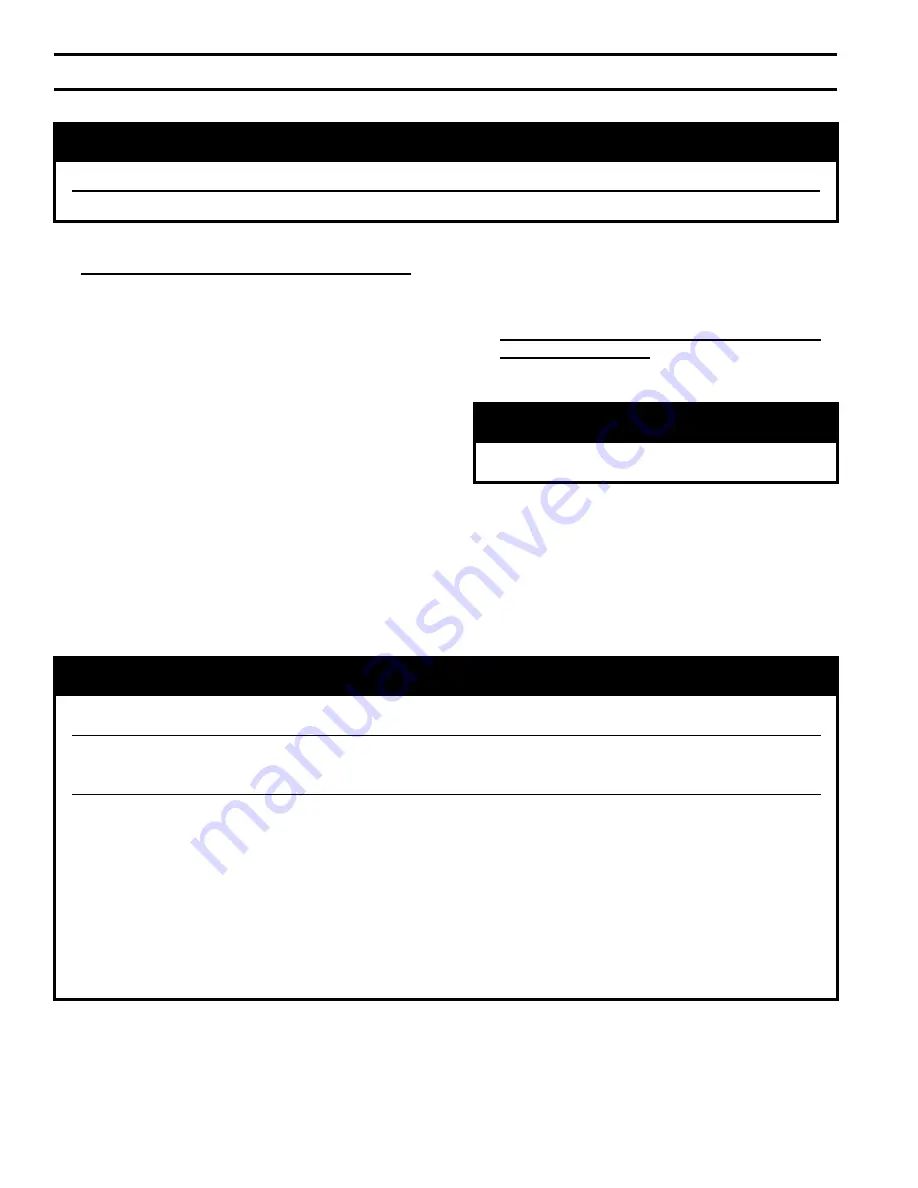
A.
EVALUATE THE ExISTING STEAM SYSTEM.
The single most important factor in determining the
expected life cycle of a steam boiler, is the amount of
fresh water added to the boiler during operation. Fresh
water brings minerals and oxygen into the boiler. These
contaminants greatly accelerate corrosion of the cast
iron boiler sections.
1. Assure that all system radiators, piping and vents are
absolutely leak tight.
a. When a steam boiler is installed in an existing
system, ALL air vents should be replaced at the
same time. This assures that the new boiler will
not be compromised by existing system leaks.
b. If the system contains hidden supply or return
piping (hidden behind walls, buried in concrete,
etc.) pressure test this piping to assure there are
no leaks.
SECTION III: STEAM BOILER PIPING & TRIM
2. Repair any leaks in the system.
3. Install accurate water meter on the fresh water
supply to the boiler.
B. CONNECT SYSTEM SUPPLY AND RETURN
PIPING TO BOILER.
See Figure 12 for piping
details. Also consult I=B=R Installation and Piping
Guides.
CAUTION
Maintain minimum ½ inch clearance from hot
water piping to combustible materials.
WARNING
Failure to properly pipe boiler may result in improper operation and damage to boiler or structure.
Do not increase steam boiler input above the ratings.
NOTICE
Do not use softened water in steam boilers. Accelerated boiler corrosion will result. Tie in fresh water
supply to the boiler upstream of a water softener.
Oxygen contamination of boiler water will cause corrosion of iron and steel boiler components, and can
lead to boiler failure. U.S. Boiler Company's Standard Warranty does not cover problems caused by
oxygen contamination of boiler water or scale (lime) build-up caused by frequent addition of water.
Before using copper for steam piping, consider the following characteristics of copper piping:
1) high coefficient of thermal expansion can induce mechanical stresses and cause expansion/
contraction noises if not accounted for in the piping system design and installation,
) high heat transfer rate (heat loss) of uninsulated copper piping must be included in the normal
piping and pickup factors used to size the boiler,
3) soldering or brazing pastes and fluxes that end up in the system can cause poor heat transfer,
surging, an unsteady water line and wet steam if not thoroughly removed during the boil out
procedure and,
) galvanic corrosion of the adjoining metal may occur due to dissimilar metals in certain water
chemistries if dielectric unions are not used.
Summary of Contents for MegaSteam MST
Page 5: ...Figure 1 MST288 Thru MST629 Steam Boiler with and without Tankless Heater Beckett Burner Shown...
Page 11: ...11 Figure 4 Boiler Removal from Skid SECTION II UNIT PAK BOILER ASSEMBLY continued...
Page 34: ...34 Figure 18 Wiring Diagram Steam Hydrolevel CG450 Probe LWCO SECTION VI ELECTRICAL continued...
Page 58: ...58 Bare Boiler Assembly SECTION XII Repair Parts continued...
Page 60: ...60 Jacket Assembly SECTION XII Repair Parts continued...
Page 62: ...62 MST288 Thru MST629 Steam Boilers Trim and Controls SECTION XII Repair Parts continued...
Page 64: ...64 Beckett AFG Burner SECTION XII Repair Parts continued...