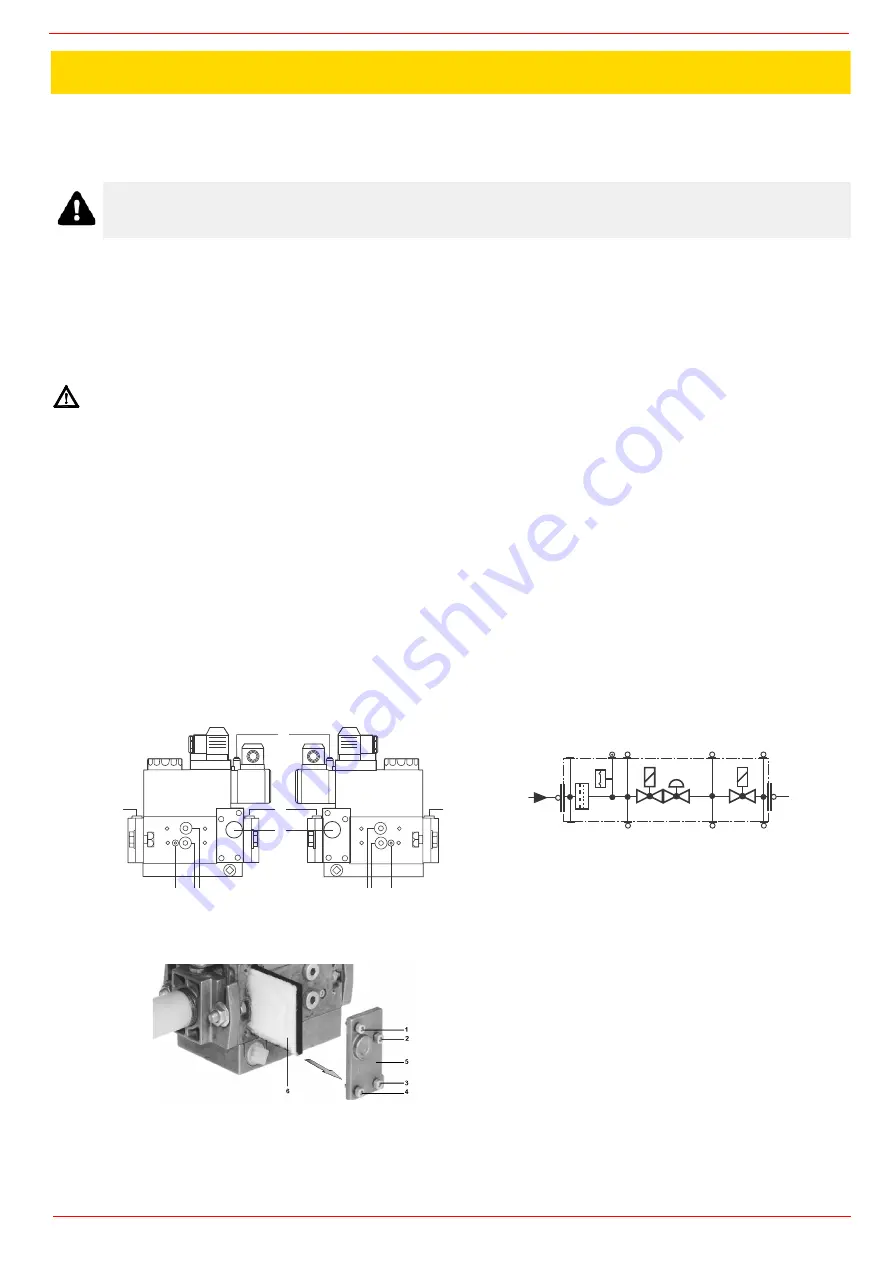
PART III: MAINTENANCE
28
At least once a year carry out the maintenance operations listed below. In the case of seasonal servicing, it is recommended to carry
out the maintenance at the end of each heating season; in the case of continuous operation the maintenance is carried out every 6
months.
ROUTINE MAINTENANCE
Clean and examining the gas filter cartdrige, if necessary replace it (Fig. 22 on).
Removal, examination and cleaning of the combustion head (see Fig. 28 on).
Check the ignition and detection electrodes, clean and adjust if necessary (see page 31). In case of doubr, check the detection cur-
rent according to the schemes in page 32.
Cleaning and greasing of sliding and rotating parts.
ATTENTION: when servicing, if it was necessary to disassemble the gas train parts, remember to execute the gas proving test,
once the gas train is reassembled, according to the procedure imposed by the law in force.
Removing the filter in the MULTIBLOC DUNGS MB-DLE 405..412
Check the filter at least once a year!
Change the filter if the pressure difference between pressure connection 1 and 3 (Fig. 22-Fig. 23)is
p > 10 mbar.
Change the filter if the pressure difference between pressure connection 1 and 3 (Fig. 22-Fig. 23) is twice as high compared to the last
check.
You can change the filter without removing the fitting.
1
Interrupt the gas supply closing the on-off valve.
2
Remove screws 1 ÷ 4 using the Allen key n. 3 and remove filter cover 5 in Fig. 24.
3
Remove the filter 6 and replace with a new one.
4
Replace filter cover 5 and tighten screws 1 ÷ 4 without using any force and fasten.
5
Perform leakage and functional test, p
max.
= 360 mbar.
6
Pay attention that dirt does not fall inside the valve.
WARNING: ALL OPERATIONS ON THE BURNER MUST BE CARRIED OUT WITH THE MAINS DISCONNECTED
AND THE FUEL MANAUL CUTOFF VALVES CLOSED!
ATTENTION: READ CAREFULLY THE “WARNINGS” CHAPTER AT THE BEGINNIG OF THIS MANUAL.
Fig. 22
Fig. 23
Fig. 24
PART III: MAINTENANCE
➞
1
0
5
3 4
5
3
4
6
6
➞
2
1
3
p
e
0
4
p
a
5
p
Br
0
3
p
e
4
p
a
6
1
5
p
Br
2