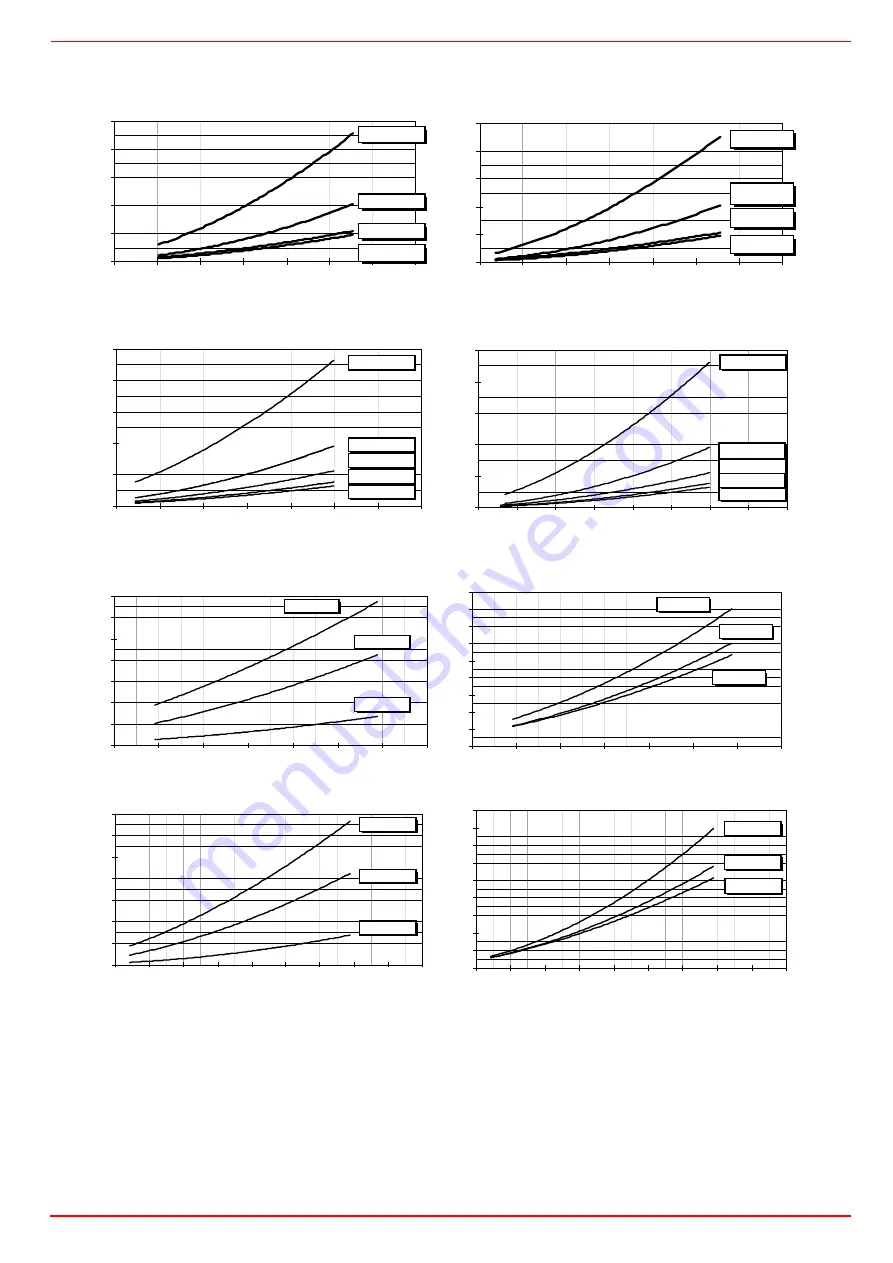
C.I.B. UNIGAS - M039132CD
15
Pressure in the network - gas flow rate curves
z
Gas burners
GA
S PRESSURE
mbar
NG280M-.TN...
Gas rate Stm
3
/h
NG280M-.xx...
Gas rate Stm
3
/h
GAS PRESSURE mbar
NG350M-.TN...
Gas rate Stm
3
/h
NG350M-.PR/MD...
Gas rate Stm
3
/h
GAS PRESSURE mbar
NG400 M-.TN..15-20-25
Gas rate Stm
3
/h
NG400 M-.TN..32-40-50
Gas rate Stm
3
/h
G
AS PRESSURE mbar
NG400 M-.PR/MD...15-20-25
Gas rate Stm
3
/h
NG400 M-.PR/MD...32-40-50
Gas rate Stm
3
/h
0
20
40
60
80
100
5
10
15
20
25
30
35
40
Rp 1" (25)
Rp 1"¼ (32)
Rp ¾" (20)
Rp ½" (15)
0
20
40
60
80
100
5
10
15
20
25
30
35
40
Rp 1" (25)
Rp 1"¼ (32)
Rp ¾" (20)
Rp ½" (15)
0
20
40
60
80
100
10
15
20
25
30
35
40
45
Rp 1" (25)
Rp 1"¼ (32)
Rp 1"½ (40)
Rp ¾" (20)
Rp ½" (15)
0
20
40
60
80
100
5
10
15
20
25
30
35
40
45
Rp 1" (25)
Rp 1"½ (40)
Rp 1"¼ (32)
Rp ½ " (15)
Rp ¾ " (20)
0
20
40
60
80
100
120
140
15
20
25
30
35
40
45
50
Rp 1" (25)
Rp ¾" (20)
Rp ½" (15)
0
2
4
6
8
10
12
14
16
18
15
20
25
30
35
40
45
50
Rp 1"¼ (32)
Rp 1"½ (40)
Rp 2" (50)
0
20
40
60
80
100
120
140
10
15
20
25
30
35
40
45
50
55
Rp 1" (25)
Rp ¾" (20)
Rp ½" (15)
0
2
4
6
8
10
12
14
16
18
10
15
20
25
30
35
40
45
50
55
Rp 1"¼ (32)
Rp 1"½ (40)
Rp 2" (50)
Summary of Contents for IDEA LG280
Page 46: ......
Page 47: ......
Page 48: ......
Page 49: ......
Page 50: ......
Page 51: ......
Page 52: ......
Page 53: ......
Page 54: ......
Page 56: ...C I B UNIGAS M039132CD 47 ...
Page 63: ......
Page 65: ...E039132CA Rev 0 5 07 2015 LG NG NGX280 LG NG NGX350 LG NG NGX400 WIRING DIAGRAMS ...
Page 67: ......
Page 68: ......
Page 69: ......
Page 70: ......
Page 71: ......
Page 72: ......
Page 73: ......
Page 74: ......
Page 75: ......
Page 76: ......
Page 77: ......
Page 78: ......
Page 79: ......
Page 80: ......
Page 81: ......
Page 82: ......
Page 83: ......
Page 84: ......
Page 85: ......
Page 86: ......
Page 87: ......
Page 88: ......
Page 89: ......