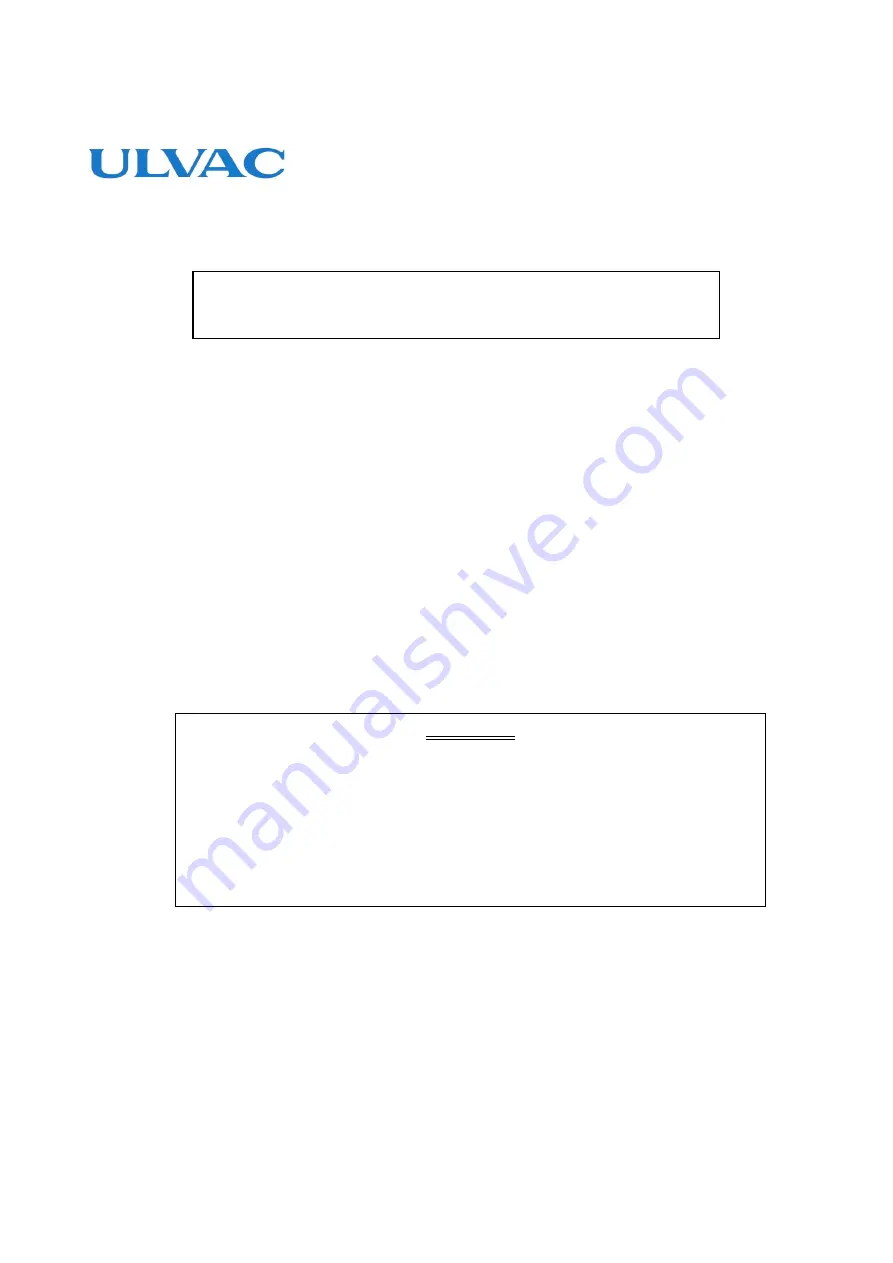
No
.
27500-2-01-7
Diaphragm Type Dry
Vacuum Pump
DA-41D, DA-81S
DA-41DK, DA-81SK
Indoor specification
Request
Please read this Instruction Manual before starting the pump in order to
use the pump effectively and safely. Please keep this Instruction Manual
carefully.
We reserve our right to change dimensions or specifications of the
motors described in this Instruction Manual for improvement of the
performance without prior notice.
ULVAC KIKO Inc.
Instruction Manual