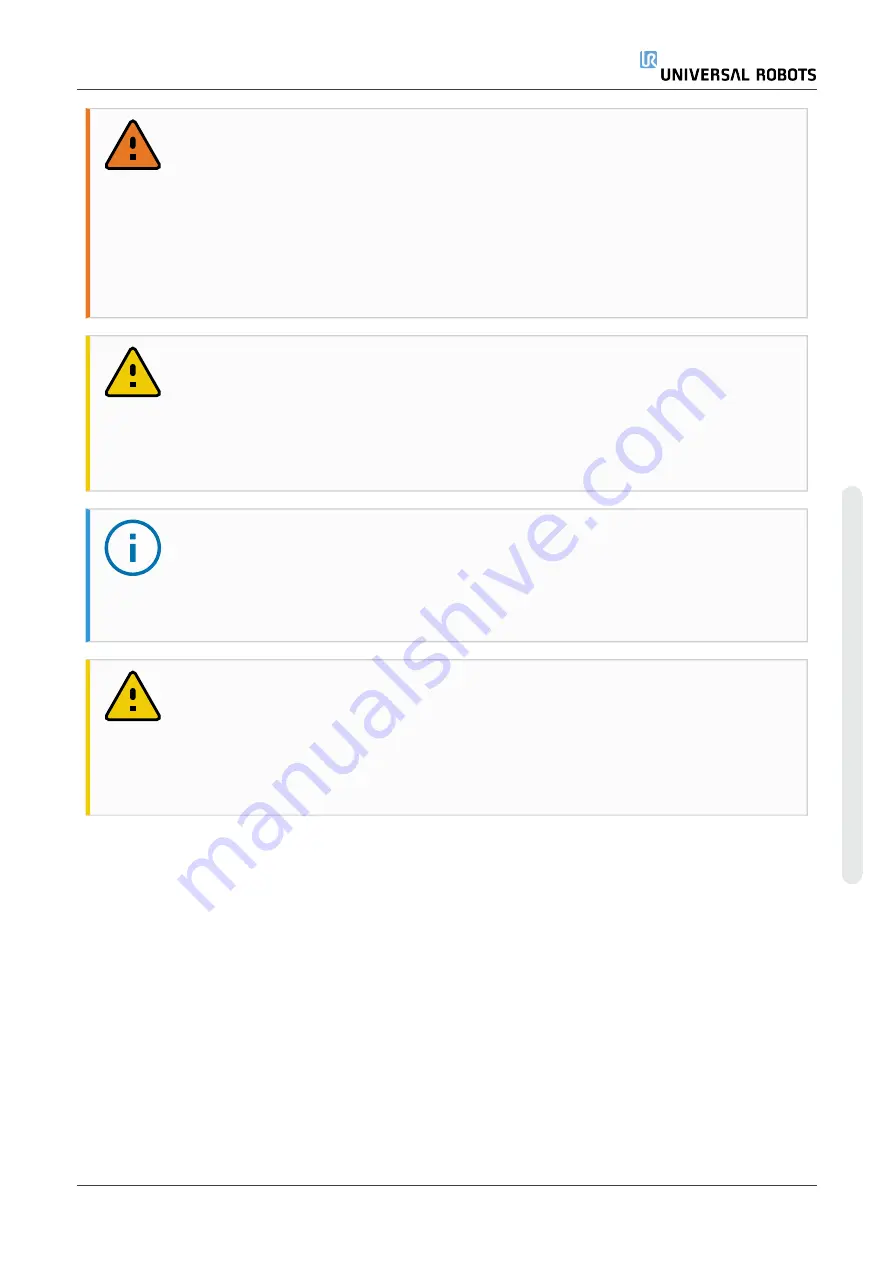
WARNING
Incorrect connection of the power source or ground wires may result in
equipment damage or personnel injury.
Damage caused by invalid power source connection is not covered by warranty.
Before starting the operation:
l
Ensure that the power source wiring is correct.
l
Ensure that the grounding is correct.
CAUTION
Failure to perform installation or maintenance correctly may result in equipment
damage or personnel injury.
l
Only qualified personnel must perform installation, start-up, and
maintenance.
NOTICE
ESD can damage sensitive components in the OEM Control Box.
l
Always wear an ESD wrist strap when working with the OEM Control Box
electrical interfaces.
CAUTION
Failure to perform a risk assessment before installing and operating the OEM
Control Box may result in equipment damage or personnel injury.
l
Perform a risk assessment before installing and operating the OEM Control
Box.
Installation Guide
3
OEM Control Box
2. Safety
C
o
p
yr
ig
h
t
©
2
0
1
9
b
y
U
n
iv
e
rs
a
l
R
o
b
o
ts
A
/S
.
A
ll
ri
g
h
ts
re
s
e
rv
e
d
.