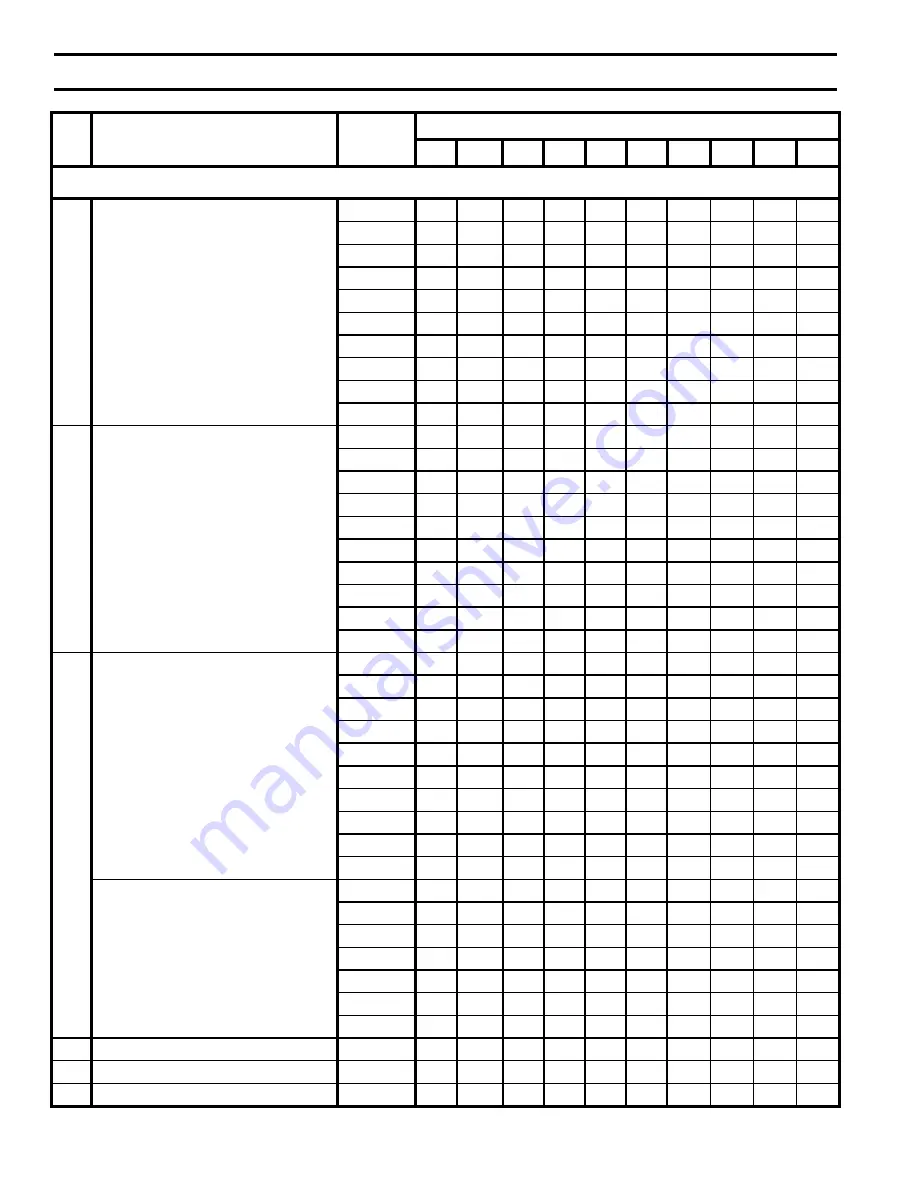
54
Key
No.
Description
Part No.
Quantity
IN3I IN4I IN5I IN6I IN7I IN8I IN9I IN10 IN11 IN12
3. Base Assembly (Continued)
3B2
Base Rear Insulation
72060035
1
---
---
---
---
---
---
---
---
---
72060045
---
1
---
---
---
---
---
---
---
---
72060055
---
---
1
---
---
---
---
---
---
---
72060065
---
---
---
1
---
---
---
---
---
---
72060075
---
---
---
---
1
---
---
---
---
---
72060085
---
---
---
---
---
1
---
---
---
---
72060095
---
---
---
---
---
---
1
---
---
---
72060105
---
---
---
---
---
---
---
1
---
---
72060115
---
---
---
---
---
---
---
---
1
---
72060126
---
---
---
---
---
---
---
---
---
1
3C
Base Front Panel Assembly
618600341
1
---
---
---
---
---
---
---
---
---
618600441
---
1
---
---
---
---
---
---
---
---
618600541
---
---
1
---
---
---
---
---
---
---
618600641
---
---
---
1
---
---
---
---
---
---
618600741
---
---
---
---
1
---
---
---
---
---
618600841
---
---
---
---
---
1
---
---
---
---
618600941
---
---
---
---
---
---
1
---
---
---
618601041
---
---
---
---
---
---
---
1
---
---
618601141
---
---
---
---
---
---
---
---
1
---
618601241
---
---
---
---
---
---
---
---
---
1
3D
Burner Tray (1 Inch Main Burners)
718600305
1
---
---
---
---
---
---
---
---
---
718600405
---
1
---
---
---
---
---
---
---
---
718600505
---
---
1
---
---
---
---
---
---
---
718600605
---
---
---
1
---
---
---
---
---
---
718600705
---
---
---
---
1
---
---
---
---
---
718600805
---
---
---
---
---
1
---
---
---
---
718600905
---
---
---
---
---
---
1
---
---
---
718601005
---
---
---
---
---
---
---
1
---
---
718601105
---
---
---
---
---
---
---
---
1
---
718601205
---
---
---
---
---
---
---
---
---
1
Burner Tray (40mm Main Burners)
71806037
1
---
---
---
---
---
---
---
---
---
71806047
---
1
---
---
---
---
---
---
---
---
71806057
---
---
1
---
---
---
---
---
---
---
71806067
---
---
---
1
---
---
---
---
---
---
71806077
---
---
---
---
1
---
---
---
---
---
718600806
---
---
---
---
---
1
---
---
---
---
718600906
---
---
---
---
---
---
1
---
---
---
3E
Base Leg Assembly
6186001
4
4
4
4
4
4
4
4
6
6
3E1 Base Leg [Included in Key No. 3E]
71860021
4
4
4
4
4
4
4
4
6
6
3E2 Nylon Glide [Included in Key No. 3E]
8186006
4
4
4
4
4
4
4
4
6
6
XI. Repair Parts (continued)
Summary of Contents for INDEPENDENCE
Page 4: ...4 Figure 1 Dimensional Drawing...
Page 56: ...56 Manifold and 1 Main Burners XI Repair Parts continued...
Page 62: ...62 XI Repair Parts continued...
Page 64: ...64 XI Repair Parts continued...
Page 72: ...72 U S Boiler Company Inc P O Box 3020 Lancaster PA 17604 1 888 432 8887 www usboiler net...