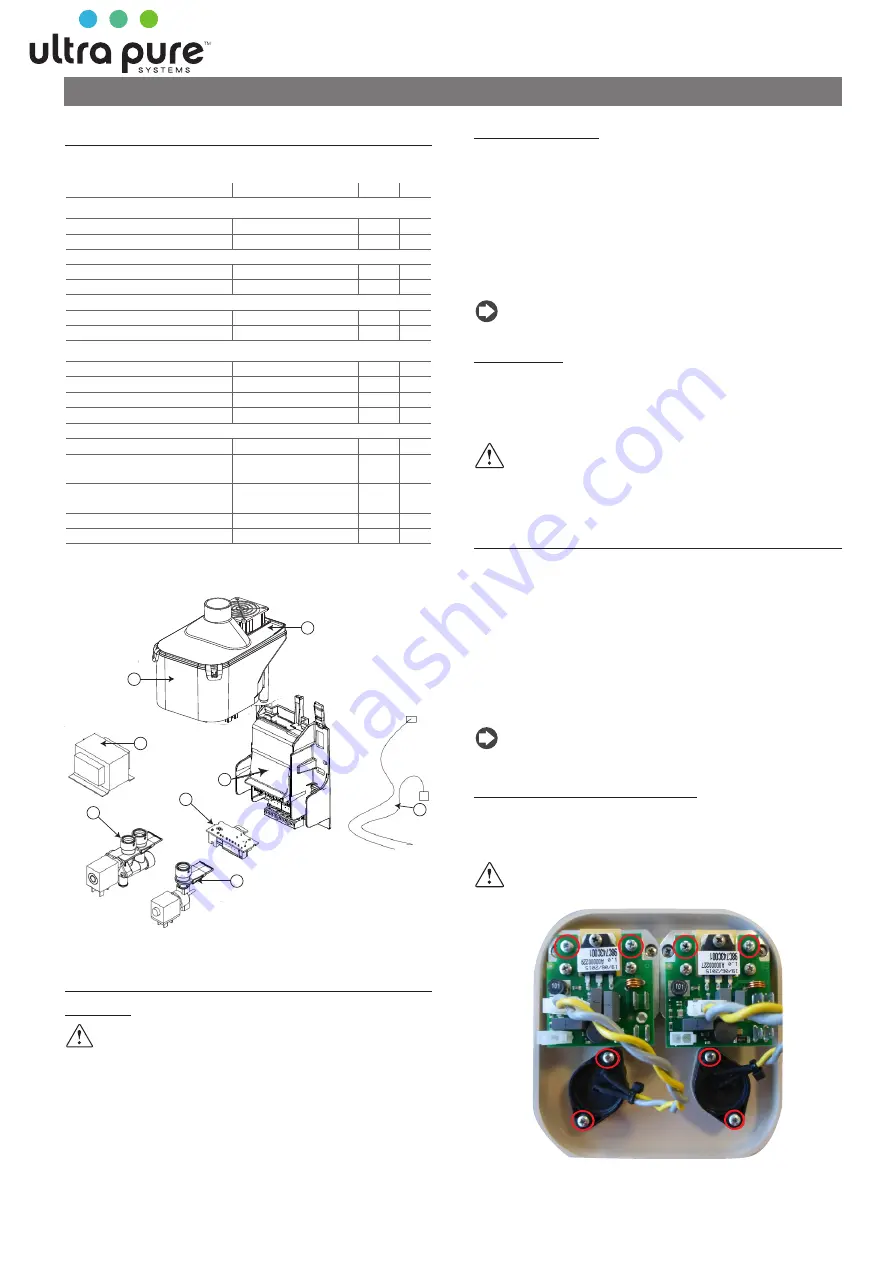
16
9. MAINTENANCE AND SPARE PARTS
9.1 Spare parts
Table of water circuit, electrical and electronic spare part numbers
part number
pos.
fig.
Water circuit
Fill solenoid valve kit
UP_P_0558
F
9.a
Drain solenoid valve kit
UP_P_0559
E
9.a
Water circuit (UP01)
Tank complete
UP_P_0560_1
B
9.a
Cover with fan and level sensor
UP_P_0561_1
L
9.a
Water circuit (UP02)
Tank complete
UP_P_0562_2
B
9.a
Cover with fan and level sensor
UP_P_0563_2
L
9.a
Electrical and electronic parts
Main electronic board
UP_P_0560
D
9.a
Main board + auxiliary card
UP_P_0561
D + H 9.a
Driver
UP_P_0562
Transducer TDK
UP_P_0563
Electrical parts -
(UP01 - UP02)
Power transformer:
115-24V
UP_P_0564
A
9.a
Power transformer:
115-50V
UP_P_0565
A
9.a
Cable Kit UU01F
UP_P_0566
G
9.a
Cable Kit UU01G
UP_P_0567
G
9.a
Tab. 9.a
B
L
A
E
H
D
F
G
Fig. 9.a
9.2 Tank cleaning and maintenance
Replacement
Important:
replacement must only be carried out by qualified
personnel, with the humidifier disconnected from the power supply.
In normal conditions, the
tank requires maintenance after one year
(or 1500/5000 operating hours respectively with mains/demineralised
water), or
if not used for an extended period
. Replacement is required
immediately – even before the scheduled period – should problems
occur (for example, when scale inside the tank prevents correct operation
of the piezoelectric transducers
).
Replacement procedure:
1.
switch the humidifier off (switch “0”), and open the mains disconnect
switch (safety procedure);
2.
disconnect the transducer power cable;
3.
release the tank (the two tabs at the rear) and lift it vertically to
remove it;
4.
clean or replace the transducers by removing the screws, see Fig. 9.b
(after replacement test water-tightness by filling the tank manually)
5.
reconnect the transducer power cables;
6.
reposition the tank;
7.
switch the humidifier on.
Note:
the tightening torque of the screws that fasten the transducer
must be 0.2ft-lb-0.03ft-lb.
Periodical checks
•
Every year
or no more than 1500/5000 operating hours respectively
with mains/DI water:
- clean the piezoelectric transducers
-
make sure the level sensor slides freely
Important
: in the event of water leaks, disconnect the humidifier
from the power supply and repair the leak
9.3 Cleaning and maintenance of other
components
•
Ultra Pure humidifers work best with DI water. Each trasnducer will
operate approx. 10,000hrs proportionally. If RO or City water is used,
transducers useful life is reduced proportionally
•
When cleaning plastic parts do not use detergents/solvents;
•
To replace the drivers and transducers, loosen the screws shown in the
figure with a screwdriver. Before applying the new driver , spread on
the back of the heat sink in contact with the tank, a layer of conductive
paste. The lack of the conductive paste may cause malfunctions. To
insert new transducers, observing the direction of insertion (
please,
pay attention to the print before removing the old one).
Note:
the tightening torque of the screws that fasten the transducer
must be 0.02ft-lb-0.03ft-lb.
Maintenance checks on other components:
□
fill solenoid valve. After having disconnected the cables and hoses,
remove the solenoid valve, check the inlet filter and clean if necessary,
using water and a soft brush.
Important
: after having replaced or checked the water circuit
components, make sure the connections are restored correctly.
Fig. 9.b