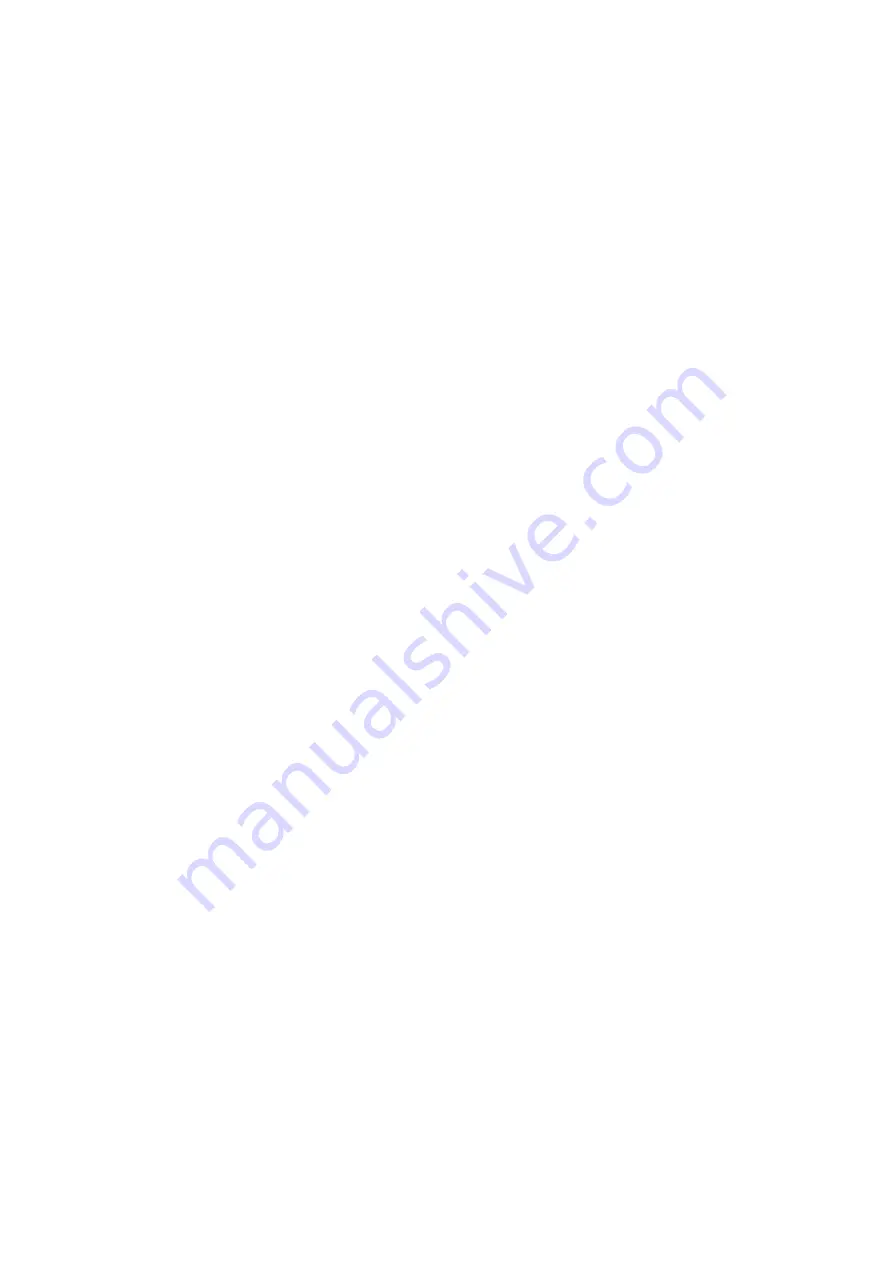
92
-Maintain the undercarriage, steering wheel and brake units properly functioning;
-Follow road safety rules and apply efficient driving methods considering road conditions,
strictly comply with operation norms of tires with regulated air pressure described in “Warnings” and
“Truck Driving” paragraphs.
4.3.3.1 Maintenance.
Check tire air pressure every day before driving, and pump it to the norm, if necessary.
Tire air pressure is set (designated) for completely loaded truck and is checked in cold tires.
Check tire, wheel and fasteners conditions at daily maintenance. Tires should not have
damages, non-repaired local damages (bottoming, cuts), local thread and side wall separation, and
wheels should not have mechanical damages, corrosion or cracks. Wear of tires should suit for opera-
tion. Remove foreign objects stuck in the thread and side wall. Tire tube valves must be fault-free.
Check that fuel, oil and other petrochemicals do not get to the tires, because they destroy
rubber.
If any faults are detected in tires and wheels, take measures to repair or replace the parts.
When strong or uneven thread wear is detected, which is usually caused, apart from wrong
driving, by truck undercarriage failure, steering wheel or brake failure, find its causes and remedy the
failure.
Wheel fasteners loosening and truck operation is forbidden, if at least one wheel fixation nut
or pin is absent or fixing holes of discs are worn.
Every time when mounting the wheel on boss, independent of disassembly reason, fasten
wheel retaining nuts twice: first time after 100-150 km and second time after 200-300 km.
When performing second truck maintenance, check general wheels and tires condition, if
any defect is detected, repair or replace it, swap, fasten wheel retaining nuts, if necessary and if
wheels with tires were not disassembled from the truck. Besides, when wheels are worn and steering
lever is repaired or replaced, toe-in angle adjustment should be checked, all pipelines and hoses of
tire pressure control system should be aired.
4.3.3.2 Tire Fitting
When assembling and disassembling tires follow the rules:
- completely deflate the tires;
- fit the tires in a special area with dedicated equipment, tools and devices; when in field
conditions, use the tools from the driver’s tool kit, herein, take measures to avoid sand and dirt com-
ing inside the tires;
- tire casing and tire flaps should be clean and dry;
Summary of Contents for 4320M
Page 1: ...URAL 4320М TRUCK and its Modifications ...
Page 106: ......
Page 110: ......
Page 159: ...156 Figure 123 Engine Electronic Control Unit Wiring Scheme ...
Page 165: ......
Page 167: ......
Page 173: ......
Page 177: ...Figure 140 Installation of left and right side safety devices 171 ...
Page 201: ......
Page 203: ......
Page 205: ......
Page 207: ......
Page 209: ......
Page 212: ......
Page 214: ......
Page 216: ......
Page 218: ......
Page 220: ......
Page 222: ......
Page 224: ......
Page 226: ......
Page 228: ......
Page 230: ......
Page 232: ......
Page 234: ......
Page 236: ......
Page 238: ......
Page 240: ......
Page 242: ......
Page 244: ......
Page 246: ......
Page 248: ......
Page 250: ......
Page 252: ......
Page 254: ......
Page 256: ......
Page 257: ...223 ...
Page 259: ......
Page 315: ...280 ...
Page 317: ......