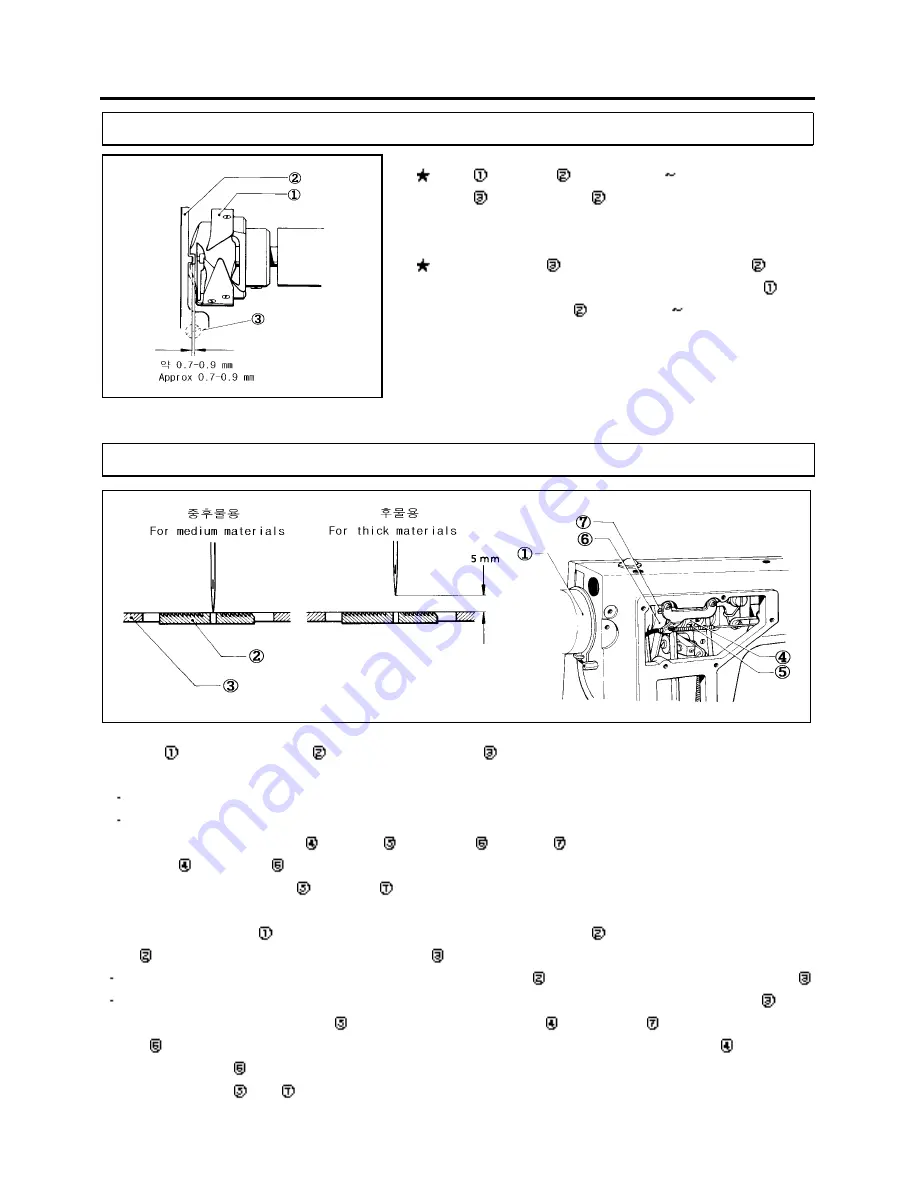
- 16 -
4. 이송타이밍 조정 / Adjusting the feed timing
3. 가마와 가마고정의 간격조정 / Adjusting the rotary hook holder poaition
조 정 / ADJUSTMENT
★ 내가마①와 가마고정②의 간격은 약0.7~0.9mm가 되도록
죔나사③을 풀고, 가마고정②를 앞 뒤 움직여서
조정해 주십시오.
★ Loosen the screw ③. Move the rotary hook holder ② forward
or backward so that the gap between the rotary hook ① and
the rotary hook holder ② is approx 0.7~0.9mm.
1. 미싱풀리①를 앞쪽으로 돌려 톱니②가 상승해서 톱니끝이 침판③의 상면과 일치했을 때 바늘의 끝이 아래와 같이 되어
있는지를 확인해주십시오.
․ 중후물용 : 톱니의 상면과 침판의 상면과 바늘의 선단이 일치합니다.
․ 후물용 : 톱니의 상면과 침판의 상면이 일치하고, 바늘의 선단과 침판의 상면은 5mm의 간격이 있습니다.
2. 이송타이밍이 다를때는 상하편심륜④의 고정나사⑤와 수평편심륜⑥의 고정나사⑦을 풀고 조정합니다. 톱니가 빨리 내려갈때는
상하편심륜④과 수평편심륜⑥을 미싱의 회전방향과 반대방향에, 또 톱니가 늦을때는 미싱의 회전방향으로 조금 돌립니다.
3. 올바른 타이밍에 맞춰 고정나사⑤와 고정나사⑦를 확실히 체결해주십시오.
1. Turn the machine pulley① toward the front of the machine until the feed dog② ascends and the tips of the feed
dog② align with the upper surface of the needle plate③. At this time, check that the needle tip is as indicated below.
․For thin materials : The needle tip is aligned with tips of the feed dog② and the upper surface of the needle plate③.
․For thick materials : There is a 5mm gap between the needle tip and the upper surface of the needle plate③.
2. To adjust the timing, loosen the screw⑤ of the feed lifting eccentric wheel④ and the screw⑦ of the level feed eccentric
wheel⑥. If the feed dog descends below the needle plate too soon, turn the feed lifting eccentric wheel④ and the level
feed eccentric wheel⑥ opposite to its normal rotation. If the feed dog is too late, turn the wheel slightly forward.
3. Tighten the screws ⑤ and ⑦.
All manuals and user guides at all-guides.com
all-guides.com
Summary of Contents for LS2-H550
Page 2: ...All manuals and user guides at all guides com...
Page 4: ...5 off A S 31 2 40 25 OFF A S A S All manuals and user guides at all guides com...
Page 35: ...25 4 4 16 15 15 15 4 4 4 6 6 6 2 All manuals and user guides at all guides com...
Page 37: ...27 4 4 1 4 4 15 15 15 6 6 All manuals and user guides at all guides com...
Page 39: ...29 6 6 6 6 puff 15 19 23 4 22 19 23 19 All manuals and user guides at all guides com...
Page 41: ...31 6 1 22 6 24 24 24 24 All manuals and user guides at all guides com a l l g u i d e s c o m...
Page 43: ...33 All manuals and user guides at all guides com...