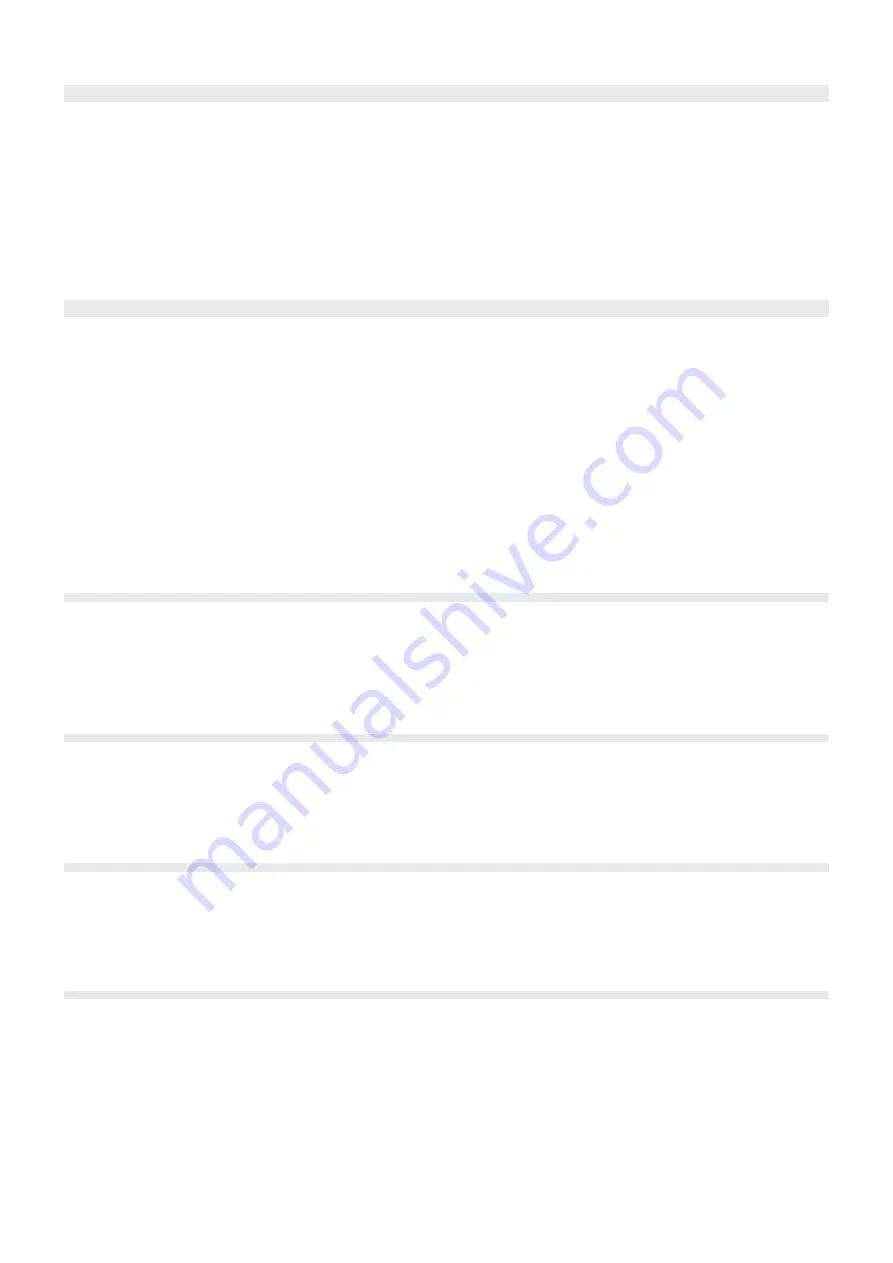
12
2.4 - CONNECTION TO THE
CHIMNEY
The chimney has a foundamental importance for
the good operation of the boiler.
Due to the low temperature of the smokes
during the intermittent opera tion, it is necessary
that the chimney is perfectly impermeable to
the condensate of the combustion products and
manufactured with corrosion resistant materials.
The different connections must be sealed with
an approved boiler putty so that the inlet of fresh
air, with consequent increase of the possibility
of condensate formation, is avoided.
