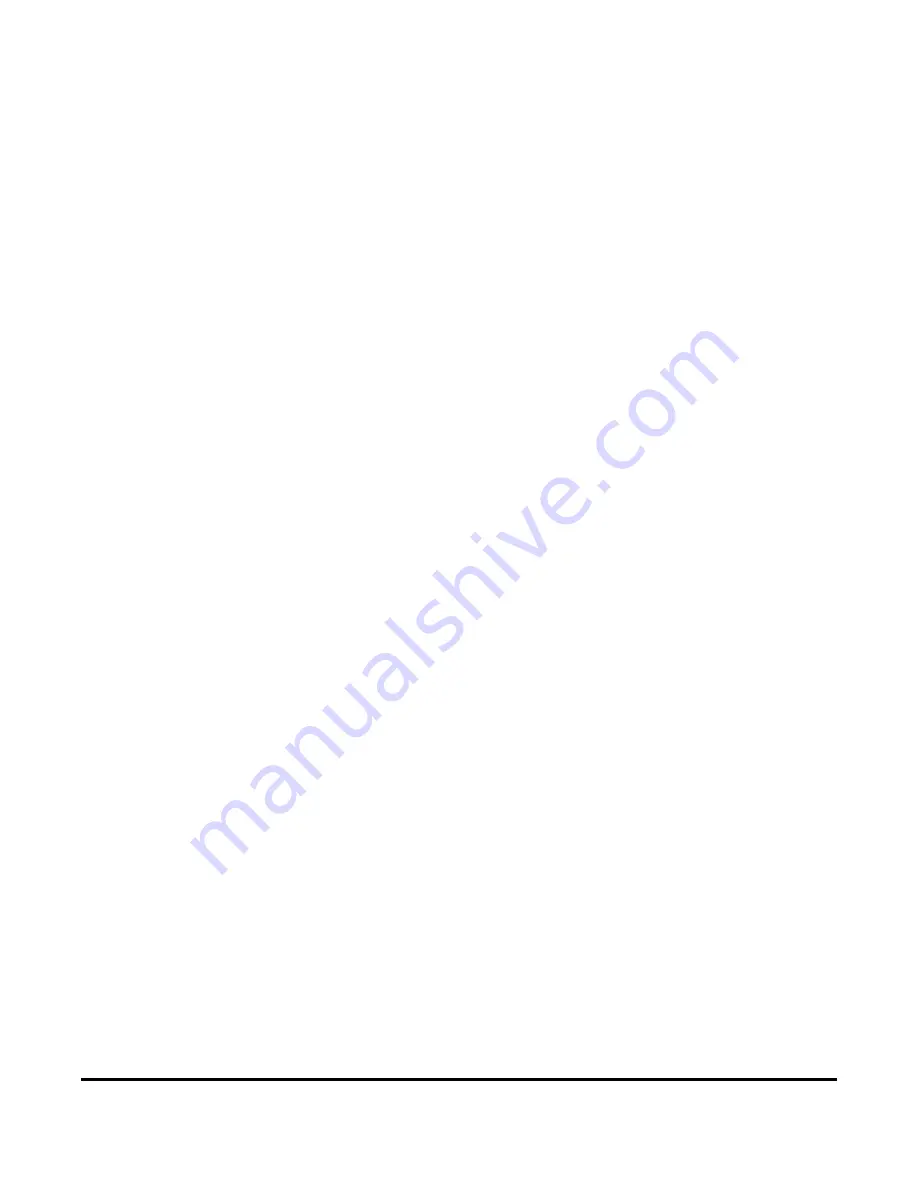
HF25D DC RESISTANCE WELDING SYSTEM
990-333
5-1
CHAPTER 5
MAINTENANCE
Section I. Introduction
General Kinds of Problems
It has been our experience that most resistance welding power supply ‘problems’ are caused by lack of
material control, process control and electrode tip surface maintenance. The problems that you might
encounter fall into two groups:
•
Soft
— The problem is transient, and you can correct it by resetting the system
or parameter limits. For example, you should ensure that:
−
Correct force is set at the weld head
−
Correct weld energy and time is set at the Control
−
The equipment is set up properly
−
All electrical connections are tight
−
Electrode alignment allows flush contact with the weld pieces
−
Electrodes are properly dressed
•
Hard
— The problem is embedded in the system and some form of repair will
be needed. For example, repair might include replacing a broken weld head
flexure.
Alarm Messages
Built-in automatic self-test and self-calibration routines will bring up alarm messages on the display
screens. These messages will usually let you know what action is required of you to correct the reason
for the alarm. For a complete listing of the alarm messages, what they mean, and corrective actions, see
Section II, Troubleshooting
.
Summary of Contents for HF25A
Page 9: ...HF25D DC RESISTANCE WELDING SYSTEM 990 333 ix ...
Page 10: ......
Page 20: ......
Page 84: ...CHAPTER 6 CALIBRATION HF25D DC RESISTANCE WELDING SYSTEM 990 333 6 4 Final Calibration Setup ...
Page 113: ......
Page 129: ......
Page 153: ......
Page 171: ......