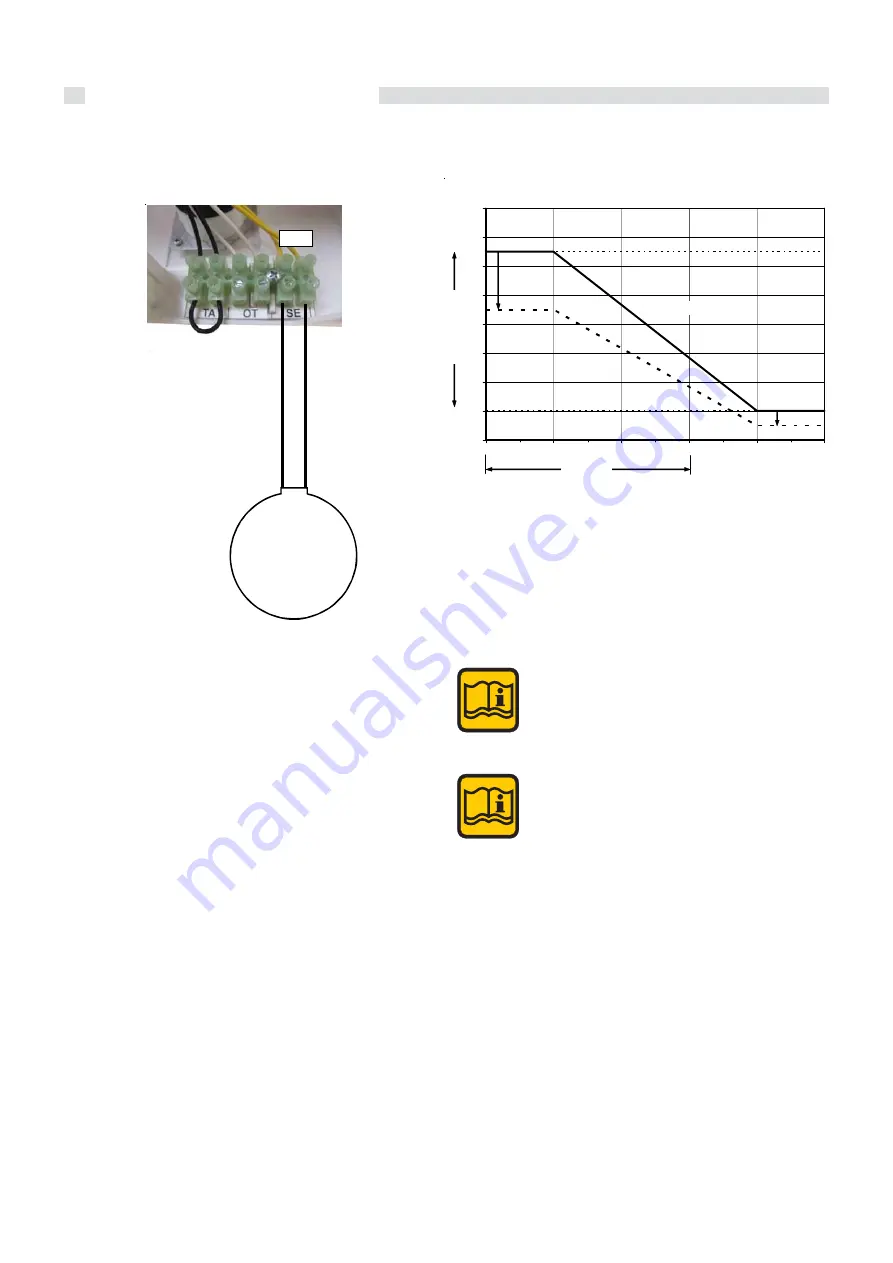
32
Instruction for the installer
Outdoor sensor connection (optional)
With this solution it is possible to control the flow temperature
according to the variations of the outdoor temperature.
However, it is necessary to configure the heating curve.
The curve can be “drawn” by setting the maximum and
minimum flow design temperatures: the first one must be
selected on the boiler (via the “C” knob on the control panel –
max. setting 85°C), whilst the second is set at 30°C (MINIMUM
HEATING TEMPERATURE).
-
The connection of the outer sensor has to be made on the
terminals
5
&
6
of the terminal strip
M1
.
This adjustment must be made by the parameter
oC
.
Obviously
this temperature is different from zone to zone and varies in
function of the climatic conditions of the installation site (it
corresponds to the minimum design temperature). The
minimum flow temperature instead (HL) is automatically set
by the boiler when the outdoor temperature is +20°C.
Once these parameters have been set the boiler will choose
a flow temperature on the heating curve on the basis of the
outdoor sensor readout.
Subsequently we have to make the maximum flow temperature
correspond to the minimum external temperature by setting
the Otc parameter (outdoor sensor set-point)
Note:
This adjustment could be susceptible to
subsequent slight changes in function of the
outdoor sensor’s location.
M1
6
5
Outer
sensor
The temperature detected by the outer sensor is
sent also to the REGOLAFACILE (if there) and
elaborated by the REGOLAFACILE it self
according to the setting of the heating curve.
In case of contemporary heat request by the ON-
OFF zone and the zone controlled by the
REGOLAFACILE, the ON-OFF zone has the
priority.
CH Setpoint vs ExtSensor
20
30
40
50
60
70
80
90
100
-20
-10
0
10
20
30
ExtSensor
30°C
Setpoint
C
H
a
dj
us
t
20°C
oC
-20°C
10°C
oC range
85°C
C
H
ad
ju
s
t r
a
ng
e
Night reduction=20°
5°C
0°C
Summary of Contents for ALKON R 18
Page 1: ...ALKON 09 R 18 C 18 R 24 C 24 00333176 2nd edition 10 2011 INSTALLATION AND SERVICING MANUAL...
Page 46: ......
Page 47: ......