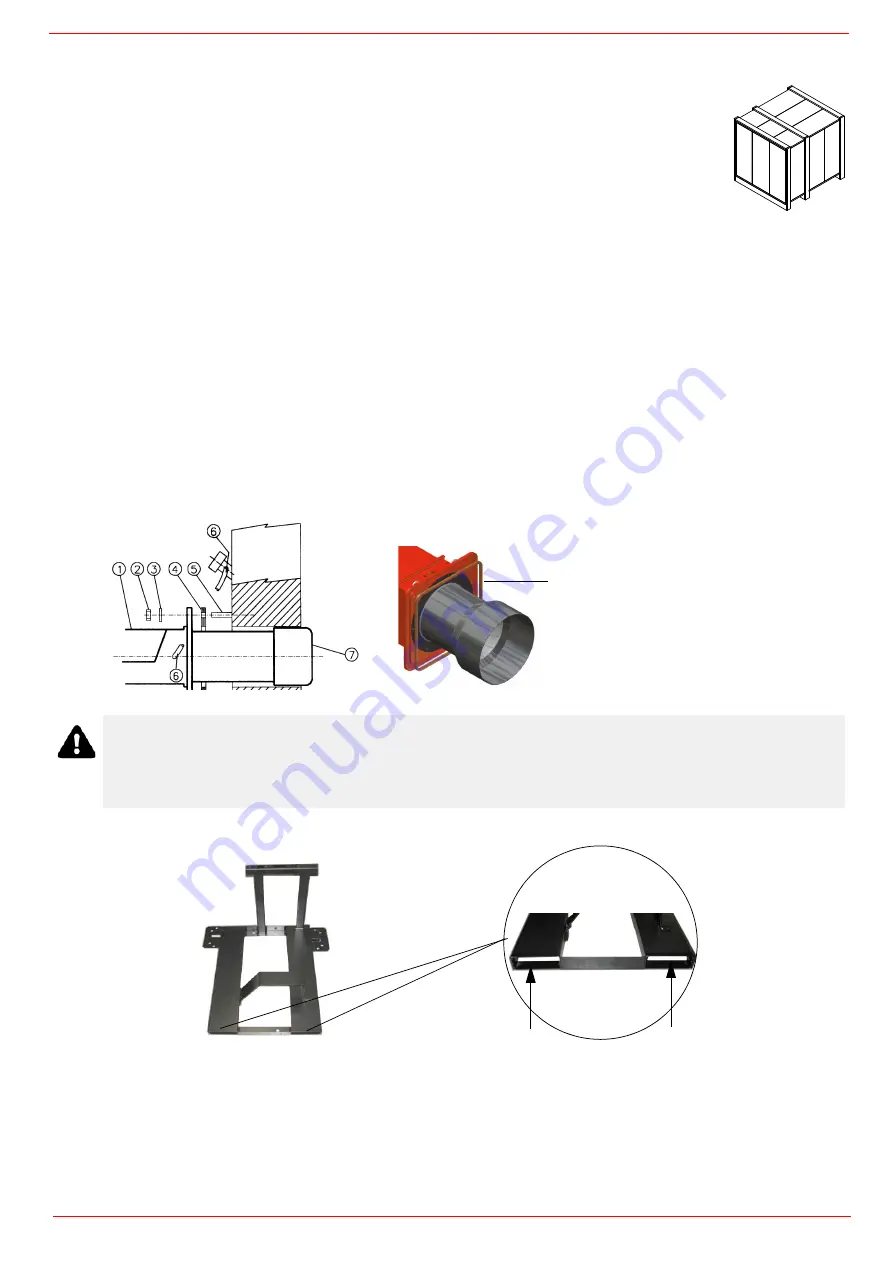
PART II: INSTALLATION
8
MOUNTINGS AND CONNECTIONS
Packing
The burners are dispatched in wooden packages whose dimensions are:
1730 mm x 1280 mm x 1020 mm (L x P x H)
Packing cases of this kind are affected by humidity and are not suitable for stacking. The following are pla-
ced in each packing case.
burner;
light oil flexible hoses;
light oil filter;
gasket to be inserted between the burner and the boiler;
envelope containing this manual.
To get rid of the burner’s packing, follow the procedures laid down by current laws on disposal of materials.
Fitting the burner to the boiler
To perform the installation, proceed as follows:
1
drill the furnace plateas decribed in paragraph (“Overall dimensions”);
2
place the burner towards the furnace plate: lift and move the burner by means of its eyebolts placed on the top side (see”Lifting and
moving the burner”);
3
screw the stud bolts (5) in the plate holes, according to the burner’s drilling plate described on paragraph “Overall dimensions”;
4
place the ceramic fibre rope on the burner flange (if necessary, use a spray adhesive on the flange).
5
install the burner into the boiler;
6
fix the burner to the stud bolts, by means of the fixing nuts, according to the picture below.
7
After fitting the burner to the boiler, ensure that the gap between the blast tube and the refractory lining is sealed with appropriate
insulating material (ceramic fibre cord or refractory cement).
Handling the burner
The burner is mounted on a support provided for handling the burner by means of a fork lift truck: the forks must be inserted into the A
anb B ways. Remove the stirrup only once the burner is installed to the boiler.
The burner is designed to work positioned according to the picture below. For different installations, please contact the Technical
Department.
WARNING! The handling operations must be carried out by specialised and trained personnel. If these
operations are not carried out correctly, the residual risk for the burner to overturn and fall down still
persists. To move the burner, use means suitable to support its weight (see paragraph “Technical spec-
ifications”).
The unpacked burner must be lifted and moved only by means of a fork lift truck.
H
P
L
Keys
1
Burner
2
Fixing nut
3
Washer
4
Ceramic fibre plait
5
Stud bolt
7
Blast tube
4
A
B