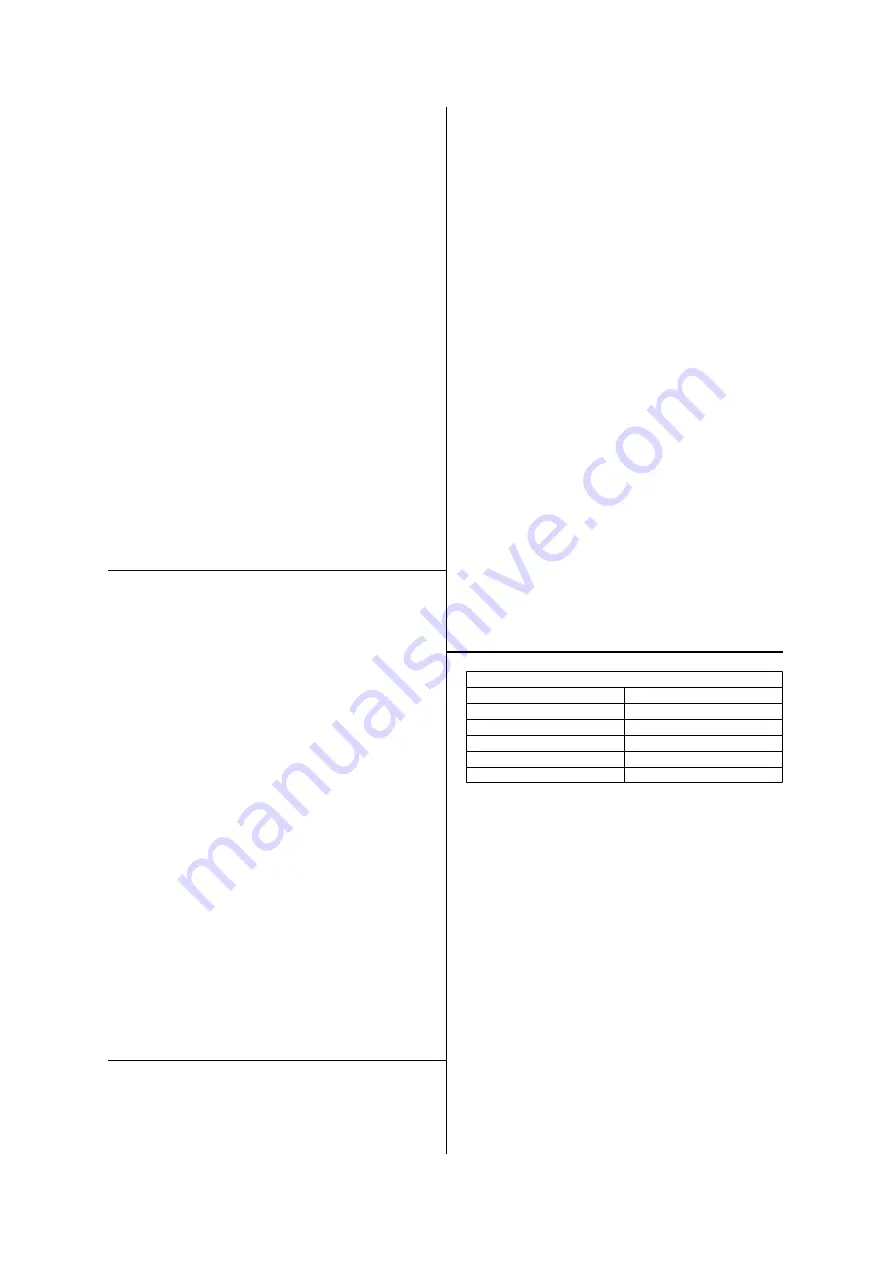
Page No 2
Safety Rules For A Sander
1) Read all the instructions before using this tool. All operators must be
fully trained in its use and aware of these safety rules.
2) Do not exceed the maximum working air pressure.
Operating
Select a suitable abrasive belt of the required grade to achieve a fine
sanded finish or high metal removal. The belt size for this tool is 20
mm wide x 525 circumference (continuous belt) and is available in
various grades, the lowest is grade 40 grit which is coarse for high
material removal and grits are available as 40, 50, 60, 80, 100 and
120. The coarseness of the grit decreases as the grade number
increases, hence 40 is coarse and 120 very fine.
To fit a belt, press down the tension bar and push the idle pulley
towards the tool until the tension bar clicks into place which releases
the tension and holds the tension off the belt. Fit the belt ensuring that
it sits centrally on the drive pulley and the idle pulley. Release the
tension bar to tighten the belt. Start the tool slowly and use the
adjusting screw (2A) to align the belt centrally.
