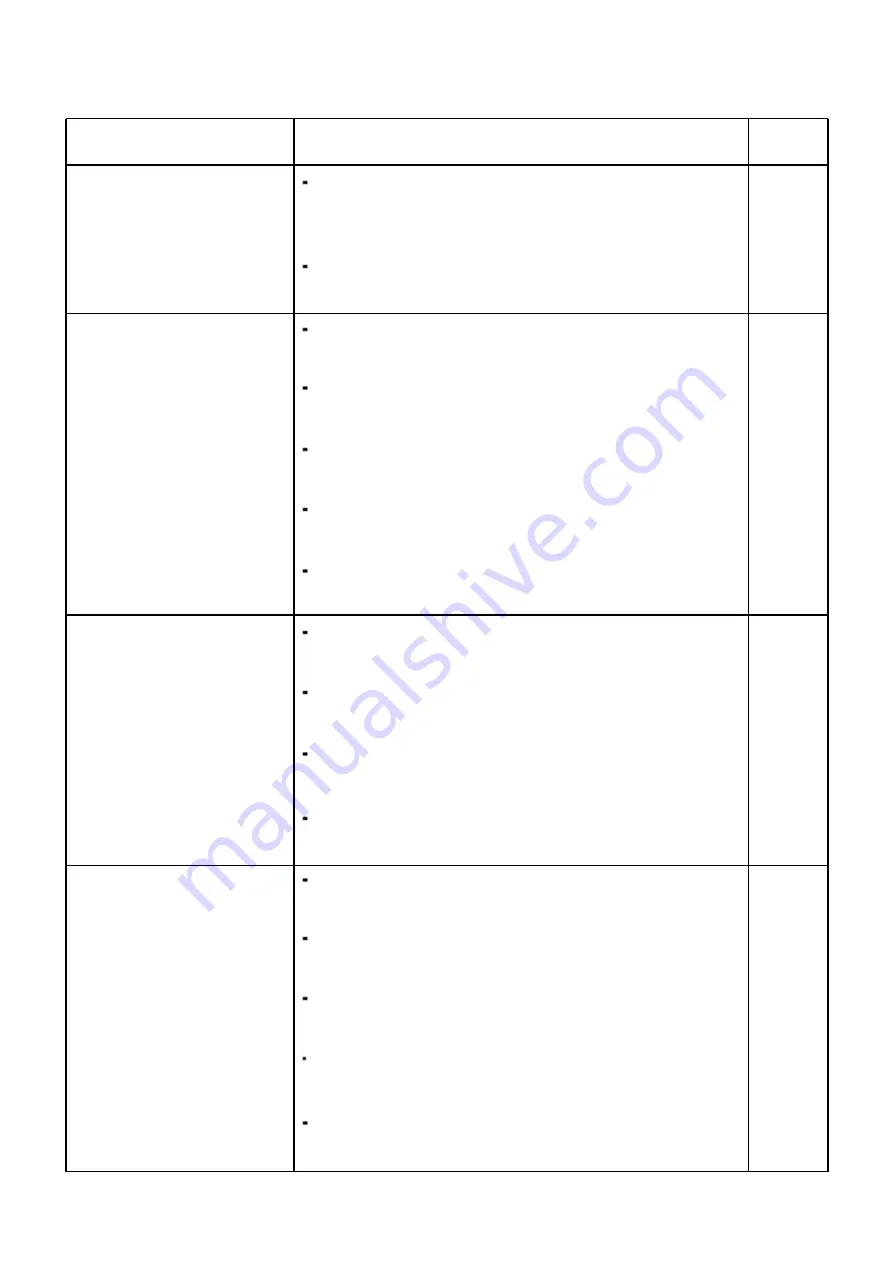
- 22 -
10. 문제 점 해결
증 상
조사 내용
참고
1.윗실 이 재 봉되지 않음
․윗 실장력이 약하 지 않 은가. 또는 아 래실 장력이 약하지
않은가 ?
-> 윗실장 력, 아래 실 장 력을 조정하여 주십시 오
13
․윗 실천평실 걸이의 위치는 적절 한가.
-> 윗실천 평실걸이 의 위 치를 정확하게 조정하 여 주 십시오.
19
2. 재봉 도중 비봉
․바 늘 취 부 방 법이 틀리지 않은가?
-> 틀릴 때는, 정확하게 바늘 을 취 부하여 주십시오 .
9
․루 퍼 칼 끝이 망가지지 않은 가.
-> 루퍼를 교체 하여 주십시오 .
16
․바 늘과 루퍼의 타이밍 은 적 절한가
-> 바늘과 루퍼 의 타 이밍을 정확하 게 조정 하여 주십시오
16
․아 래실 천평의 타이밍 은 적 절한가.
-> 아래실 천평 의 타 이밍을 정확하 게 조정 하여 주십시오
20
․바 늘과 루퍼의 간격이 넓지 않은가
-> 바늘과 루퍼 의 간 격을 조정하여 주십시 오.
16
3. 재봉 엇갈림.
재봉 파카링
(풀러 사용 )
․풀 러의 타이밍은 적절 한가.
-> 풀러장 치의 타이밍을 조정 하여 주십시오.
․풀 러의 이송량은 적정 한가.
-> 풀러의 이송 량을 조정하여 주십 시오
․노 루발의 압력은 적정 한가.
-> 노루발 압력 을 조 정하여 주십시 오.
13
․톱 니의 높이는 적정한 가.
-> 톱니의 높이 를 조 정하여 주십시 오.
19
4. 천의 이송이 안됨.
․톱 니의 높이가 낮지 않은가 .
-> 톱니의 높이 를 조 정하여 주십시 오.
19
․노 루발 압력이 약하지 않은 가.
-> 노루발 압력 을 조 정하여 주십시 오.
13
․톱 니가 마모하지 않은 가.
-> 전문가 에게 보여 주십시오 .
․노루발이 떠서 재봉 천을 완전히 누르지 않고 있는가.
-> 전문가 에게 보여 주십시오 .
․톱 니와 노루발이 한쪽 으로 치우칠 때
-> 전문가 에게 보여 주십시오 .
Summary of Contents for DT6-H892?3
Page 2: ......
Page 4: ...5 off A S 31 2 40 25 OFF A S A S...
Page 32: ...22 10 1 13 19 2 9 16 16 20 16 3 13 19 4 19 13...