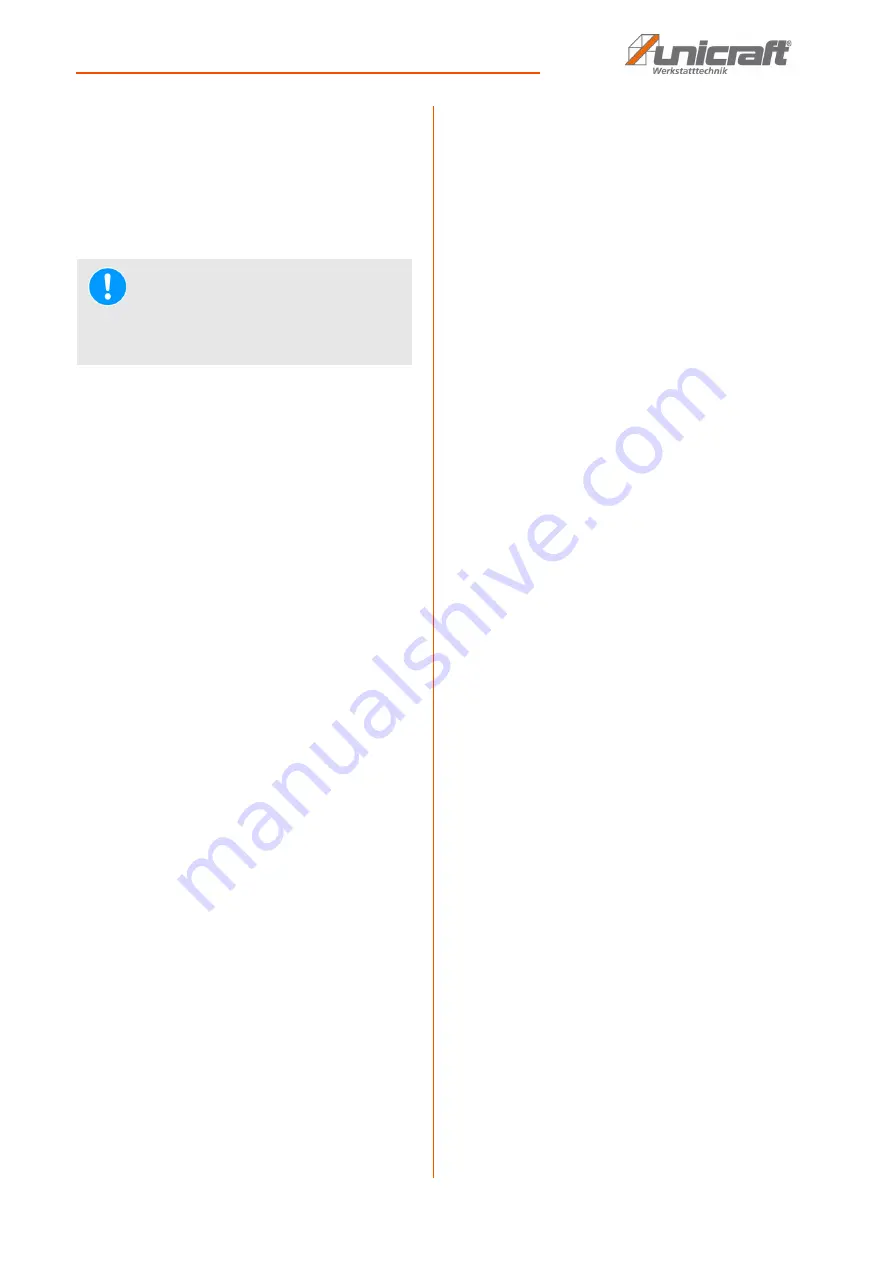
14
WPP 15 E | Version 1.02
Disposal, reusing used machines
11.2.5 Oil changes
Draining oil:
Step 1: open the screw connection on the retracted hy-
draulic cylinder.
Step 2: pump out the hydraulic oil and collect it in a suit-
able container using a hose.
Topping up oil:
Step 1: retract the piston so that it is in the base position.
