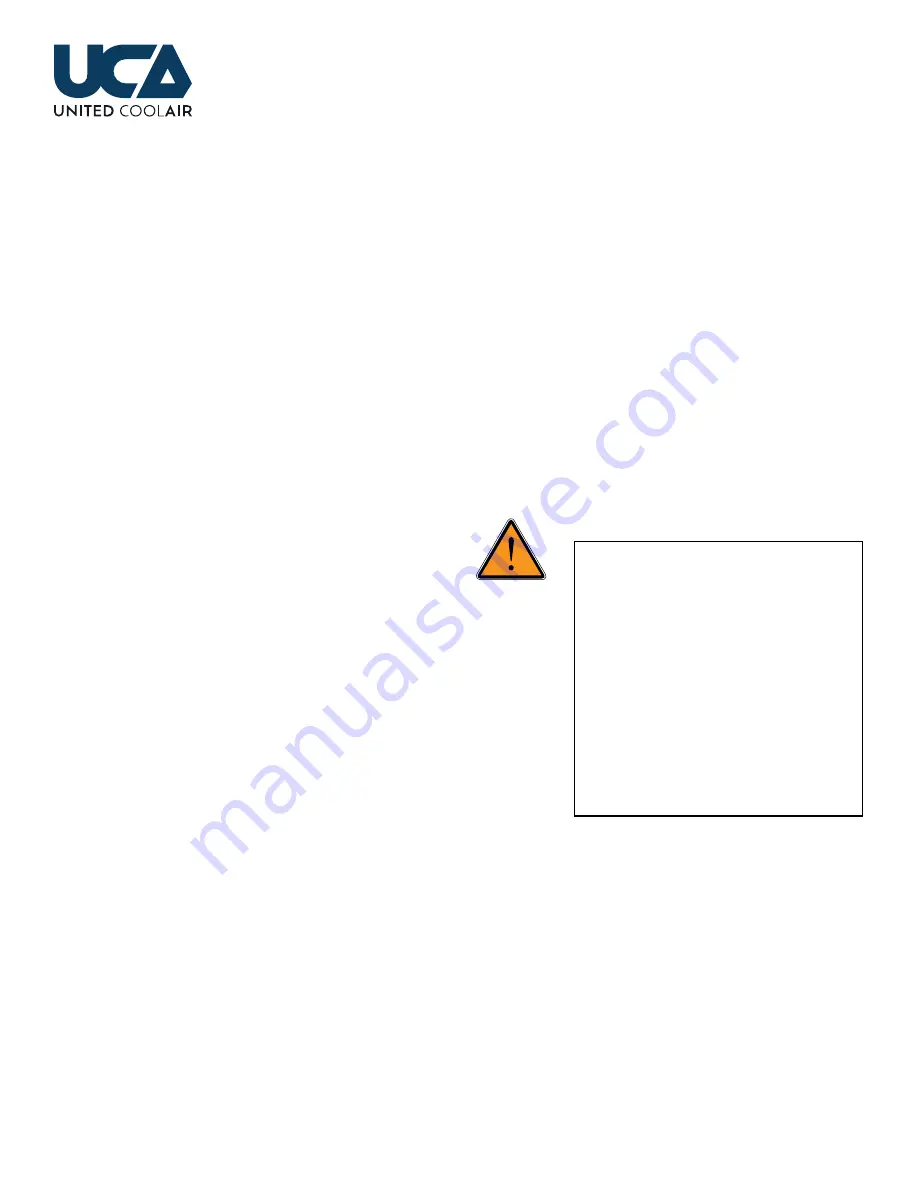
Installation, Operation and Maintenance Manual
VariCool EZ-Fit
36
Subject to change without notice.
Start-Up Procedures
(R-410a Systems)
1�
Start up must be performed by a qualified HVAC
Technician
2�
Make certain that all power is disconnected at the main
power circuit breaker or service disconnect before
starting any of this procedure
3�
Check all electrical screw terminals and wiring lugs
for tightness internal to the equipment Components
may have loosened due to vibration during transit
or handling Verify that the main power block lug
connections made in the field are tight and secure
4�
Confirm that the voltage rating of the equipment data
tag coincides with the power that will be delivered to
the unit
5�
Verify that the circuit protection for the unit satisfies
Local and National Codes according to the unit data
tag Minimum Circuit Ampacity (MCA) and Maximum
Fuse Size (MFS)
6�
Leak check the refrigerant system While the unit was
leak checked at the factory, leaks can develop during
transit and / or handling
7�
Confirm that the unit condensate has been adequately
trapped and taken to a suitable point for disposal
8�
Verify that the filters are in place, clean and usable
9�
Apply power to the unit Switch the circuit breaker or
field supplied electrical service disconnect switch to the
on position
NOTE: If the unit has crankcase heaters and the surrounding
ambient is 70˚ F or lower, let the compressors sit for
approximately 24 hours before proceeding�
10�
Record the voltage at the unit terminals
11�
On the wall controller, navigate to the system enables
menu Set the compressor to OFF Set the system
ON/OFF menu to the ON position
12�
Verify that the evaporator blower(s) are rotating in the
correct direction (three phase units only)
NOTE: If the evaporator blower motor runs backwards,
shut off all power to the unit. Switch any two of the
incoming power leads at the unit main power terminal
block. The unit has been wired and phased properly
at the factory� DO NOT change any factory wiring to
correct for a phase problem�
NOTE: Before conducting the following start up sections
connect a refrigerant gauge set to the unit Schrader
connections� Install temperature sensors or probes to
record the appropriate refrigerant line temperatures�
13�
Set the wall controller to a temperature set point
approximately 5˚ lower than the entering air
temperature This should energize the compressor(s)
NOTE: Dependent upon the options and/or the thermostat,
there may be a delay for the compressor(s) operation�
14�
While waiting for the compressor(s) to stabilize, record
the External Static Pressure (ESP) for the evaporator
blower
NOTE: Make sure all the unit access panels are in place when
taking these readings.
WARNING
HEAT EXCHANGER FREEZE RISK:
Heat Exchanger will fail if operated at or
near the freezing point of water/glycol
mixture
The following precautions must be taken:
• At startup, fluid side must be started
first
• At shutdown, refrigerant side must be
shut down first
• Fluid side outlet must have temperature
monitoring and emergency shutdown
equipment in case temperature
approaches too close to the freezing
point
15�
Verify that the incoming water / fluid pressure does not
exceed the rating for the water / fluid control valves
16�
Verify that the unit piping and heat exchangers will not
be subjected to freezing conditions
17�
Confirm that no joints are leaking in the cooling fluid
circuit(s)
18�
Document the type of fluid being used as the cooling
medium If glycol is being used, make sure the mixture
is adequate for any low ambient conditions that may be
possible
Continued on next page
Summary of Contents for VariCool EZ-Fit Series
Page 2: ......