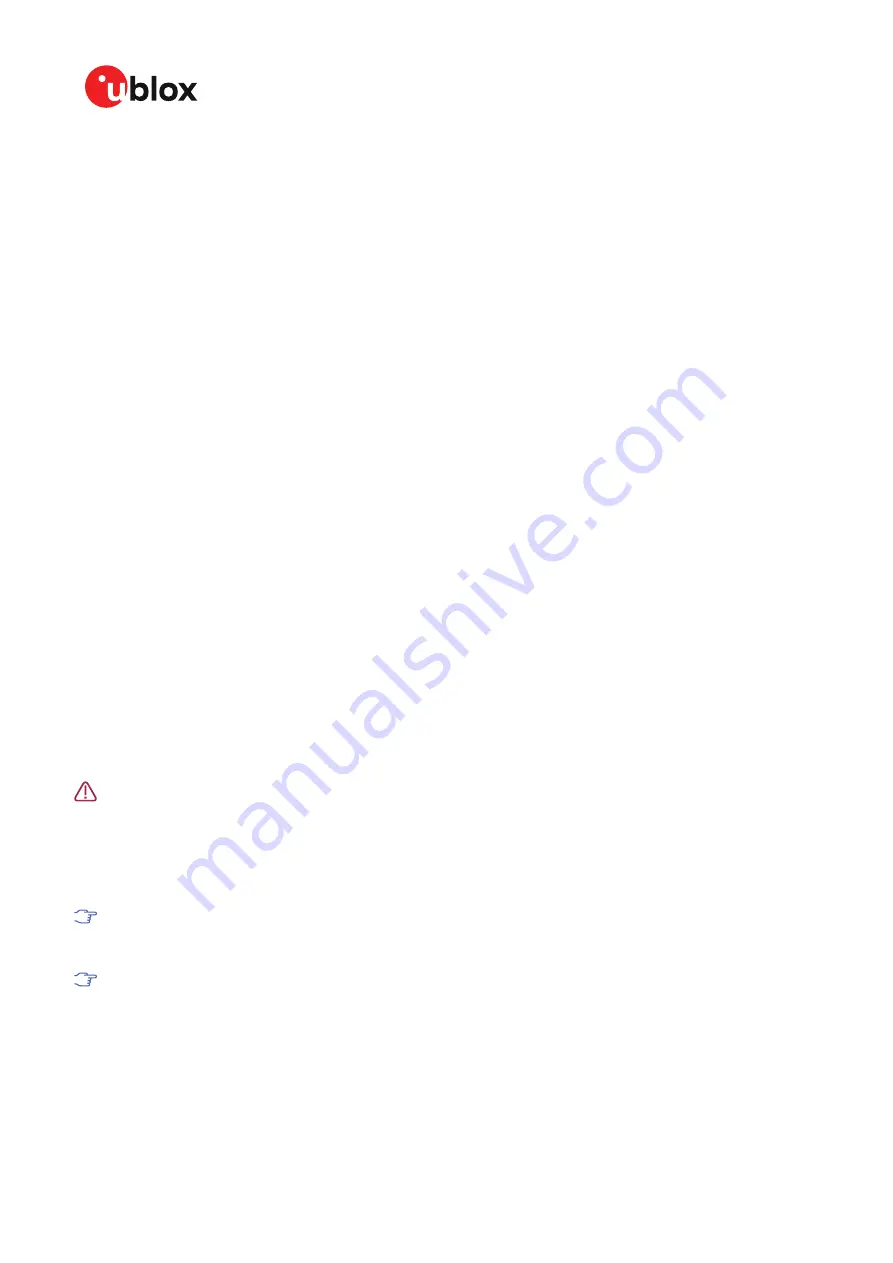
NEO-D9S - Integration manual
4.7 Layout
This section details layout and placement requirements of the u-blox D9 correction data receiver.
4.7.1 Placement
L-band signals at the surface of the Earth are below the thermal noise floor. A very important
factor in achieving maximum GNSS performance is the placement of the receiver on the PCB. The
placement used may affect RF signal loss from antenna to receiver input and enable interference
into the sensitive parts of the receiver chain, including the antenna itself. When defining a GNSS
receiver layout, the placement of the antenna with respect to the receiver, as well as grounding,
shielding and interference from other digital devices are crucial issues and need to be considered
very carefully.
Signal loss on the RF connection from antenna to receiver input must be minimized as much as
possible. Hence, the connection to the antenna must be kept as short as possible.
Ensure that RF critical circuits are clearly separated from any other digital circuits on the system
board. To achieve this, position the receiver digital part closer to the digital section of the system
PCB and have the RF section and antenna placed as far as possible away from the other digital
circuits on the board.
A proper GND concept shall be followed: The RF section shall not be subject to noisy digital supply
currents running through its GND plane.
4.7.2 Thermal management
During design-in do not place the receiver near sources of heating or cooling. The receiver oscillator
is sensitive to sudden changes in ambient temperature which can adversely impact satellite signal
tracking. Sources can include co-located power devices, cooling fans or thermal conduction via the
PCB. Take into account the following questions when designing in the receiver.
• Is the receiver placed away from heat sources?
• Is the receiver placed away from air-cooling sources?
• Is the receiver shielded by a cover/case to prevent the effects of air currents and rapid
environmental temperature changes?
High temperature drift and air vents can affect the GNSS performance. For best
performance, avoid high temperature drift and air vents near the receiver.
4.7.3 Package footprint, copper and paste mask
Copper and solder mask dimensioning recommendations for the NEO-D9S module packages are
provided in this section.
The module edge pads are 0.8 mm x 0.9 mm. Implement a pad size on your PCB as a copper
pad size of 0.8 mm x 1.8 mm. Solder mask for the same pad is 0.9 mm x 1.9 mm. Paste
mask for the same pad is 0.8 mm x 2.1 mm.
These are recommendations only and not specifications. Consider the paste mask outline
when defining the minimal distance to the next component. The exact copper, solder and
paste mask geometries, distances, stencil thickness and solder paste volumes must be
adapted to the specific production processes (e.g. soldering etc.) of the customer.
UBX-19026111 - R07
4 Design
Page 34 of 52
C1-Public