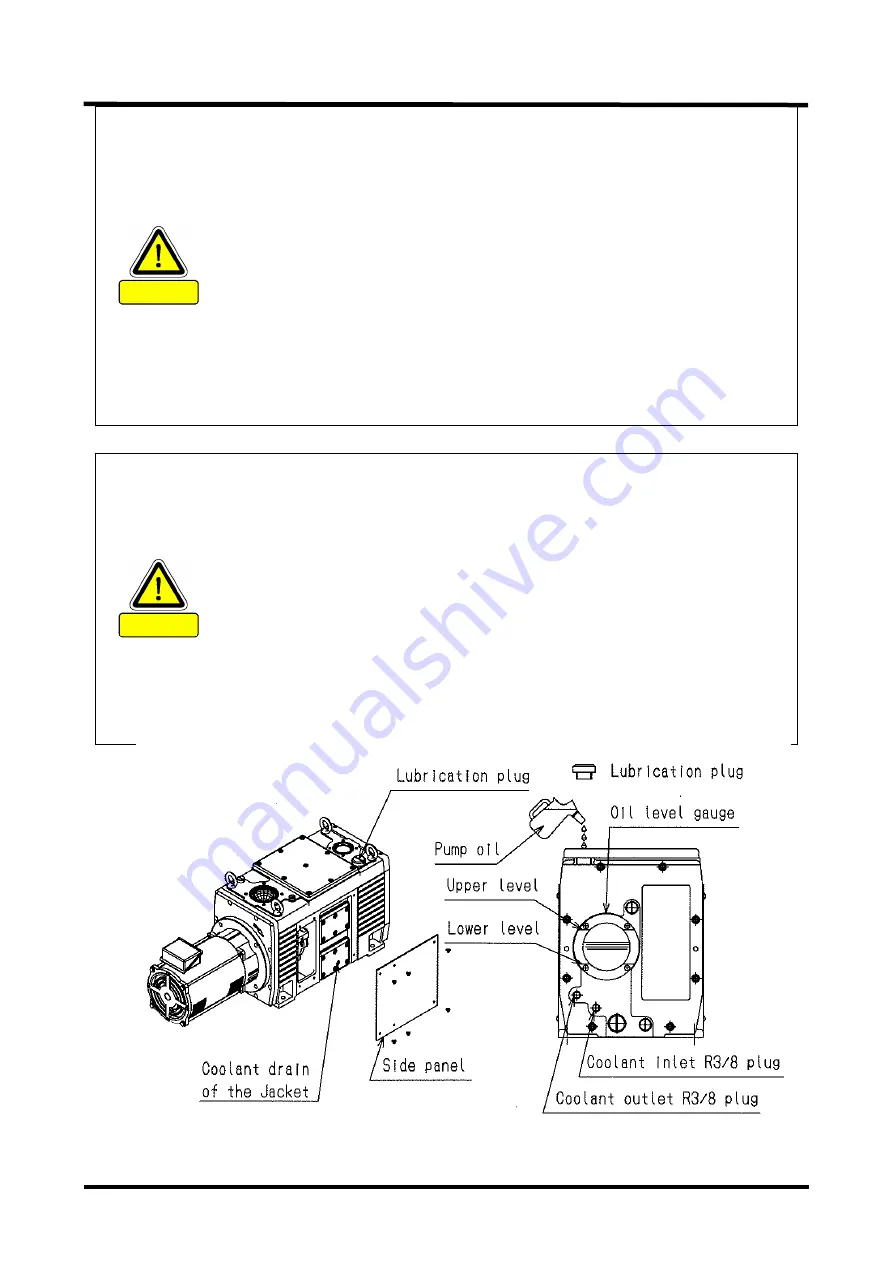
SK00-4390-DI-002-11
12
The machine is designed not to cause any leakage under restricted
condition and demonstrated by the Leak test. However, it still has a
risk of leaking under any abnormal condition other than specified, for
example abnormal water pressure rise. In such a case, the leakage
shall remain unstopped unless the supply from the system stops. You
should refrain from installing electrical equipment or wiring beneath
the Pump and on the floor around the Pump.
We recommend you to put the Leak sensor on the floor beneath the
Pump and engage it with the interlock system of the equipment. Close
the Coolant supply valve (HWSV) immediately you noticed the leakage.
Put the [Closed] tag onto the handle after having closed the valve.
Put a Flow meter (HWFM: for example Flow sight) applicable to
visuallycheck the flow onto the Coolant supply source to make it
possibleto check the flow.
If you use several pumps, be sure to connect the Coolant pipes
parallel.
Cooling capacity might come down if connected them serial and cause
thefailure.
You should put a filter at the front stage if you are obliged to use the
water containing much impurity such like water stain, iron and the like.
Appropriate flow might not be ensured when the supply source and
discharge outlet were apart or there was level difference in the
piping(discharge outlet was elevated higher than the Pump). In such a
case,cause a measure to ensure the flow volume, such as to change
the piping layout, put a larger pipe or raise the supply pressure within
thespecification range.
Fig. 4 Lubrication and water piping drawing
CAUTION
Summary of Contents for VS1501
Page 2: ......
Page 13: ...SK00 4390 DI 002 11 xi Fig 1 Warning Label display position...
Page 27: ...SK00 4390 DI 002 11 7 Fig 2 VS1501 Dimensional drawing...
Page 28: ...SK00 4390 DI 002 11 8 Fig 3 VS2401 Dimensional drawing...
Page 36: ...SK00 4390 DI 002 11 16 Fig 5 Suction Exhaust piping connection diagram...