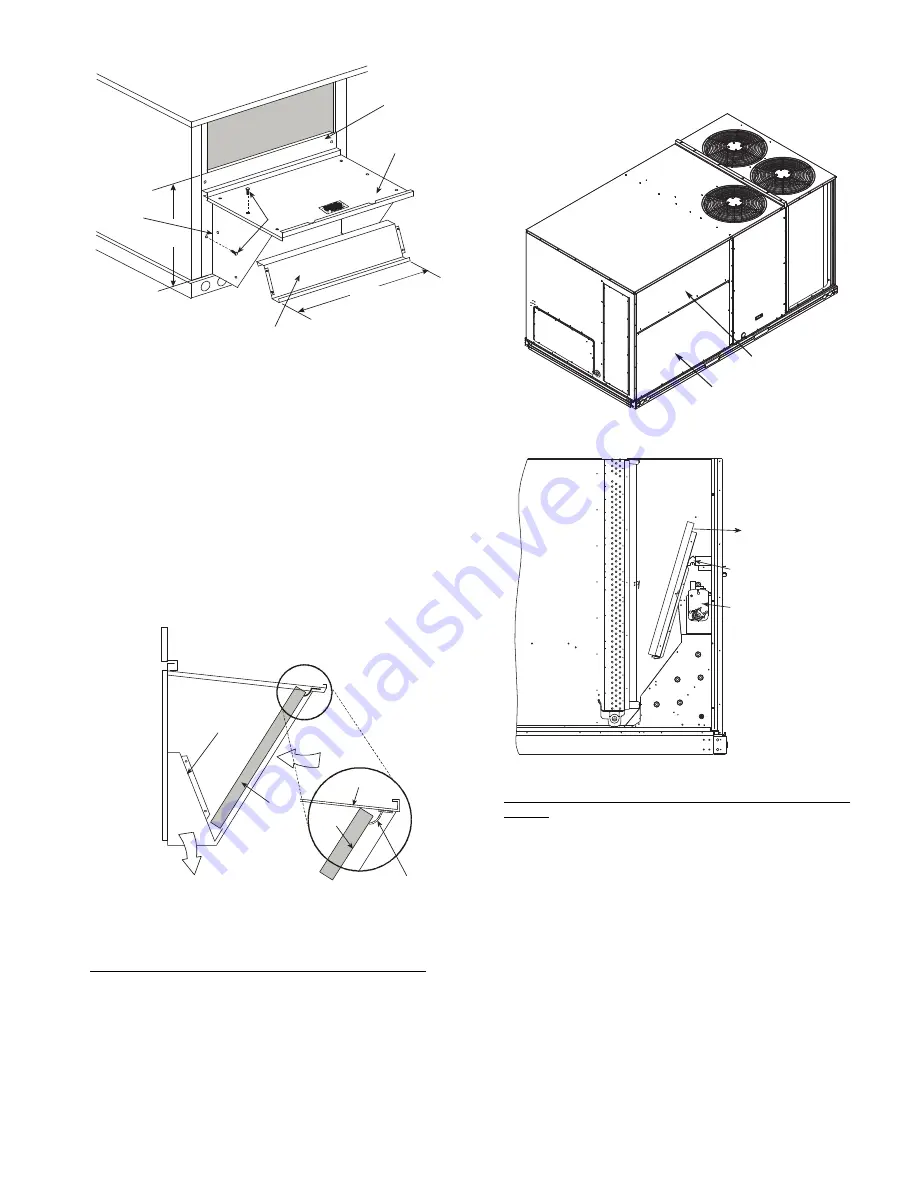
17
Fig. 16 — Economizer Hood Construction
3. Remove the shipping tape holding the economizer baro-
metric relief damper in place (economizer only).
4. Insert the hood divider between the hood sides. See
Fig. 16 and 17. Secure hood divider with 2 screws on
each hood side. The hood divider is also used as the bot-
tom filter rack for the aluminum filter.
5. Open the filter clips which are located underneath the
hood top. Insert the aluminum filter into the bottom filter
rack (hood divider). Push the filter into position past the
open filter clips. Close the filter clips to lock the filter into
6. Caulk the ends of the joint between the unit top panel and
the hood top.
7. Replace the filter access panel.
Fig. 17 — Economizer Filter Installation
50TC 16 UNIT SIZE
Economizer Hood Removal and Setup (Factory Option)
1. The hood is shipped in knock-down form and located in
the return air compartment. It is attached to the economiz-
er using two plastic tie-wraps.
2. To gain access to the hood, remove the filter access panel.
3. Locate and cut the (2) plastic tie-wraps, being careful to
not damage any wiring. (See Fig. 19.)
4. Carefully lift the hood assembly through the filter access
opening and assemble per the steps outlined in Econo-
mizer Hood and Two–Position Hood section.
Fig. 18 — Typical Access Panel Locations
Fig. 19 — Economizer Hood Package Location
Two Position Damper Hood Removal and Setup -factory
Option
1. The hood is shipped in knock-down form and assem-
bled to a metal support tray using plastic stretch wrap.
Located in the return air compartment, the assembly’s
metal tray is attached to the basepan and also attached
to the damper using two plastic tie-wraps.
2. To gain access to the hood, remove the filter access panel.
3. Locate the (2) screws holding the metal tray to the base-
pan and remove. In order to remove the screws, it may be
necessary to remove the panel underneath the two-posi-
tion damper. Remove the two screws. Locate and cut the
(2) plastic tie-wraps securing the assembly to the damper.
(See Fig. 19.) Be careful to not damage any wiring or cut
tie-wraps securing any wiring.
4. Carefully lift the hood assembly (with metal tray) through
the filter access opening and assemble per the steps out-
lined in Economizer Hood and Two–Position Hood sec-
tion.
5. If removed, reattach the panel under the damper.
B
TOP
PANEL
INDOOR COIL
ACCESS PANEL
19 1/16”
SCREW
HOOD DIVIDER
LEFT
HOOD
SIDE
33 3/8”
(848mm)
(483mm)
DIVIDER
BAROMETRIC
RELIEF
CLEANABLE
ALUMINUM
FILTER
FILTER
HOOD
FILTER
CLIP
OUTSIDE
AIR
FILTER ACCE
SS
PANEL
INDOOR COIL ACCESS PANEL
Economizer
Cut Plastic Ties
(2) Places
Remove Hood Parts
Summary of Contents for Carrier WeatherMaker 50TC A08 Series
Page 4: ...4 Fig 2 Unit Dimensional Drawing Size 08 09 12 Units...
Page 5: ...5 Fig 2 Unit Dimensional Drawing Size 08 09 12 Units cont...
Page 6: ...6 Fig 3 Unit Dimensional Drawing Size 14 Unit...
Page 7: ...7 Fig 3 Unit Dimensional Drawing Size 14 Unit cont...
Page 9: ...9 Fig 4 Unit Dimensional Drawing Size 16 Unit cont...
Page 13: ...13 Fig 8 Roof Curb Details Size 16 Unit...
Page 50: ...50 Fig 73 50TC 16 Control Box Component PremierLink Locations...
Page 51: ...51 Fig 74 Typical PremierLink Control Wiring Diagram...
Page 52: ...52 Fig 75 Typical PremierLink Control Wiring Diagram with Humidi MiZer System Option...
Page 64: ...64 Fig 106 Typical RTU Open Controller Wiring Diagram 50TC 08 14 Size Units...
Page 65: ...65 Fig 107 Typical RTU Open Controller Wiring Diagram 50TC 16 Size Unit...