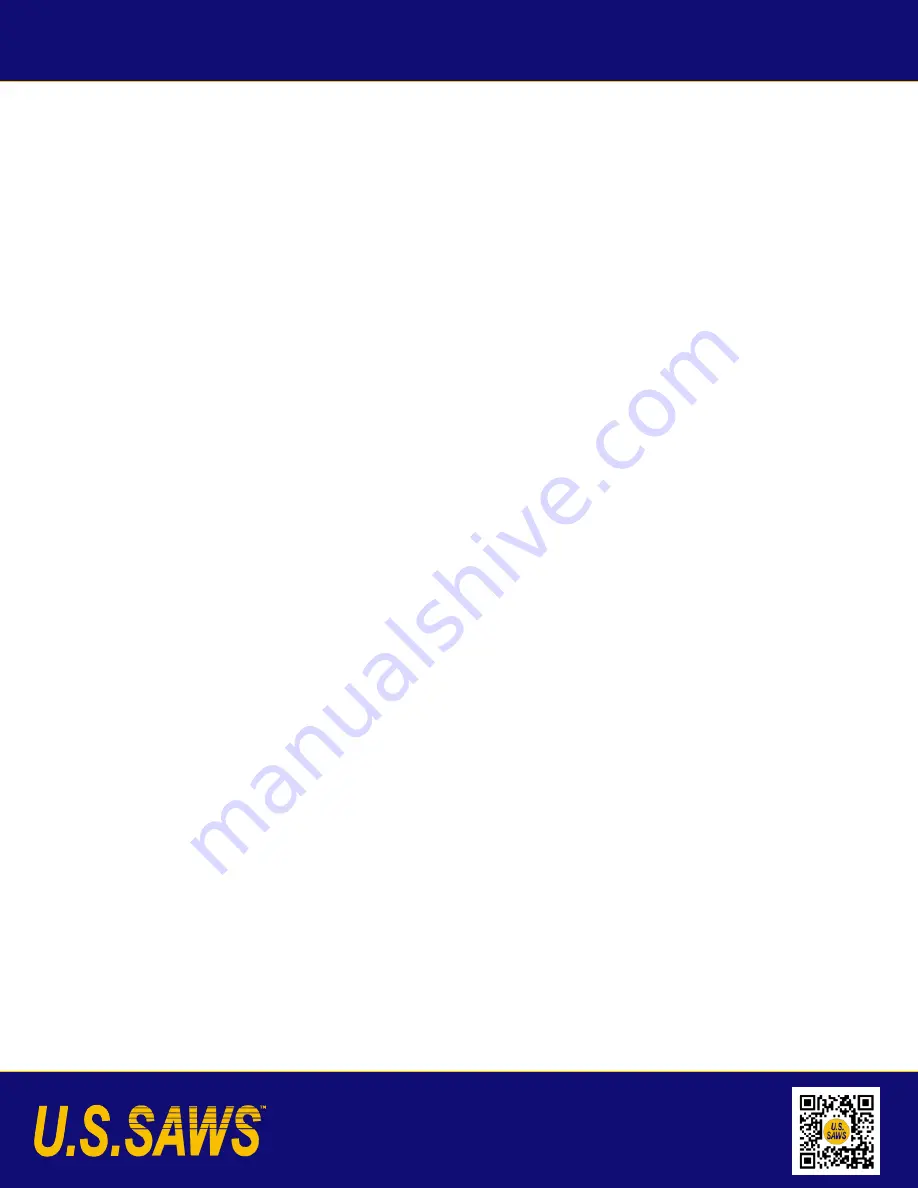
O P E R AT I O N
6.16
Open Joint: With an un-filled control joint where it only needs to
be cleaned of debris, it is better to line the pointer up with the left edge of
the joint so that the pointer wheel rides along on the surface of the floor.
If the pointer wheel is directly in the joint, it can get stuck and make it dif-
ficult to move the machine forward.
6.17
Filled Joint: The pointer wheel can be lined up directly in the cen-
ter of the joint or off to the side edge. It is up to the operator to determine
what they are more comfortable with.
6.18
Adjusting the pointer: Part # 49 in the parts breakdown is a
“shaft collar clamp.” To adjust the pointer, loosen the allen bolt, rotate the
shaft collar clamp forward to move the pointer to the right, and rotate it
backward to move the pointer to the left. Once the pointer wheel is in the
desired position, re-tighten the allen bolt. One of the easiest ways to set
the pointer is, with the saw off, put the blade down into a joint and move
the saw back and forth a few feet while observing where the pointer wheel
is in conjunction to the joint. This will show if the pointer is in a good loca-
tion or if it needs adjustment.
6.19
Open Joint: Lower the blade to the desired depth into the open
joint with the saw “off.” Move the saw forward and backward to align the
blade with the joint. Carefully, and without moving the position of the
saw, raise the blade just above the surface. With the other hand, turn the
saw on and lock the trigger. Slowly lower the blade into the joint. Once
the blade is at it’s full depth, use two hands and guide the saw through
the joint. The blade will follow the path of least resistance and therefore
follow the joint with minimal effort. Tip: There may be some dust escaping
through the front of the joint upon entry or if the joint is relatively clean
to begin with. If this is the case and total dust control is necessary, it
may be helpful to sweep some dry sand into the joint before running the
saw through it. The sand will block the dust and direct it upward into the
vacuum port and the blade will easily remove the sand.
6.20
Filled Joint: Line the blade up with the joint fill material to be
removed, turn the saw on, and slowly lower the blade into the cut. The
saw will be forced back toward the operator until the blade is at full depth.
Do not force the saw forward. Let the rpm of the saw stay high and let the
blade do the cutting. Forcing the blade will cause excessive heat and may
make cutting slower. The saw must be guided in an accurate and skillful
manner as to keep the saw in the joint fill material and not wander off into
the concrete. This is especially important when removing polyurea.
6.21
Finishing a cut: When the operator gets to a wall or other termi-
nation point, with the blade still in the “down” position, shut the saw off
and wait for the blade to stop. Retract the blade and move to the next cut
and repeat the process. It is not recommended to tip the saw back on it’s
rear wheels while the saw is still on and the blade is spinning. This is espe-
cially important on polished concrete floors to prevent accidental damage
to the floor surface.
10
6.22
Align bolt holes for Dust Buggy Arm in the most vertical position.
Make sure the Adjustment Lever is in position.
6.23
Attach both 3/8”-16 bolts.
6.24
Attach Clamp Plate.
6.25
Attach 3/8” washers and tighten Lock nuts firmly.
6.26
Attach 3/8” Shoulder Bolt through Adjustment lever and spacer.
Then tighten firmly to motor plate.
6.27
Use the shortest, heaviest gauge extension cord possible for
your job. The longer the cord, the more power will be lost. The
thinner the cord, the more heat will be generated and will even
tually end up damaging the motor.
6.28
Keep the machine clean.
6.29
Don’t get the machine wet
6.30
Clean dust out of the threads of the blade nuts before
tightening.
6.31
Periodically check nuts and bolts for tightness
6.32
Familiarize yourself and your employees with the machine and
it’s intended manner of use before using it.
6.33
Bring a variety of thickness of blade with you to every job.
6.34
Bring a good set of tools to every job.
Surface Prep
Division
P: 877-817- 6687 F: 813-621-7125
Visit us at www.ussaws.com
sales@ussaws.com
LINING UP THE BLADE WITH THE JOINT/POINTER ADJUSTMENT
OPERATING THE SAW:
OTHER INFORMATION: