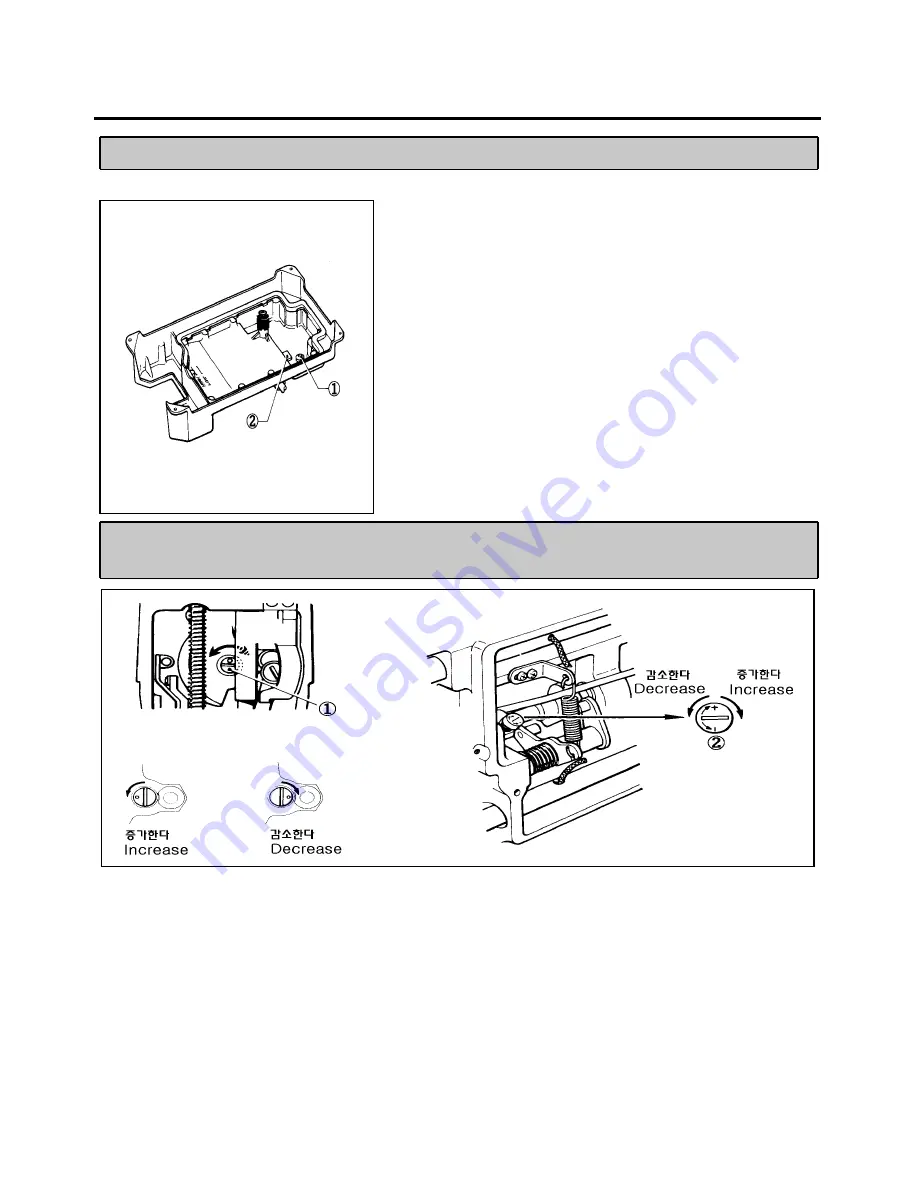
- 2 -
급 유 / LUBRICATION
1. 급 유 / Lubrication
★ 기름은 좌측의 선(HIGH)까지 천천히 넣어주십시오.
우측의 선(LOW)에서 기름이 내려가면 급유해 주십시오.
★ 기름이 오염되었으면 기름덮개나사①을 빼내고, 기름을 바꿔
주십시오.
★ 자석②와 유수판에 쌓인 오염을 깨끗이 닦아주십시오.
※ 기름은 스핀들15 기름을 사용해주십시오.
★ Slowly pour oil into the oil pan to the HIGH mark.
If the oil level falls below the LOW mark. add oil.
★ If the oil becomes contaminated, remove the oil cover
Screw ①.
★ Wipe off any contamination from the magnet ②, and the
oil pan.
※ Use the oil specified by Spindle15.
2. 상축
․
가마 급유량의 조절 /
Adjusting lubrication for upper shaft and rotary hook
1. 상축급유량의 조절
★ 면판을 분리하고, 상축급유조절나사①을 돌려서 급유량을 조절해주십시오.
1. Upper shaft lubrication
★ Remove the face plate and turn the adjusting screw ① for the upper shaft.
2. 가마급유량의 조절
★ 미싱을 눕히고, 가마급유조절나사②를 돌려서 급유량을 조절해주십시오.
2. Rotary hook lubrication
★ Tilt the machine head until it stops and turn the adjusting screw ② for the rotary hook.
Summary of Contents for LS2-H530
Page 2: ......
Page 4: ...5 off A S 34 2 40 25 OFF A S A S...
Page 26: ...16 4 4 8 8 8 8 4 4 4 6 6 6 2...
Page 28: ...18 4 4 1 4 4 8 8 8 6 6...
Page 30: ...20 6 6 6 6 puff 8 11 14 4 13 11 14 11...
Page 32: ...22 6 1 13 6 11 11 11 11...
Page 34: ...24...