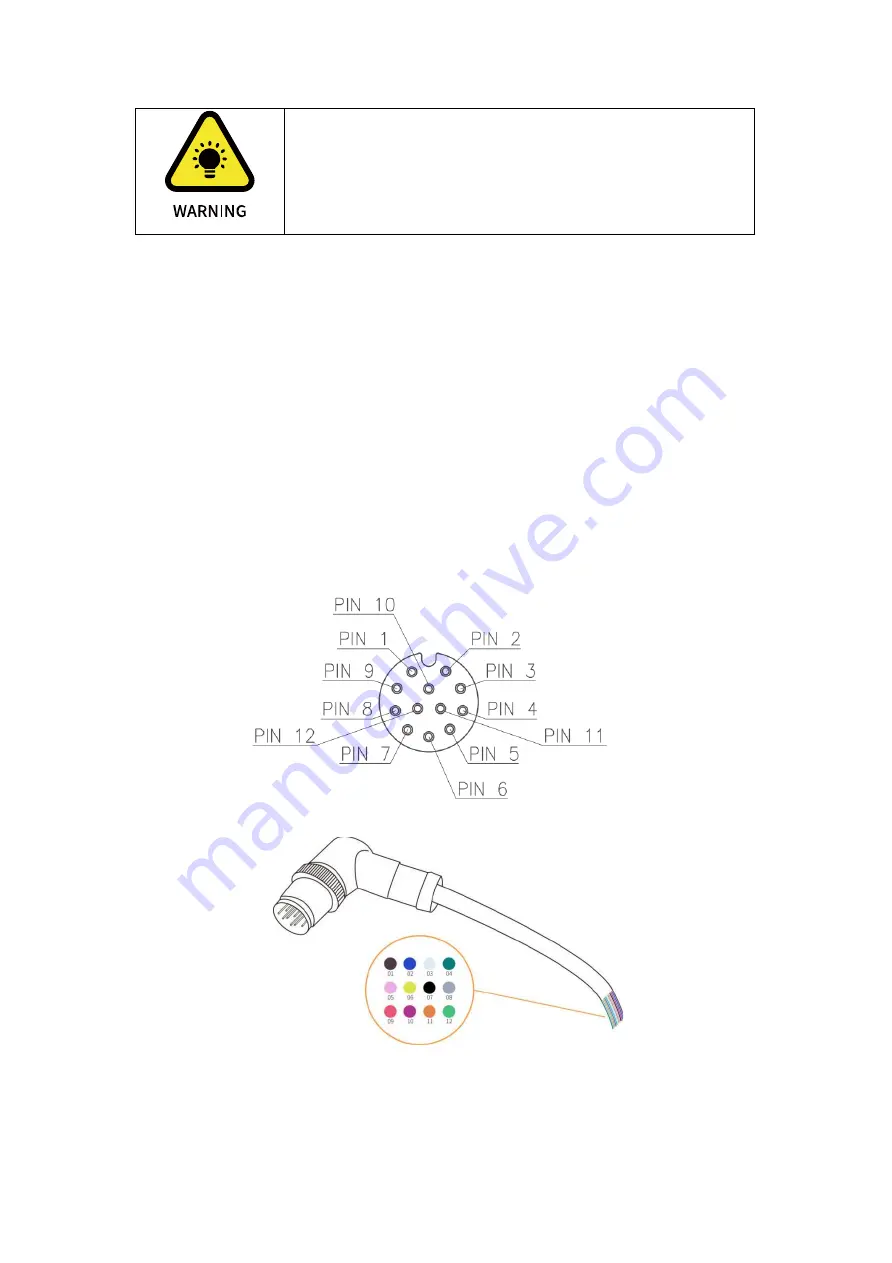
44
1.
When wiring the electrical interface of the Control
Box, the Control Box must be powered off.
2.4.
End-Effector I/O
At the tool side of the robotic arm, there is an avionic socket 12-pin
female industrial connector. This connector provides power and control
signals for the grippers and sensors used on a particular robotic arm
tool. Please refer to the figure below: