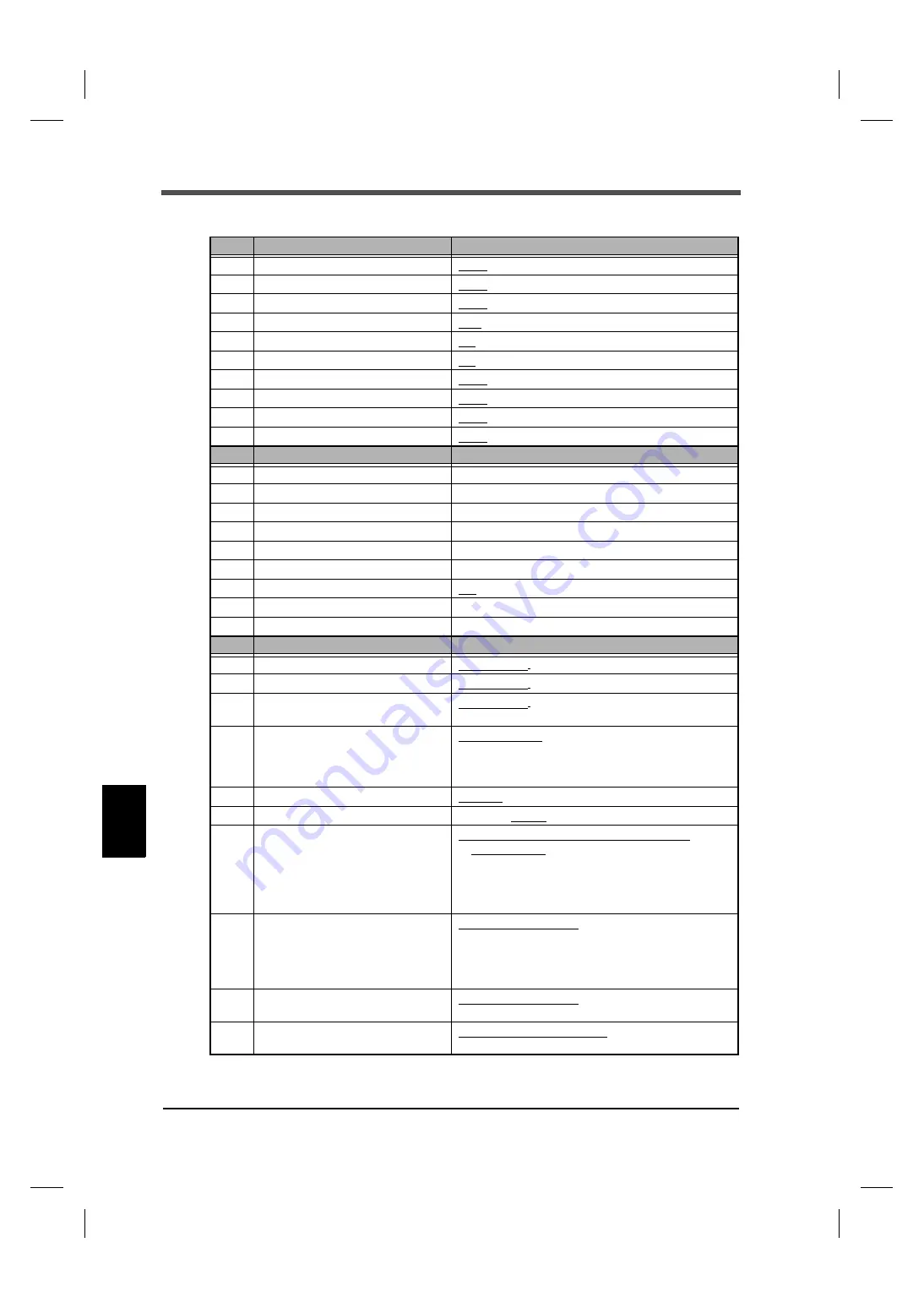
82
9
SUPPLEMENTS
82
SUPPLEMENTS
Chapter
9
■
Setting Range Details of the Set Value
Code
Function
Setting range
00
Final
00000 to 99999
01
Set point 1
00000 to 99999
02
Set point 2
00000 to 99999
03
Compensation (CPS)
0000 to 9999
04
Over
000 to 999
05
Under
000 to 999
06
Upper limit
00000 to 99999
07
Lower limit
00000 to 99999
08
Near zero
00000 to 99999
09
Preset tare value
00000 to 99999
Code
Function
Setting range
10
Comparison inhibit time
0.00 to 9.99
11
Judging time
0.00 to 9.99
12
Complete output time
0.00 to 9.99
13
Adjust feeding time
0.00 to 9.99
14
Auto zero times
00 to 99
15
Judging times
00 to 99
17
Auto free fall compensation coefficient
0: 1, 1: 3/4, 2: 1/2, 3: 1/4
18
Average count of auto free fall compensation
1 to 9
19
Auto free fall compensation regulation
00000 to 99999
Code
Function
Setting range
20
Over/Under comparison
0: Gross weight, 1: Net weight, 2: Comparison OFF
21
Upper/Lower limit comparison
0: Gross weight, 1: Net weight, 2: Comparison OFF
22
Near zero comparison
0: Gross weight, 1: Net weight, 2: Comparison OFF,
3: |Gross weight|, 4: |Net weight|
23
Feed/discharge control mode
0: Feeding control
1: Discharging control
2: External
3: Communication
24
Preset tare weight
0: Invalid, 1: Valid
25
Auto free fall compensation
0: Invalid, 1: Valid, 2: Communication
26
Complete output mode
0: ON by the complete output time after a lapse of
the judging time
1: ON by the complete output time after stability of
the weight value and a lapse of the judging time
2: ON by the complete output time after stability of
the weight value or a lapse of the judging time
27
Over/Under comparison mode
0: Continuous comparison
1: Comparison when the external judgment input is ON
2: Comparison when the complete signal is ON
3: Comparison, holding the weight value,
when the complete signal is ON
28
Upper/Lower limit comparison mode
0: Continuous comparison
1: Comparison when the external judgment input is ON
29
Net weight sign inversion in discharge
weighing
0: Display with the sign inverted
1: Display without inverting the sign