Furthermore the possible condensate or rain
water comming from the chimney must be
avoided from entering the smoke chamber of
the boiler.
As far as the cross section and the high of the
chimney is concerned, it is necessary to make
reference to the local and national rules in force.
In the flue pipe, between the boiler and the
chimney, convenient sampling points for
smoke temperature and combustion products
analysis must be provided.
2.5 - WATER CONNECTIONS
2.5.1 - FEEDING WATER QUALITY
- The chemical-physical characteristics of
the C.H. system and reinstatement water
are foundamental for the good operation
and safety of the boiler.
- Among the inconvenients caused by the
bad quality of the feeding water the most
frequent and serious is the scaling of the
heat exchange surfaces.
- Less frequent, but also dangerous, is the
corrosion of the water side surfaces of all
the circuit.
- It is well known that the lime, due to its very
low thermal conductivity, reduces the heat
transfer so that also a scaling of a few
millimeters produces very dangerous
localized overheating.
1mm of lime reduces the heat transfer from
metal to water by 10%.
It is suggested to make a water treatement
in the following cases:
A- high hardness of the water available on site
(higher than 20°f).
B- very large C.H. systems.
C- large quantities of reinstatement water due
to water leaks.
D- subsequent fillings of the system due to
maintenance works.
E- mixing of different metals in the CH circuit.
For the treatment of filling water it is suggested to
address them self to specialized firms.
The same firms are able to provide for the
descaling of the boilers.
Every C.H. system needs reinstatements of
water, du to evaporation, small or large water
leaks or for maintenance works.
It is, therefor, necessary to be able to evaluate
the entity of the reinstatement water to avoid
inconvenients due to untreated water.
For that reason it is suggested to fit, in the
feeding line to the boiler, a water meter for small
capacities.
2.5.2 - C.H. FLOW AND RETURN
CONNECTIONS
The dimensions of flow and return connections
are shown, for each boiler model, in the table
DIMENSIONS.
Before connecting the boiler to the C.H.
system, this one has to be throughly cleaned.
Make sure in the system there is a sufficient
number of air venter.
When connecting flow and return pipes avoid to
create mechanical stress onto the boiler flanges.
The boiler is not made to support the piping of
the C.H. system, which needs dedicated
supports.
Once the complete C.H. system is finished,
check for water leaks all the connections.
2.5.3 - CONNECTION OF FILLING
AND DRAIN TAP
For the filling and drain of the boiler a dedicated
tap can be connected to the point T4, which is
in rear part of the boiler.
2.5.4 - CONNECTION OF THE
PRESSURE RELIEF VALVE
Fit onto the point T3 or onto the supply pipe,
within 0.5m from the flow flange, a pressure
relief valve properly dimensioned for the boiler
capacity and in conformity with the local rules in
force.
It is forbidden to put any gate valve between
the boiler and the pressure relief valve.
The maximum working pressure of the boiler is
6 bar; the pressure relief valve has to be
selected accordingly.
2.5.5 - CONNECTION OF THE
EXPANSION PIPE AND VESSEL
An expansion vessel is always necessary, to
compensate the water volume increase due
to the heating.
The ELLPREX boilers are suitable for fully
pumped systems, which can be open vented
or sealed.
In the 1
st
case the height of the hydrostatic
column must be, at least, 3m above the boiler
casing and the capacity of the expansion
cistern shall be able to contain, between the
water surface and the overflow pipe, the volume
increase of all the water of the C.H. system.
Preference shall be given to high and narrow
cisterns, to expose to the air a surface as small
as possible, thus reducing the water evaporation.
In the 2
nd
case the vessel capacity has to be
calculated taking into consideration:
- The total volume of the water contained in
the system. The maximum working pressure
of the system (see setting of PRV).
- The maximum working pressure of the
expansion vessel.
- The initial preloading of the expansion vessel.
- The maximum working temperature of the
boiler (the maximum setting of the
thermostat fitted onto the panel board is
90 °C; under this aspect it it suggested to
consider 100 °C.
Summary of Contents for ELLPREX Series
Page 1: ...26739 01 13 rev 4 ELLPREX INSTALLATION USE AND SERVICING INSTRUCTION to be kept by the user...
Page 37: ...37 Notes...
Page 38: ...38 Notes...
Page 39: ...39 Notes...