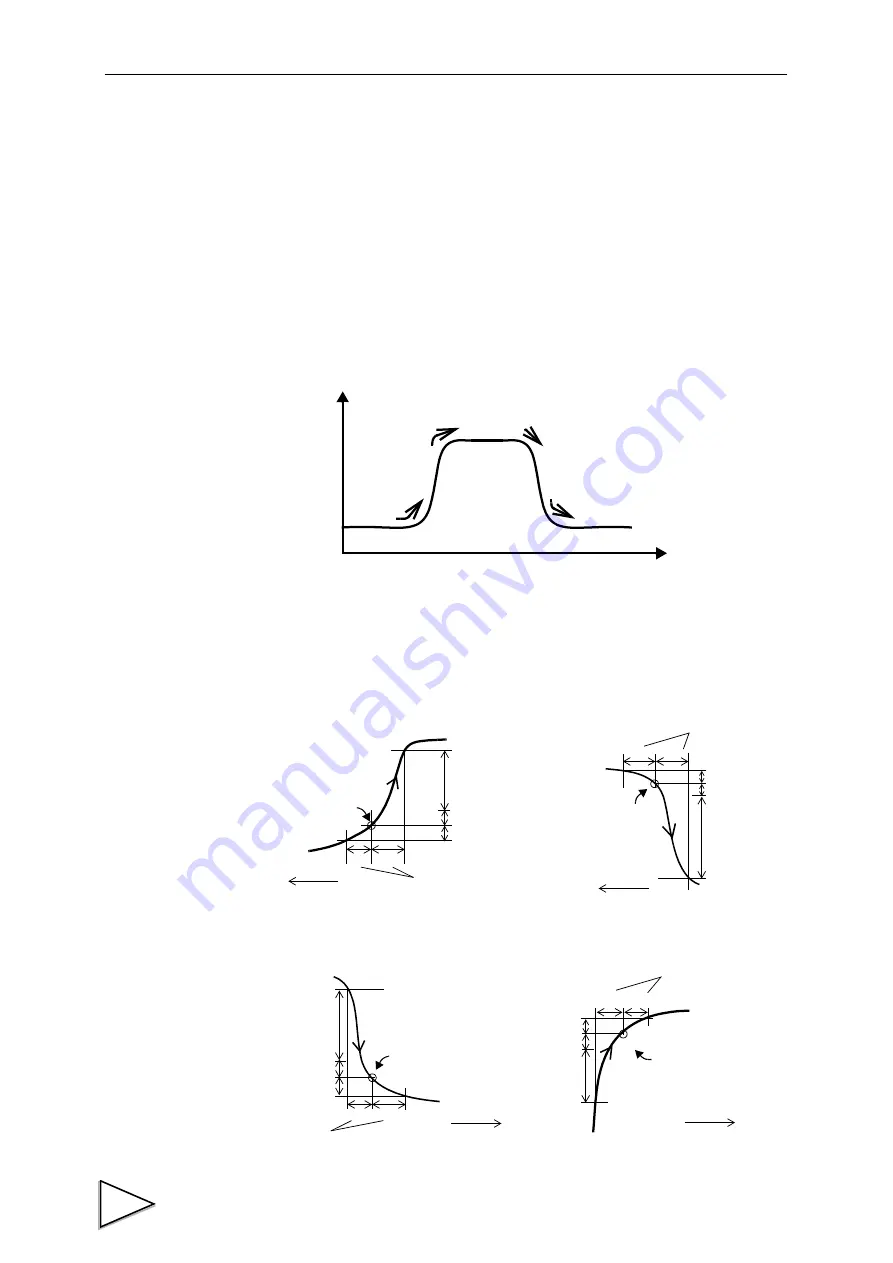
10.Multi-Hold Mode
57
10-3-9. Four Types of Inflection Point Hold
Detection starts when the H/M signal is input and the indicated value crosses over the
Hold Start Level. Detection is performed while the H/M signal is ON. The COMPLETE
output is made immediately when there is a minute slope. Therefore, if the Judgment
output is taken in immediately after the COMPLETE output is made, correct results may
not be able to be obtained as is the case with the peak hold.
Take in the Judgment output after determination of the hold by turning off the H/M
signal. The hold can be cancelled by turning on the T/H signal as a reset signal.
Each inflection point hold is explained by the method in "16-2-12. Minimum Slope
Detection Value / Slope Detection Interval A / Slope Detection Interval B / Preliminary
Slope Detection Point" P118. (Point a is held as an inflection point when the amount of
change D exceeds the set "Minimum Slope Detection Value".
+
+
+
+
Four types of Inflection Point Hold
Load
Time
Inflection Point Hold A
Inflection Point Hold B
Inflection Point Hold C
Inflection Point Hold D
A
B
D
C
C
a
a
A
B
C
C
D
Inflection Point Hold A
Inflection Point Hold B
Inflection Point Hold C
Inflection Point Hold D
A
B
a
D
C
C
A
B
D
C
C
a
Slope change point
Slope change point
Slope change point
Slope change point
Slope Detection
Intervals
Slope Detection Intervals
Slope Detection Intervals
Slope Detection
Intervals
Preliminary Slope
Preliminary Slope
detection point
Preliminary Slope
Detection Point
Detection Point
Preliminary Slope
detection point