Apply the sander lightly to the work and allow the belt to cut. Take
great care when sanding around sharp edges and corners to avoid
snagging and belt damage or breakage. It is always recommended to
use safety glasses and a breathing mask. The sanding of certain
materials may create a hazardous dust which may require special
breathing equipment. Check before using the tool.
Even if the tool has a low noise level, the actual sanding process may
create a noise such that hearing protectors should be worn.
If there are sharp edges on the material being sanded then safety
gloves are recommended.
Do not continue to use belts that are clogged or worn as this will
make the sanding process inefficient and the need to apply
unnecessarily high loads to the tool.
Only use belts of the dimensions specified. To use an incorrect belt
will either cause it to break or fly off. Both occurrences could be
dangerous.
Dismantling & Assembly Instructions
Disconnect tool from air supply.
Press on belt at idle pulley (2) position towards tool and idle pulley
bracket (1) will click into a holding position taking the tension off of the
belt to allow the belt to be taken off. Note that a new belt is fitted in
a similar way and tension bar (14) is pressed after the belt has been
fitted to tension the belt. With a screwdriver located in the idle pulley
assembly (2) unscrew nut. Unscrew hexagon socket head bolt (2A).
Remove finger pad assembly (4) by removing holding cap screw.
Remove hexagon socket head bolt (6) and take off flat shoe (10).
Remove key bolt (5) and drive out lever pins (16) and (17) and take
out tension bar (14) and spring (15). Pull out idle pulley bracket (1) and
spring (3). Grip drive pulley (9) and unscrew bolt (8) with washer (8A)
and prise off drive pulley (9) with key (22).Pull out dust cover (12).
Unscrew bolt (11) and slide off guard body (13). Grip housing (18)
and unscrew cap (23). Tap the end of rotor (28) to drive the complete
motor assembly out of the end of housing (18). Grip end plate (20)
and insert a punch into the threaded hole in rotor (28) and tap the
punch to drive the rotor (28) through end plate assembly (20). Take
off cylinder (26), spacer (21) and 5 off rotor blades (27) (one set) from
rotor (28). Locate end plate (25) on the cylinder side and tap the end
of the rotor to drive it though end plate (25) assembly. Tap out bearing
(19) from end plate (20) and bearing (24) from end plate (25). Drive
out pin (30) and remove lever (29). Unscrew air inlet with screen (39)
and take off deflector (38). Unscrew valve body (31) and take out
O-rings (32) (33) (34) and (36), valve stem (35) and valve spring (36).
Reassembly
Clean all parts and examine for damage and wear. Replace any part
with parts obtained from the manufacturer or an approved
representative. Coat all parts with a pneumatic tool lubricating oil and
assemble in reverse order. Fit new belt - see section Operating.
3) Use personal safety equipment.
4) Use only compressed air at the recommended conditions.
5) If the tool appears to malfunction remove from use immediately
and arrange for service and repair.
6) If the tool is used with a balancer or other support device ensure
that it is fixed securely.
7) Always keep hands away from the working attachment fitted to the
tool.
8) The tool is not electrically insulated. Never use the tool if there is any
chance of it coming into contact with live electricity.
9) Always when using the tool adopt a firm footing and/or position
and grip the tool firmly to be able to counteract any forces or reaction
forces that may be generated whilst using the tool.
10) Use only correct spare parts. Do not improvise or make
temporary repairs.
11) Do not lock, tape, wire, etc. the on/off valve in the run position.
The trigger/lever etc. must always be free to return to the ‘off’ position
when it is released.
12) Always shut off the air supply to the tool, and depress the
trigger/lever etc. to exhaust air from the feed hose before fitting,
adjusting or removing the working attachment.
13) Check hose and fittings regularly for wear. Replace if necessary.
Do not carry the tool by its hose and ensure the hand is remote from
the on/off control when carrying the tool with the air supply connected.
14) Take care against entanglement of moving parts of the tool with
clothing, ties, hair, cleaning rags, etc. This will cause the body to be
drawn towards the tool and can be very dangerous.
15) It is expected that users will adopt safe working practices and
observe all relevant legal requirements when installing, using or
maintaining the tool.
16) Do not install the tool unless an easily accessible and easily
operable on/off valve is incorporated in the air supply.
17) Take care that the tool exhaust air does not cause a problem or
blows on another person.
18) Never lay a tool down unless the working attachment has
stopped moving.
Technical Specification
Length (Folded)
340 mm (13.38")
Length (Max)
345 mm (13.58")
Height
65 mm (2.56")
Air Inlet
1/4" NPT
Air Consumption
4.0 CFM
Standard Belt Size
20 mm wide x 525 mm