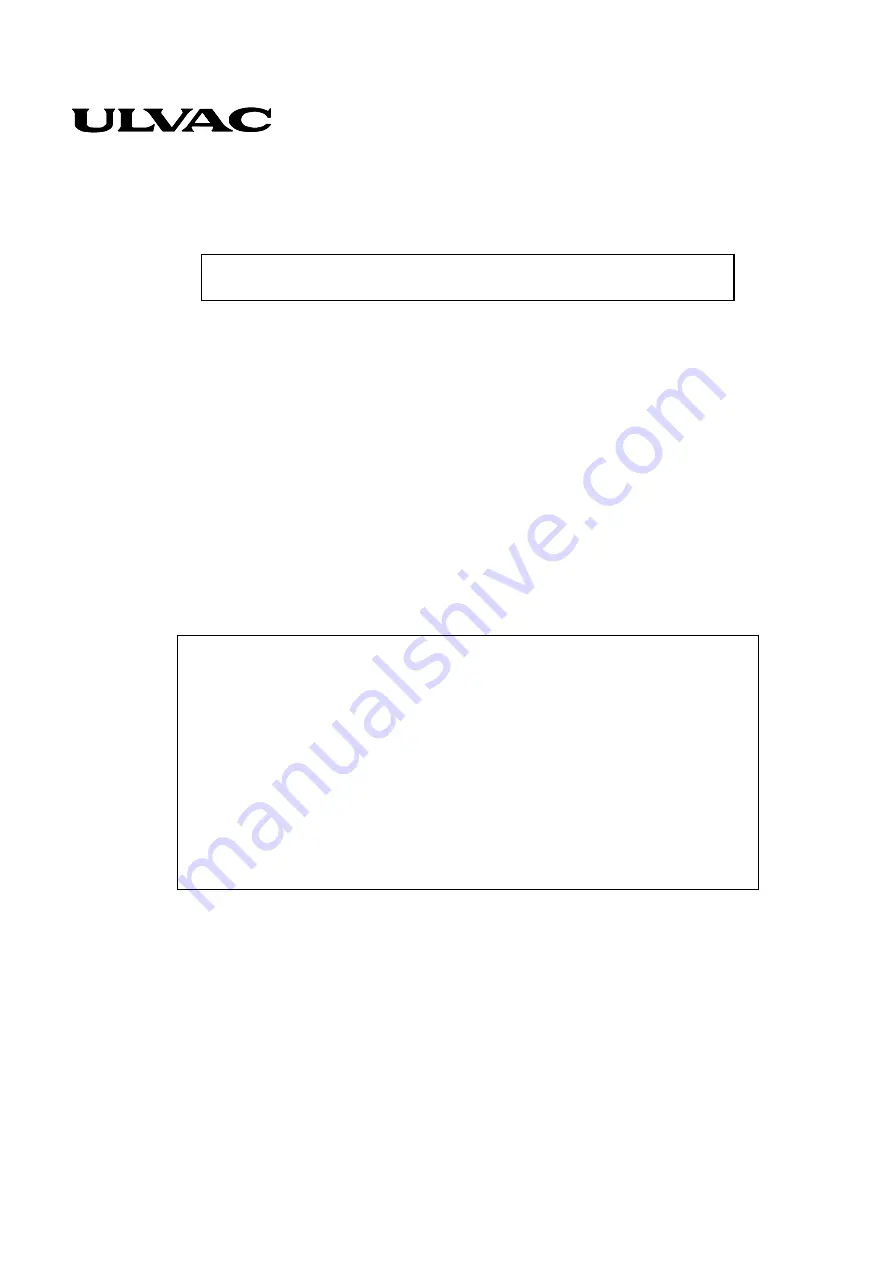
No. 21510-2-01-6
DIAPHRAGM DRY VACUUM PUMP
MODEL
DAT-50DEP, DAT-100SEP
Prior to use
For safe and efficient use of this pump, please read this
manual carefully before operation.
After reading the manual, keep it in your file for future
reference.
Specifications in this manual are subject to change without
notice due to future improvement.
ULVAC KIKO. Inc.
INSTRUCTION MANUAL