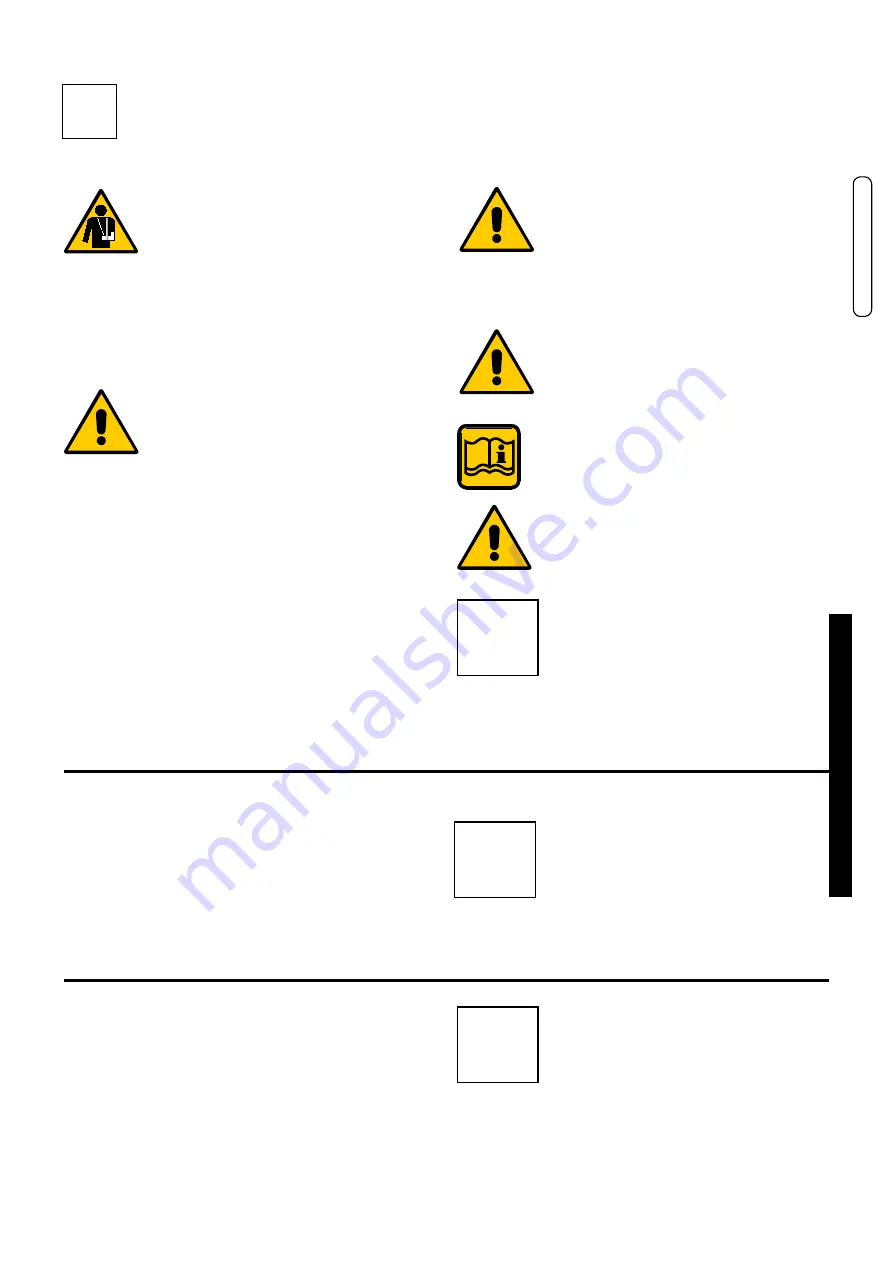
15
ENGLISH
Installation Instructions
3.2 - INSTALLATION STANDARDS
t must be installed by a professionally qualified technician,
who
shall take the responsibility of observing all local and/or
national laws published in the official journal, as well as
the applicable technical standards.
3.3 - PREVENTIVE VERIFICATION AND
VERIFICATION AND ADJUSTMENT
OPERATIONS
NOTE!
For further details relating to the standards,
rules and regulations for safe installation of
the thermal unit, refer to the section “Tech-
nical Information” on the boiler page of the
www.unicalag.it website
NOTE!
Further details in the section
‘‘Technical Information’’ on the boiler
indicated at page 2.
NOTE!
Further details in the section
‘‘Technical Information’’ on the boiler
indicated at page 2.
3
INSTALLATION INSTRUCTIONS
ATTENTION!
T
his boiler is intended solely for the use for
which it was expressly designed. Any other
use is to be considered improper and there-
fore dangerous.
This boiler heats water at a temperature
lower than the atmospheric pressure boiling
temperature.
Before connecting the boiler, have professionally
qualified personnel:
a) Thoroughly wash all the piping of the sys-
tem to remove any residues or impurities
which could jeopardise proper operation
of the boiler, even from a hygienic point
of view.
b) Check that boiler is set up to oper-
ate with the available type of fuel.
This can be seen written on the package and
on the technical feature plate;
c) Check that the chimney/flue has an appropri
-
ate draught, without any bottlenecks, and that
no exhausts from other appliances are insert-
ed, unless the flue has been implemented to
accommodate several utilities according to
specific standards and regulations in force.
Only after this check can the fitting between
the boiler and chimney/flue be mounted;
ATTENTION!
If there is dust and/or if there are
aggressive/corrosive vapours present in
the installation room, the appliance must
be protected suitably and must be able to
operate independently from the air in the
room.
ATTENTION!
Only mount the appliance on a closed wall, made
of non-flammable material, flat, vertical so that
the minimum distances required for installation
and maintenance can be observed.
The boiler must be connected to a central heat-
ing system and/or domestic hot water supply
network compatible with its efficiency and output.
The boiler can be installed outdoors in a
partially protected place or at least in a place
where the boiler is not exposed to the direct
action of the weather.
3.1 - GENERAL wARNINGS