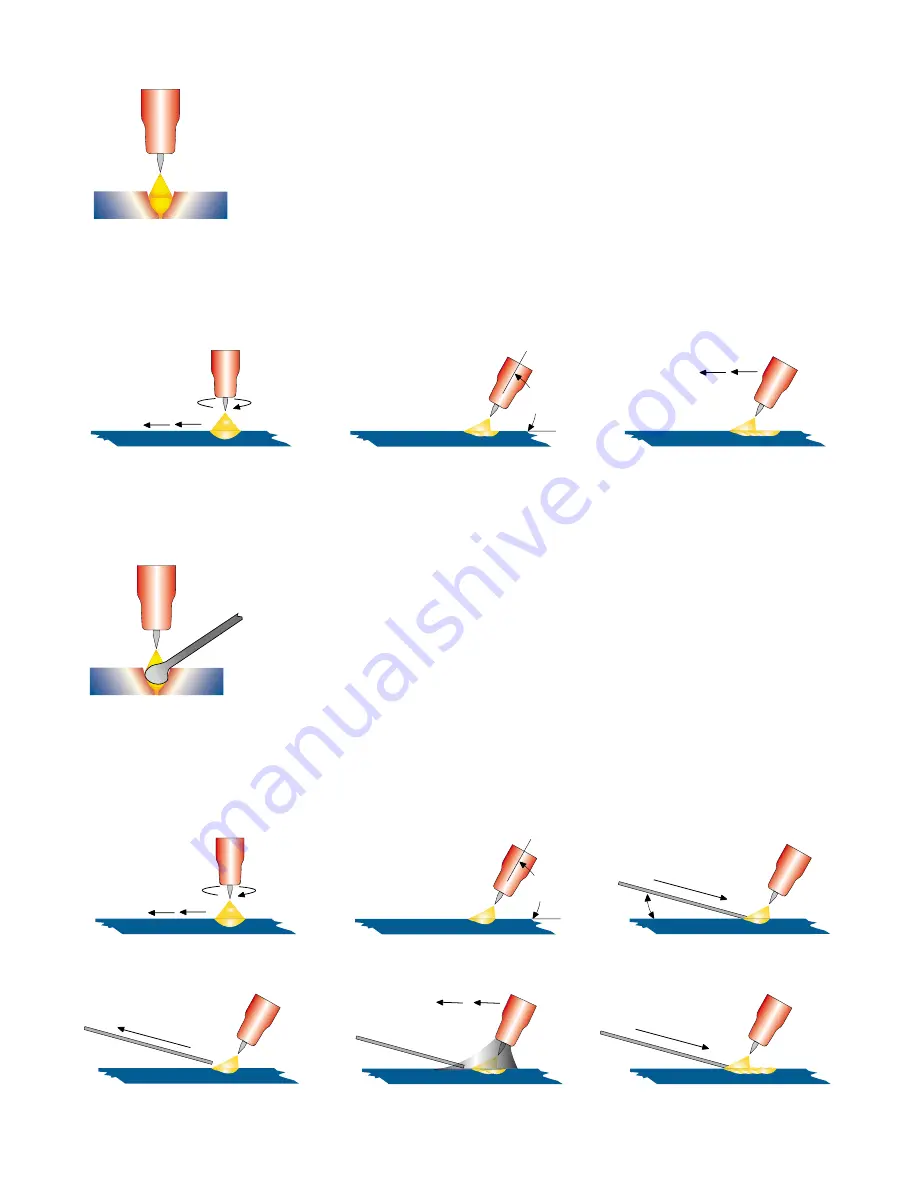
22
TIG Welding with Filler Wire Technique
It is necessary in many situations with TIG welding to add a filler wire into the weld
pool to build up weld reinforcement and create a strong weld. Once the arc is started
the torch tungsten is held in place until a weld pool is created, a circular movement
of the tungsten will assist is creating a weld pool of the desired size. Once the weld
pool is established tilt the torch at about a 75
° angle and move smoothly and
evenly along the joint. The filler metal is introduced to the leading edge of the
weld pool. The filler wire is usually held at about a 15° angle and fed into the
leading edge of the molten pool, the arc will melt the filler wire into the weld pool as the torch is
moved forward. Also a dabbing technique can be used to control the amount of filler wire added, the
wire is fed into the molten pool and retracted in a repeating sequence as the torch is moved slowly
and evenly forward. It is important during the welding to keep the molten end of the filler wire inside
the gas shield as this protects the end of the wire from being oxidised and contaminating the weld
pool.
75°
15°
Form a weld pool
Travel direction
Angle torch
Add Tig filler wire
Retract the filler wire
Move the torch forward to
the front of the weld pool
Repeat the process
gas
shield
TIG Welding Fusion Technique
Manual TIG welding is often considered the most difficult of all the welding
processes. Because the welder must maintain a short arc length, great care and skill are
required to prevent contact between the electrode and the workpiece. Similar to Oxygen
Acetylene torch welding, Tig welding normally requires two hands and in most
instances requires the welder to manually feed a filler wire into the weld pool with one
hand while manipulating the welding torch in the other. However, some welds combining
thin materials can be accomplished without filler metal like edge, corner, and butt joints.
This is known as Fusion welding where the edges of the metal pieces are melted together using only the
heat and arc force generated by the TIG arc. Once the arc is started the torch tungsten is held in place until
a weld pool is created, a circular movement of the tungsten will assist is creating a weld pool of the desired
size. Once the weld pool is established tilt the torch at about a 75
° angle and move smoothly and evenly
along the joint while fusing the materials together.
75°
Form a weld pool
Angle torch
Move the torch slowly
and evenly forward
Travel direction