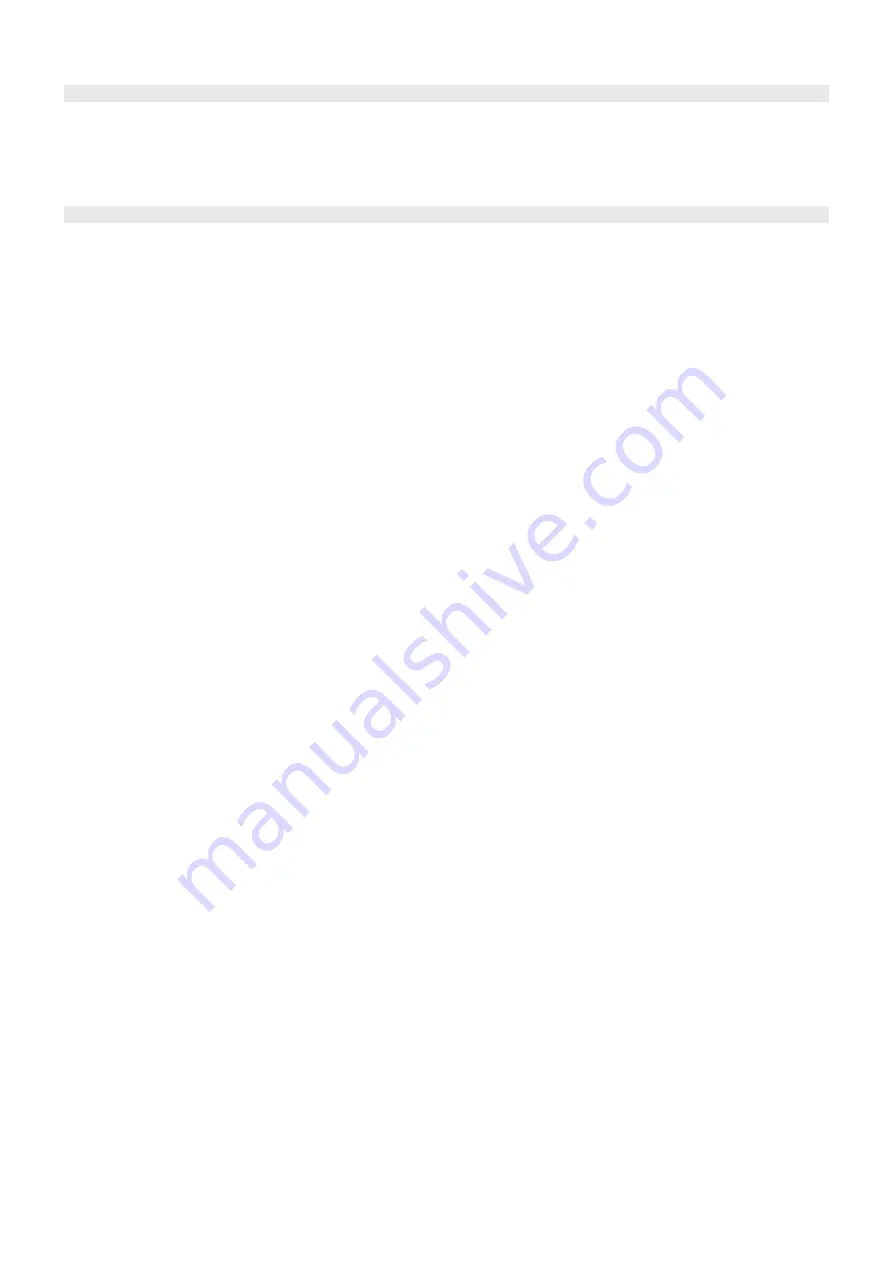
2
GENERAL INFORMATIONS
Introduction
This manual supplies a summary of what has to be followed during the installation, use and
servicing of the UNICAL boilers, TRISECAL 3P range.
In the course of this text the short name TS 3P can be used to indicate the TRISECAL 3P
boiler.
Choice of the boiler
For a correct choice and application of the TRISECAL 3P boilers it is necessary to follow the
instructions given in this manual.
Installation
The installation of the boilers and the auxiliary equipments, related to the heating system,
must be in conformity with all the regulations and rules in force.
It is law that all the gas appliances are installed, commissioned and serviced by a registered
installer in accordance with the regulations below. Failure to install appliances correctly could
lead prosecution. It is in your own interest, and that of the safety, to ensure the law is complied
with.
The following must be complied with:
Current Building Regulations and Clean Air Act.
Water Authority Regulations.
Local Authority Regulations and Regional Bylaws.
Gas Safety Regulations.
Any special regional requirements of local Electricity and Gas undertaking.
Fire Service and Insurance Company requirements.
Commissioning
The main purpose of the commissioning is to verify the correct operation of all the safety and
control devices.
Before leaving the installation the commissioner has to control the operation of the boiler for,
at least, a complete working cycle.
Guarantee
The boiler guarantee is bound to the compliance of the the requirements stated in this manual,
and any non-fulfilment or modification will make it void.
Normative
It is the responsibility of the installer to fulfil all the regulations concerning the boiler house,
the safety devices, the chimney, the fuel supply lines, the electrical installations and all the
other local requirements and safety instructions.
Approvals
The UNICAL boilers, TRISECAL 3P range, have been tested and CE certified for the gas
operation by GASTEC (ITALIA), who has recognised to these boilers the conformity certificate
according to the following directives:
-
Gas Appliances Directive (90/396 CE), compulsory as per 1st January 1996;
-
Efficiency Directive (92/42 CE), compulsory as per 1st January 1998;
-
The conformity to the Low Voltage Directive (73/23 CE), compulsory as per 1st January
1997 has been verified and ascertained by GASTEC ITALIA.
The conformity to the EMC (Electro Magnetic Compatibility 89/336 CE), compulsory as per
1st January 1996, is not applicable to the TRISECAL 3P boilers because they do not have
electronic components.
For the time beeing there are no European Directives covering the oil fired boilers, except the
Efficiency Directive (92/42 CE).
Data plate and Serial No.
The data plate, supplied in a separate enveloppe with the relevant documents, makes reference to
a serial No, embossed in an aluminium plate riveted to the front tube plate in the lower RH side
corner.
Use of the boiler
This boiler has to be used for heating the water at a temperature not higher than the
boiling temperature in the installation conditions.
WARNING
When the boiler is operated with a pressure jet gas burner, because it does not belong to any of the categories among those listed in the Annex
II to the Directive 97/23/CE (regarding pressure equipment) and beeing, furthermore, mentioned in the Directive 90/396/CE (Gas Appliance
Directive) to which the art. 1, clause 3, paragraph 6.5 makes reference, it is excluded from the scope of the Directive.