Step 2: top up new oil via the filler neck.
Step 3: vent the hydraulic system. For this purpose, turn
the switching valve in anti-clockwise direction.
Operate the pump lever several times to remove
the air from the hydraulic system. Then once
again close the switching valve.
12 Disposal, reusing used machines
In your own interest and to protect the environment
make sure that all machine components are exclusively
disposed of in as intended and permitted.
12.1 Decommissioning
Disused machines must be decommissioned immedi-
ately to prevent misuse at a later point and putting the
environment or persons at risk.
Step 1: remove all environmentally hazardous process-
ing materials from the used machine.
Step 2: if necessary, disassemble the machine into as-
semblies and components that are easy to han-
dle and suitable for recycling.
Step 3: the machine components and processing mate-
rials must be disposed of using the intended dis-
posal methods.
12.2 Disposing of lubricants
Remove escaping, used or excess grease from the lu-
brication points featuring lubricant.
Lubricant manufacturers provide disposal information
for the lubricants used. If necessary, request product-
specific data sheets.
13 Liability for defects (warranty)
Our customers also represent consumers and they are subject
to statutory regulations. Customers must give us the opportu-
nity to audit the defect and transport the goods to our work-
shops for auditing upon our request and at our expense. The
following applies to our commercial customers:
(1) Customers shall check delivered goods for defects immedi-
ately on delivery. In this process, any identified, obvious dam-
age must be immediately indicated in writing. Transport
damage and missing packaging items shall also be reported
to the haulage company immediately. Any defects that were
not identified despite thorough inspections shall be reported in
writing immediately after having been identified. In this case,
our customer must immediately stop processing and using the
ordered goods. Customers must give us the opportunity to
audit the defect and transport the goods to our workshops for
auditing upon our request and at our expense. After having
carried out a mutually agreed approval, any indication of
defects that were identified upon approval shall be excluded.
The statutory period of liability for defects of two years shall not
apply to commercial customers.
(2) The period of liability for defects shall be one year from the
transfer of risk, providing no other periods have been specified
in agreements or statutory regulations. If the manufacturer of
the item subject to delivery grants a longer period of liability for
defects or a warranty, we shall transfer our resulting rights to
the ordering party/purchaser upon making the purchase. We
can provide an up-to-date list of individual periods of liability
for defects and their terms and conditions as well as warranty
periods and their terms and conditions as specified by the
manufacturer.
(3) In the event of a warranty case we shall carry out improve-
ments or provide replacement deliveries following coordination
with the manufacturer. We shall not be obliged to reimburse
any incurred costs, in particular for transport, travelling, labour
and material caused by transporting the item subject to the
purchase to a different location than the place of fulfilment,
unless specified in the statutory regulations. If any improve-
ments or replacement deliveries as a result of defects fail twice
(provide verification) or if the elimination of the defect would
incur unfeasibly high costs, causing improvements to be
denied, customers shall be permitted to demand either a
reduction of the price or annulment of the contract. We hereby
notify customers that there shall be no liability for defects in
particular for damage caused at customer premises as a result
of misuse or unintended use as well as for damage caused by
subjecting products to damaging, external influences at cus-
tomer premises (in particular extreme temperatures, humidity,
extraordinary physical or electrical loads, voltage fluctuations,
lighting strikes, static electricity, fire).
(4) If audits as part of claims for liability for defects result in that
the claim has been unjustified, we shall be authorised to
charge a conventionally applicable remuneration for the audit
of the goods as well as shipping costs.
(5) Our warranty shall not apply to natural wear, incorrect use
and storage, incorrect installation or damage caused after the
transfer of risk as a result of incorrect or irresponsible handling,
excessive use, unsuitable processing materials or as a result
of other influences that have not been specified in the contract.
(6) Any repairs carried out by ordering parties/purchasers or
third parties without our consent or incorrect repairs by a ser-
vice partner that has not been authorised by the manufacturer
shall render any claims for liability for defects void.
NOTE!
Dispose of the removed oil separately.
Consult the lubricant manufacturer for appropriate
information.