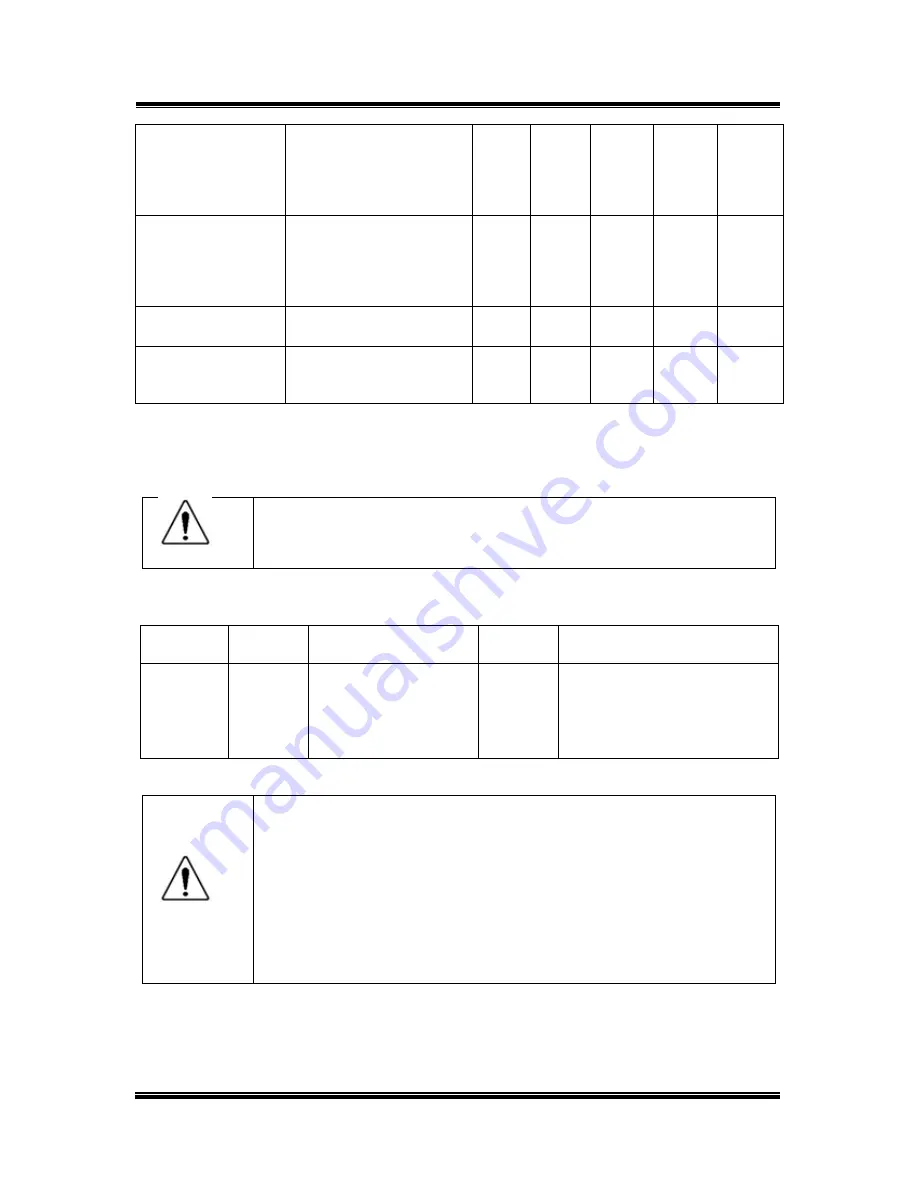
UI Robot Technology Co. Ltd.
M4220161122CN
Page 61
UI
– SR Series User Manual
Gently shake the
cable by hand to
confirm whether
there is
disconnection
External cable(including
cable units of robot)
√
√
Press each arm by
hand in power-on
state to confirm
whether there is
rocking
Joints
√
Check for abnormal
sound and vibration
Overall
√
√
√
√
√
use gauge to
measure
repeatability
Overall
√
2.3 Grease Filling
Ball screw splines require periodic greasing. Be sure to use the specified grease.
注
意
★
Please pay attention to avoid grease running out. If the grease is used
up, the sliding part may cause scratches and the like, and not only can
it not perform well, but the repair will take a lot of time and expense.
Part
Period
Grease
Method of grease filling
The third
joint
Ball
screw
splines
shaft
After moving 50km
for the first time,
then move each
100km
LUBE
6.0 ball screw splines unit
注
意
★
Once grease into eyes, mouth or adhension to skin, please carry out
the following treatment.
Into eyes: Please wash your eyes thoroughly with water, and then go
to see a doctor.
Into mouth: Do not force vomiting when swallowing, should
immediately go to see a doctor
When mouth is greased, please rinse your mouth
thoroughly with water.
Adhenring to the skin: please wash with water and soap.
2.4 Fastening of hexagon socket head bolts
Use the hexagon socket head bolts (hereinafter simply “bolts” for short) where mechanical
strength is required. When assembling, tighten the bolts follow the tightening torques shown