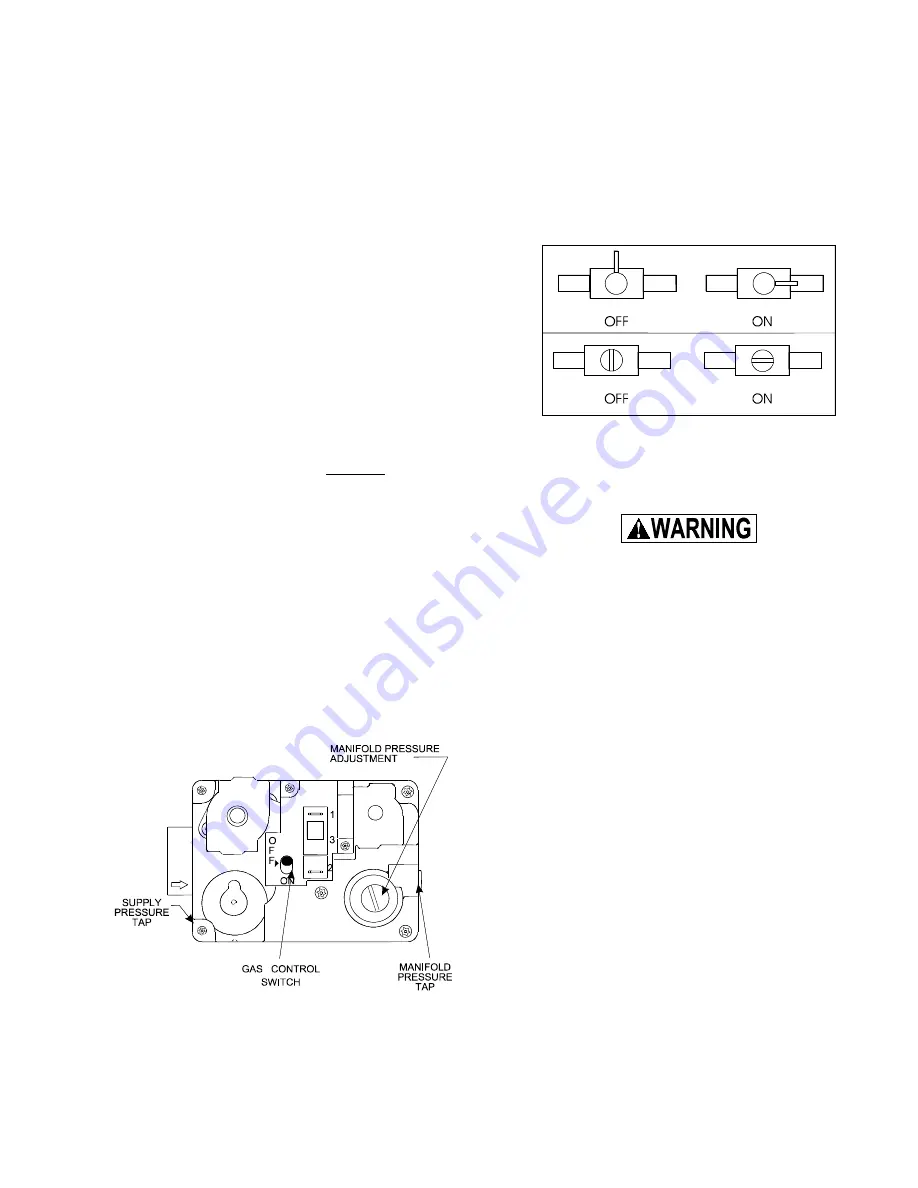
19
3. USE ONLY YOUR HAND TO MOVE THE GAS
CONTROL LEVER OR SWITCH. NEVER USE
TOOLS. IF THE LEVER OR SWITCH WILL
NOT MOVE BY HAND, DON’T TRY TO REPAIR
IT, CALL A QUALIFIED SERVICE TECHNI-
CIAN. FORCE OR ATTEMPTED REPAIR MAY
RESULT IN A FIRE OR EXPLOSION.
4. DO NOT USE THIS APPLIANCE IF ANY PART
HAS BEEN UNDER WATER. IMMEDIATELY
CALL A QUALIFIED SERVICE TECHNICIAN
TO INSPECT THE APPLIANCE AND TO RE-
PLACE ANY PART OF THE CONTROL SYS-
TEM AND ANY GAS CONTROL WHICH HAS
BEEN UNDER WATER.
Operating Instructions
1. STOP! Read the safety information listed above.
2. Set the thermostat to the lowest setting, or OFF.
3. Turn off all electric power to the furnace.
4. This appliance does not have a pilot. It is
equipped with an ignition device, which auto-
matically lights the burners. DO NOT try to light
the burners by hand.
5. Remove front door panel.
6. Move gas valve control lever or switch to "OFF".
See Figure 13.
7. Wait five (5) minutes to clear out any gas. Then
smell for gas, including near the floor. If you
smell gas, STOP! Follow "2" in the safety infor-
mation above. If you don’t smell gas, go to the
next step.
8. Move gas control lever or switch to "ON".
9. Replace front door panel.
10. Turn on all electric power to the furnace.
11. Set thermostat to desired setting.
FIGURE 13 – WHITE-RODGERS GAS VALVE
Gas Shutoff
This furnace is equipped with a gas shutoff lever or
switch on the gas valve, which can be used to
prevent gas from flowing to the furnace. Figure 13
shows the location of the shutoff lever or switch. To
turn off gas to the furnace, move the lever or switch
to the "OFF" position.
The furnace installation should also have a manual
shutoff valve in the gas piping to the furnace, similar
to what is shown in Figure 14. To turn off the gas to
the furnace, use a wrench and turn the switch or
lever so that it is pointing 90 degrees from the gas
pipe, as shown in Figure 14.
FIGURE 14 – MANUAL GAS SHUTOFF VALVE
INSTALLATION CHECKS
Checking Gas Input Rate
Natural gas heating values can vary widely. It is
the responsibility of the installer to make sure
that the input rate to the furnace as installed
does not exceed the nameplate rating of the
furnace. Failure to do so can cause heat ex-
changer failure, resulting in injury or death.
The maximum BTUH input capacity for each model
is shown on the furnace rating plate and in the
specification table. This input must not be exceeded.
The input shown may be used in geographic areas
where the elevation is from 0 to 2000 feet. The BTU
input depends on the calorific heating value of the
gas, orifice size, and manifold pressure. Orifice sizes
are based on gas values of 1050 BTU/cu. ft. for
natural gas and 2500 BTU/cu. ft. for LP (propane)
gas. The orifice sizes supplied with the furnace
should provide satisfactory input capacity for
installations in most areas, except at high altitude.
High Altitude Adjustment
In areas above 2000 feet elevation, the furnace BTU
input must be reduced 4% for each 1000 feet of
elevation above sea level. For minor input adjust-
ments, it is permissible to adjust the manifold
pressure at the gas valve pressure regulator. Do not
adjust the manifold pressure more than
±
.3" W.C.
from the specified regulator settings (3.5" for natural
gas and 10" for LP (propane gas). In many cases,
adjusting the gas valve manifold pressure may not
be enough to reduce the gas input enough for high
altitudes. In such cases, the gas orifices must be