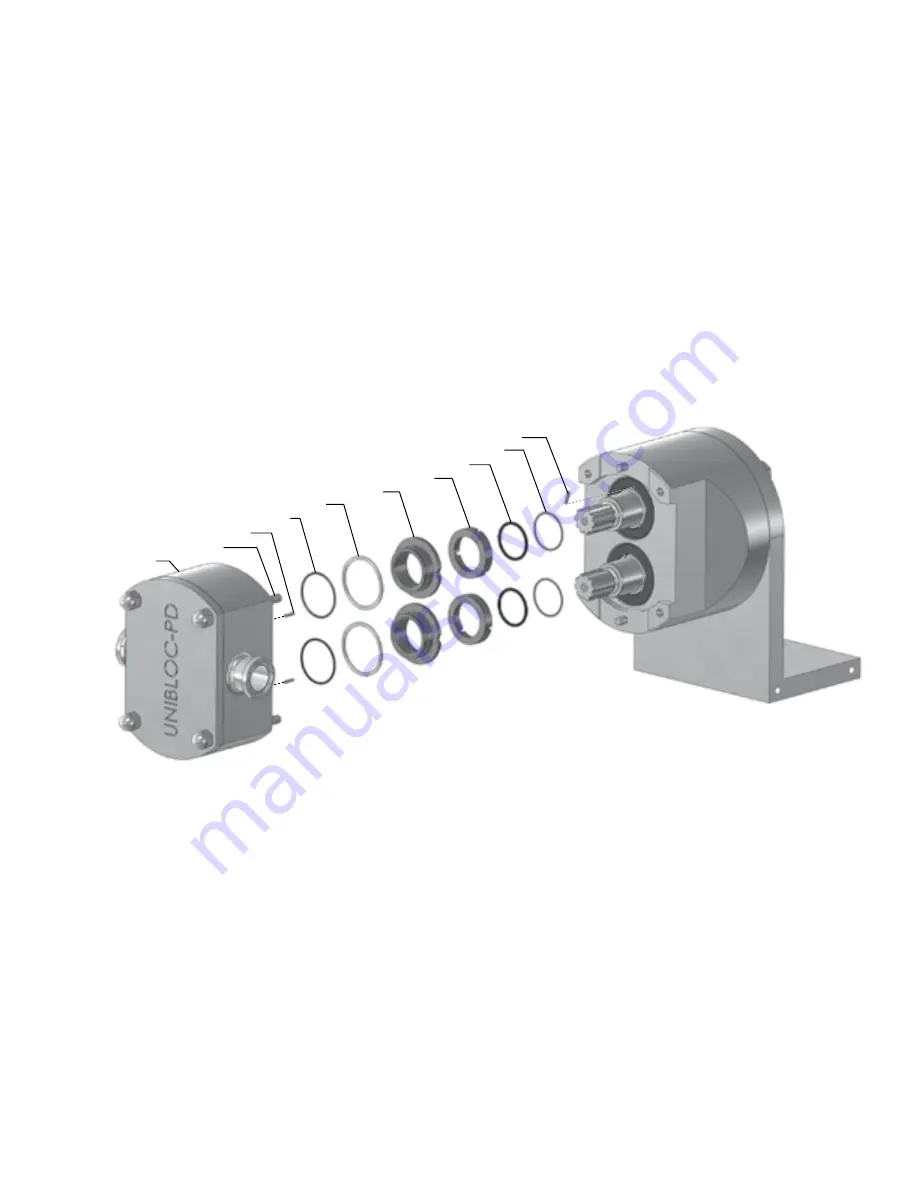
UNIBLOC-PD Operation & Service Manual: PD200-576 17
4.4.1 Single Mechanical Seal
This type of shaft seal is used in most applications with products that have a viscosity of less than 1,000 cPs. The maximum
rotational speed of this seal is 1500 rpm and the maximum service pressure is 13.5 bar (195 psig). The seal materials available are
stainless steel, carbon, silicone carbide, and tungsten. The standard o-rings supplied in these seals are FDA-viton or FDA-EPDM.
These can be replaced with other materials upon request.
UNIBLOC-PD 501
Series has front loaded seals. This seal comes with different seal face combinations. (See drawing G812B for
details.) Maximum shaft rotational speed for this seal is 2.4 m/s (7.8 ft/s) or 800rpm and the maximum service pressure should not
exceed 15 bar (220 psig). Maximum and minimum temperature limits are +160°C (320°F) and -15°C (5°F).
4.4.1.1 UNIBLOC-PD 200-275 Single Mechanical Seal Removal
Loosen and remove the acorn nuts from the
Rotor Housing
. Loosen the
Threaded Studs
by locking two M6 nuts against each
other on the exposed threaded stud ends. Remove the
Rotor Housing
by pulling on the ports or by tapping gently with a rub-
ber mallet. Do not rock the housing back and forth excessively. This can cause the seals to break. Remove the
Stationary Seal
Faces
and
Stationary Seal O-Rings
by pulling them out of the rotor housing. Remove the
Rotating Seal Faces
, the
Rotating
Seal O-Rings
, and
Rotating Seal Washers
by sliding them off the shafts. To avoid damage, carefully handle and store the loose
Stationary Seal Faces
and the
Rotating Seal Faces
so that their lapped sealing surfaces do not get scratched.
4.4.1.2 UNIBLOC-PD 200-275 Single Mechanical Seal Installation
If missing, insert the
Rotor Housing Pins
into the rotor housing and the
Shaft Pins
into the shafts. Coat the shafts and rotor
housing bores with a product compatible lubricant. Place the
Rotating Seal O-Rings
in the
Rotating Seal Face
first, and then
the
Rotating Seal Washers
. Slide the
Rotating Seal Rings
, slotted side first, onto the shafts. Place the
Wave Springs
between
the
Rotor Housing Pins
. Place the
Stationary Seal O-Rings
in the groove of the
Stationary Seal Faces
. Align the slots of the
Stationary Seal Faces
with the
Rotor Housing Pins
in the rotor housing. Push the
Stationary Seal Faces
into the rotor housing,
o-ring side first. Press several times to make sure they slide easily. Place a product compatible lubricant on the sealing surfaces.
Proceed to section 4.4.7 to complete the installation.
Stationary Seal O-Rings
Wave Springs
Stationary Seal Faces
Rotating Seal Faces
Rotating Seal O-Rings
Rotating Seal Washers
Shaft Pins
Rotor Housing Pins
Threaded Studs
Rotor Housing
UNIBLOC-PD 200-275 with Single Mechanical Seals
Summary of Contents for UNIBLOC-PD Series
Page 42: ...42 UNIBLOC PD Operation Service Manual PD200 576 UNIBLOC PUMP...
Page 43: ...UNIBLOC PD Operation Service Manual PD200 576 43 UNIBLOC PUMP...
Page 44: ...44 UNIBLOC PD Operation Service Manual PD200 576 UNIBLOC PUMP...
Page 45: ...UNIBLOC PD Operation Service Manual PD200 576 45 UNIBLOC PUMP...
Page 46: ...46 UNIBLOC PD Operation Service Manual PD200 576 UNIBLOC PUMP...
Page 47: ...UNIBLOC PD Operation Service Manual PD200 576 47 UNIBLOC PUMP...
Page 48: ...48 UNIBLOC PD Operation Service Manual PD200 576 UNIBLOC PUMP...
Page 49: ...UNIBLOC PD Operation Service Manual PD200 576 49 UNIBLOC PUMP...
Page 50: ...50 UNIBLOC PD Operation Service Manual PD200 576 3...
Page 51: ......
Page 52: ......