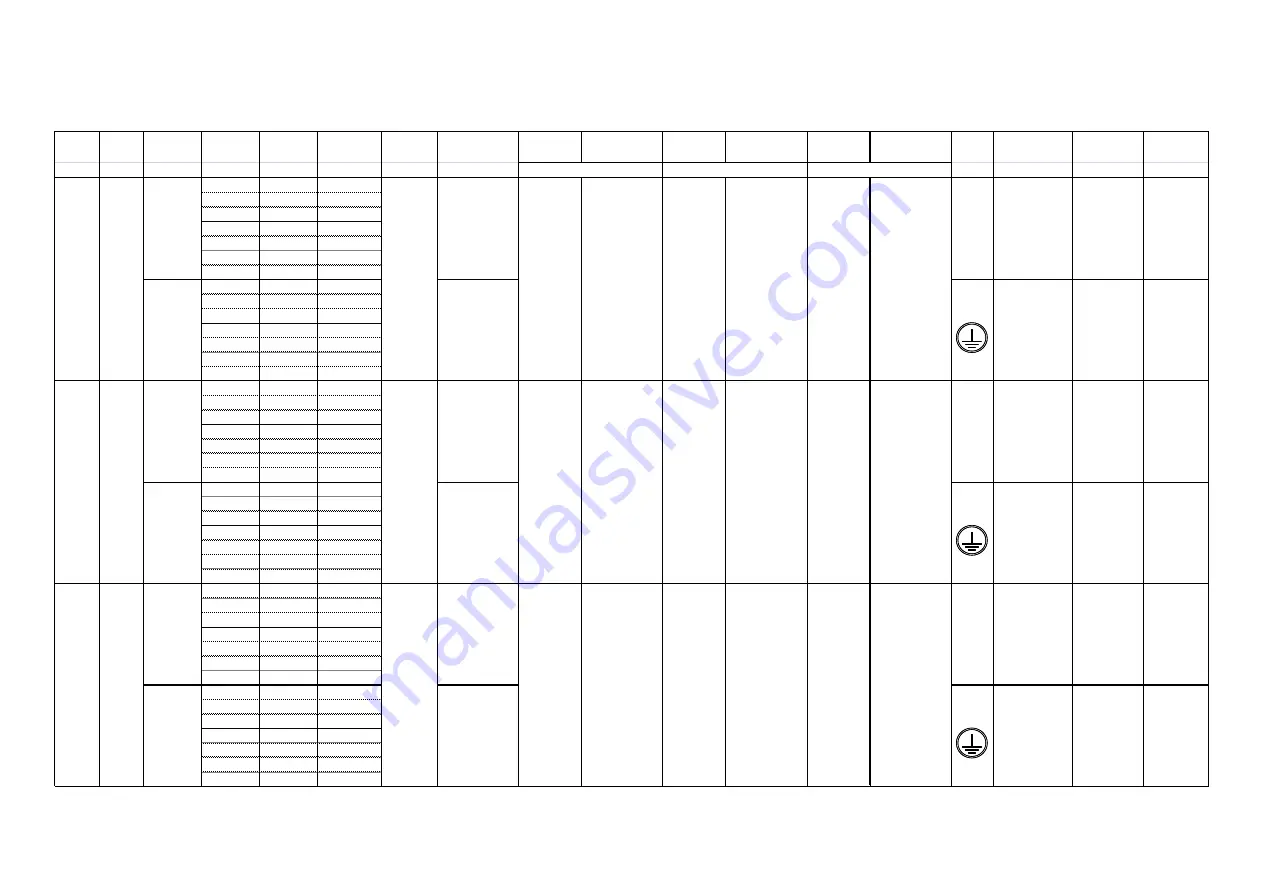
YK15-0009-DI-002-04
23
Table. 5 Rated current value of the standard motor
MODEL
MOTOR
the connection
inside the
terminal box
Voltage
Frequency
Rated Current
Breaker
cable
Recommended
Wire Gauge
Applicable
Wire Gauge
Recommended
Wire Gauge
Applicable
Wire Gauge
Recommended
Wire Gauge
Applicable
Wire Gauge
Terminal
Symbols
Terminal Screws
Tightening Torque
Solderless
Terminals
kw
V
Hz
A
A
Size・Form
N・m
JST Corporation
200
50
6.3
220
50
6.3
240
50
6.7
200
60
6.0
220
60
5.6
230
60
5.6
240
60
5.5
380
50
3.6
400
50
3.7
415
50
3.8
380
60
3.2
400
60
3.2
440
60
3.2
460
60
3.2
200
50
8.6
220
50
8.5
240
50
9.3
200
60
8.2
220
60
7.6
230
60
7.6
240
60
7.5
380
50
4.9
400
50
5.1
415
50
5.2
380
60
4.5
400
60
4.4
440
60
4.3
460
60
4.3
200
50
14.4
220
50
14.1
240
50
15.0
200
60
13.8
220
60
12.8
230
60
12.6
240
60
12.3
380
50
8.1
400
50
8.4
415
50
8.7
380
60
7.4
400
60
7.3
440
60
7.1
460
60
7.2
M5
Hexagon nut
2.0-2.5
R3.5-5
Y
(Star)
settinng < 100m
M6
Cross recessed
head screw
4.0-5.0
R3.5-6
3.5mm
2
-5.5mm
2
AWG12
AWG12-AWG10
4mm
2
4mm
2
-6mm
2
U1
V1
W1
VD90C
3.7
Δ
(Delta)
20
settinng < 30m
3.5mm
2
M4
Hexagon nut
1.2-1.5
R2-4
Y
(Star)
settinng < 85m
M5
Cross recessed
head screw
2.0-2.5
R2-5
2mm
2
-5.5mm
2
AWG14
AWG14-AWG10
2.5mm
2
2.5mm
2
-6mm
2
U1
V1
W1
VD60C
2.2
Δ
(Delta)
15
settinng < 30m
2mm
2
1.2-1.5
R2-4
Y
(Star)
settinng < 125m
M5
Cross recessed
head screw
2.0-2.5
R2-5
AWG14
AWG14-AWG10
2.5mm
2
2.5mm
2
-6mm
2
U1
V1
W1
M4
Hexagon nut
For Japan
For America
For Europe and China
VD30C
VD40C
1.5
Δ
(Delta)
10
settinng < 40m
2mm
2
2mm
2
-5.5mm
2
Summary of Contents for VD30C
Page 2: ......
Page 3: ......
Page 4: ......
Page 31: ...YK15 0009 DI 002 04 10 Fig 6 Dimensional drawing VD60C Fig 7 Dimensional drawing VD90C...
Page 33: ...YK15 0009 DI 002 04 12 Fig 10 Dimensional drawing VD60C H Fig 11 Dimensional drawing VD90C H...
Page 78: ......