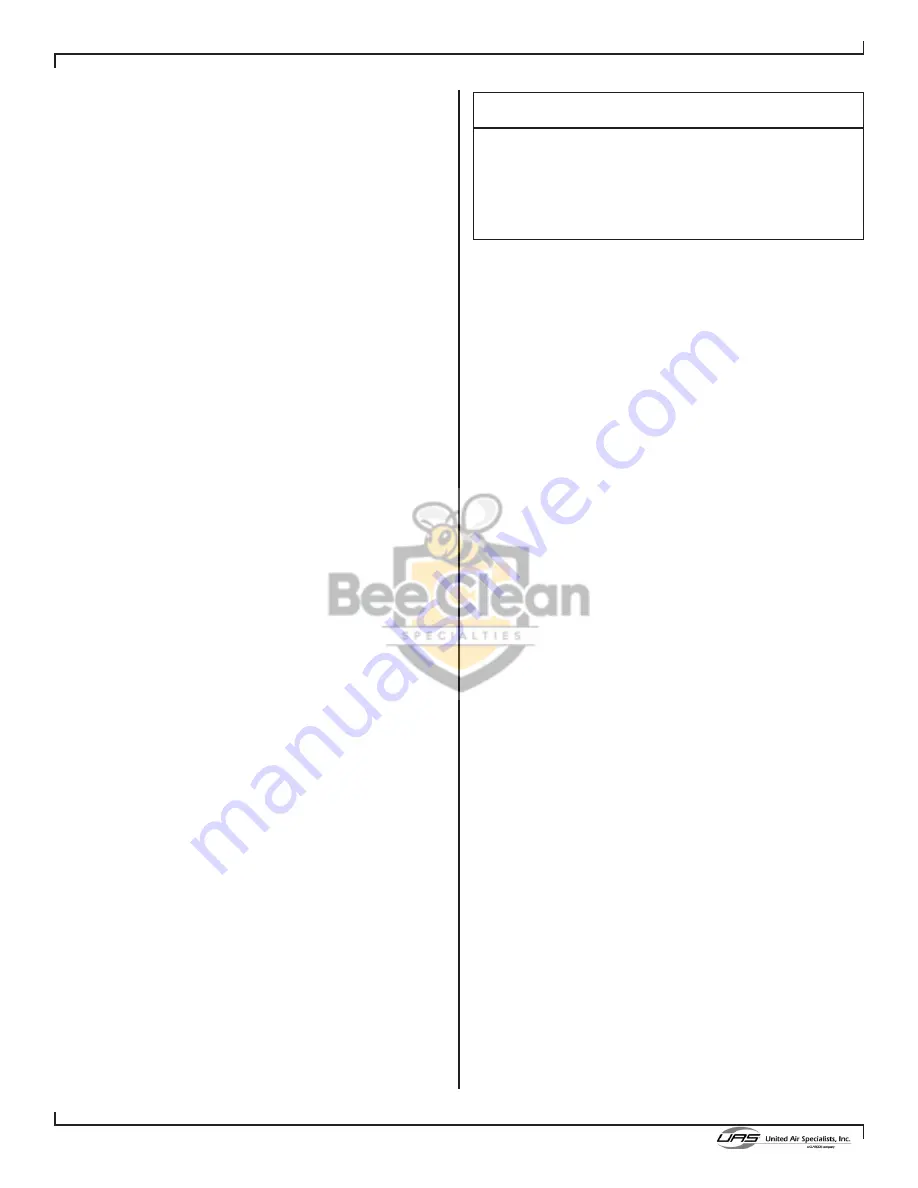
10
revised 09/09
Smog-Hog
SG Series Model
6.1.3 PERFORM IN PLACE CLEANING
If the SG is equipped with In Place Cleaning a daily
wash cycle is required refer to In Place Cleaning
Owner’s Manual and Sequence of Operation
instructions. a typical seven day wash cycle would be
six day waterwash without detergent with the seven
day a detergent wash. The detergent wash frequency
can be increased up to everyday. the auto wash cycle
is initiated by a uaS time clock, with the wash cycle
sequencing, wash cycle times, and detergent frequency
through the uaS Main electrical Panel. a wash
cycle can be manually initiated, identical operation
as the auto wash cycle, for an additional wash cycle.
a wash cycle whether a manual or by time clock can
only be initiated with the SG off line. the wash cycle
frequency could be increased or decreased depending
on visual inspection of the components and high
voltage measurements. When the SG is placed on
line after a wash cycle, the power pack enclosure(s)
indicator light(s) may intermittently or continuously blink
for approximately 60 minutes. If this condition exceeds
60 minutes, refer to Section 10 troubleshooting.
6.1.4 MANUALLY CLEANING COMPONENTS,
CABINET AND OTHER EQUIPMENT AS REQUIRED.
the unit components should be manually cleaned one
to three month interval depending upon application/high
voltage measurements refer to Section 6.2.
6.2 MANUAL CLEANING OF SMOG-HOG
COMPONENTS
there are a number of methods for manual cleaning,
certain key cleaning criteria contribute to the
effectiveness of every method. these include the type
of detergent, detergent strength, water temperature,
agitation/ impingement, duration, rinse procedure and
dry-out time.
6.2.1 TYPE OF DETERGENT
in general, the detergent used on most hydrocarbons
(e.g., oily residues) will be alkaline in nature. it is
extremely important that the detergent have a built-in
buffering agent to reduce aluminum deterioration.
6.2.2 DETERGENT STRENGTH
Detergent concentration in a mixture with water varies
with the application from 1:1 to 20:1 parts water to parts
detergent. for any contaminant condition, the best
course is to use a cleaning solution per the detergent
manufacturer’s directions. More or less detergent
may eventually be required for effective cleaning at
reasonable detergent cost. the recommended factory
detergent concentration is 5% (20:1).
CAUTION
Never mix caustic and alkaline detergents for
manual or in-place cleaning. Detergent mixing
could cause rapid heat release, gel formation
or some other undesirable condition. Complete
purging of system piping is necessary when
changing detergents.
6.2.3 WATER TEMPERATURE
Detergents can be up to twice as effective in hot water.
Hot water alone is very effective in softening built-up
residue. Water temperature should be 140°F to 170°F,
not to exceed 180°F.
6.2.4 AGITATION/IMPINGEMENT
these methods are virtually the same, with
impingement being the most extreme form of agitation.
Any liquid movement over built-up residue will remove
a layer, allowing detergent to work on the next layer. A
reduction in cleaning time duration usually results.
6.2.5 CLEANING CYCLE DURATION
In most cleaning methods, adequate time should be
allowed for the detergent to remove the contaminant
thoroughly. reaction time will vary depending on
detergent strength, temperature and agitation.
Guidelines for mixing, heating and expected results are
included on specification sheets for most detergents.
time is necessary for effective cleaning. Soaking may
seem slower and less effective than high impingement
and/or hot water above 180°F for cleaning action, so
personnel should be forewarned about using excessive
pressure or temperature to shortcut the cleaning
process. High pressure or stream spray cleaning until
plate edges are shiny is not effective. not only will
penetration to the cell core not occur, but warping and
bending of the plates may result as well. Patience and
thoroughness of cleaning best preserve the integrity of
the components in the long term. Soaking and gentle
rinsing provides for best results.
6.2.6 RINSE PROCEDURE
Cleaned components should be rinsed off quickly and
thoroughly to remove remaining contaminants. Some
detergent residue will remain if rinsing is not performed.
the residue may contribute to voltage bleed-down when
the unicell is placed in operation. also, even though the
detergent is “buffered” prolonged contact could cause
minor corrosion. Hot water should be used for rinsing.