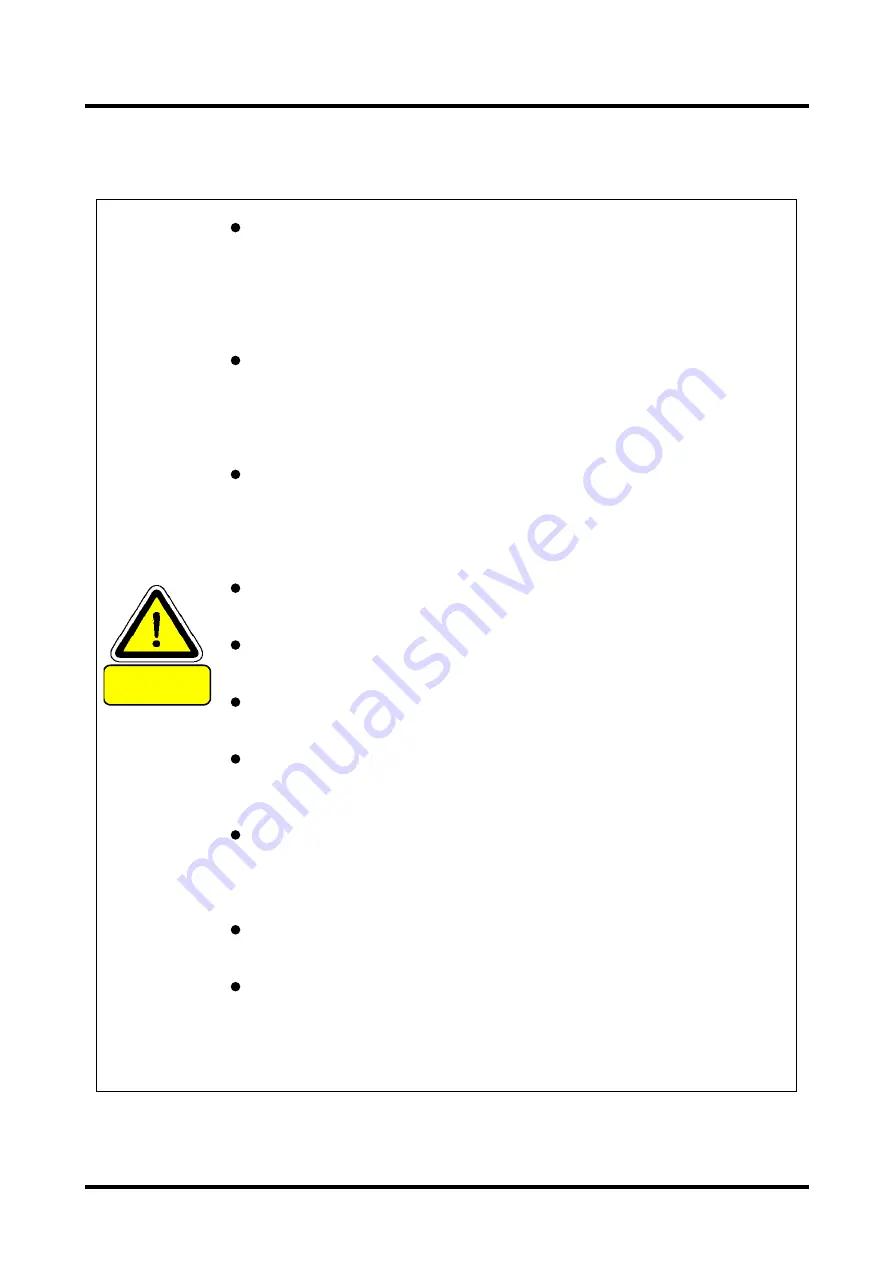
YK11-0016-DI-002-08
29
3.3 Inlet port Piping
CAUTION
Wash sufficiently inside the Vacuum chamber, pipes, Vacuum valve
and so on to connect them to the Pump. If dirty unit were connected,
it would cause a trouble such like raise the ultimate pressure or
extend the depression time to the specified pressure. Wear a pair of
gloves to touch any vacuum section. Do not touch with the bare
hand.
Pay a full attention to completely clear the welding scale and/or rust
inside the pipe. If obliged to conduct a welding work close to or on
the inlet, take a measure such as to remove the pump unit or put a
cover sheet on the inlet in order not to allow any foreign substance
enter inside.
Should the Pump sucked the water or substance such as dust,
powder and so on, it would impair the ultimate pressure and further
cause a trouble.
The pump has a really slight clearance to keep rotation and easily
gets impossible to rotate by any foreign substance entered inside.
Clear the sand completely after having sand blasted the vacuum
chamber.
Pay attention not to give damage to the Flange sheet face, Gasket
slot or gasket itself.
Check inside the casing before mounting the Pump unit to ensure
no dust is attached to the Rotor, casing or elsewhere.
Metal mesh on the Suction inlet is put to keep foreign substances
away from the Pump unit.
Be sure not to take it off unless necessitated so to check it.
Use a pipe having bellows between the Vacuum chamber and inlet
of the Mechanical Booster Pump so as
to avoid any direct load to the Pump flange
and not to transfer the pump vibration to the Vacuum chamber.
Put the Vacuum valve, Vacuum gauge and Leak valve between the
Vacuum chamber and the Pump
You should put the Leak valve closer as possible to the Vacuum
valve in order to prevent the oil from rising up to the Vacuum
chamber when the Pump stopped.
Be sure to mount the Leak valve above the Mechanical booster
pump.
Summary of Contents for PMB100D
Page 2: ......
Page 3: ...Declaration of Conformity...
Page 39: ...YK11 0016 DI 002 08 12 2 4 Dimensional drawing Fig 11 Dimensional drawing PMB100D...
Page 40: ...YK11 0016 DI 002 08 13 Fig 12 Dimensional drawing PMB300D...
Page 41: ...YK11 0016 DI 002 08 14 Fig 13 Dimensional drawing PMB600D...
Page 42: ...YK11 0016 DI 002 08 15 Fig 14 Dimensional drawing PMB1200D...
Page 43: ...YK11 0016 DI 002 08 16 Fig 15 Dimensional drawing PMB2400D...
Page 62: ...YK11 0016 DI 002 08 35...
Page 65: ...YK11 0016 DI 002 08 38...
Page 72: ...YK11 0016 DI 002 08 45...
Page 84: ...YK11 0016 DI 002 08 57 Fig 28 PMB300D Optional attachment figure...
Page 85: ...YK11 0016 DI 002 08 58 Fig 29 PMB600D Optional attachment figure...
Page 86: ...YK11 0016 DI 002 08 59 Fig 30 PMB1200D Optional attachment figure...
Page 89: ...YK11 0016 DI 002 08 62 Fig 33 Dimensional drawing PMB2400D Horizontal exhaust model...
Page 99: ...YK11 0016 DI 002 08 72...
Page 105: ...YK11 0016 DI 002 08 78...
Page 119: ......