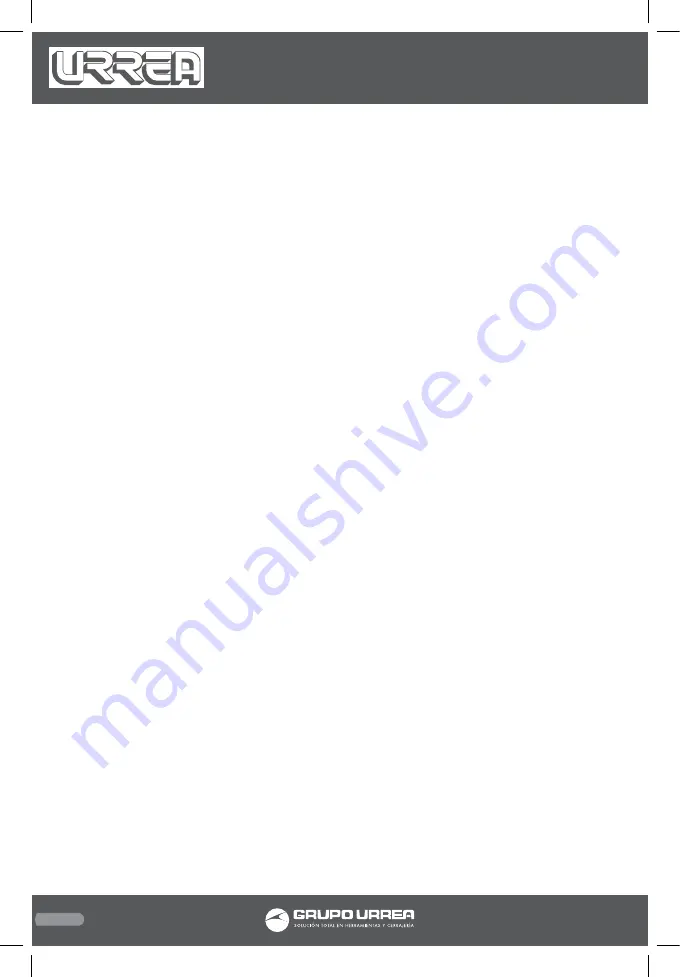
24
Drive belts too tight or misaligned. Adjust
belts to proper tension and alignment.
Compressor valves leaky, broken, carbonized
or loose. Inspect valves. Clean or replace as re-
quired. Install Valve/Gasket Step. Saver Kit.
Wrong beltwheel direction of rotation. Check
motor wiring for proper connections. Reverse
two leads on three-phase motors.
COMPRESSOR WILL NOT UNLOAD CYCLE
Leaking, broken or worn inlet unloader parts.
Inspect parts and replace as required.
Auxiliary valve dirty or seats worn. Inspect
parts. Clean, adjust or replace as required.
Leaking or maladjusted centrifugal pilot valve.
Replace pilot valve o-ring. Adjust pilot valve.
COMPRESSOR WILL NOT UNLOAD WHEN
STOPPED
Leaking or maladjusted centrifugal pilot valve.
Replace pilot valve o-ring. Adjust pilot valve.
Pressure switch unloader leaks or does not
work. Realign stem or replace.
EXCESSIVE NOISE DURING OPERATION
Loose beltwheel or motor pulley, excessive
end play in motor shaft or loose drive belts.
Check beltwheel, motor pulley, crankshaft,
drive belt tension and alignment. Repair or re-
place as required.
Lubricant viscosity too high. Drain existing lu-
bricant and refill with proper lubricant.
Compressor valves leaky, broken, carbonized
or loose. Inspect valves. Clean or replace as re-
quired. Install Valve/Gasket Step. Saver Kit.
Automatic drain valve clogged, leaking or de-
fective. Inspect valve and clean, repair or re-
place as required.
Defective ball bearings on crankshaft or motor
shaft. Inspect bearings and replace if required.
Install Bearing/Connecting Rod. Step Saver Kit.
Leaking check valve or check valve seat blown
out. Replace check valve.
Automatic start and stop mode is not suitable
for air demand. Adjust auxiliary valve for con-
stant speed operation
EXCESSIVE STARTING AND STOPPING
Air leaks in air discharge piping. Check tubing
and connections. Tighten joints or replace as
required.
Pressure switch differential too narrow. Adjust
pressure switch to increase differential, if dif-
ferential adjustment provided. Install pressure
switch with differential adjustment feature if
differential adjustment is desired.
Automatic drain valve clogged, leaking or de-
fective. Inspect valve and clean, repair or re-
place as required.
Automatic start and stop mode is not suitable
for air demand. Adjust auxiliary valve for con-
stant speed operation
Maladjusted or defective hydraulic unloader
valve Replace hydraulic unloader valve assem-
bly.
KNOCKS OR RATTLES
Loose beltwheel or motor pulley, excessive
end play in motor shaft or loose drive belts.
Check beltwheel, motor pulley, crankshaft,
drive belt tension and alignment. Repair or re-
place as required.
Compressor valves leaky, broken, carbonized
or loose. Inspect valves. Clean or replace as re-
quired. Install Valve/Gasket Step. Saver Kit.
Carbon build-up on top of piston(s). Clean
piston(s). Repair or replace as required.
Cylinder(s) or piston(s) scratched, worn or
scored. Repair or replace as required.
Connecting rod, piston pin or bearings worn
or scored. Inspect all. Repair or replace as re-
quired. Install Bearing/Connecting Rod.
Loose bearing spacer on crankshaft. Step Saver
Kit.
Defective ball bearings on crankshaft or motor
shaft. Inspect bearings and replace if required.
Install Bearing/Connecting Rod. Step Saver Kit.
LIGHTS FLICKER OR DIM WHEN RUNNING
Improper line voltage. Check line voltage and
upgrade lines as required. Contact electrician.
Wiring or electric service panel too small. In-
stall properly sized wire or service box. Contact
electrician.
Poor contact on motor terminals or starter
connections. Ensure good contact on motor
terminals or starter connections.
Improper starter overload heaters. Install
proper starter overload heaters. Contact elec-
trician.
Poor power regulation (unbalanced line). Con-
tact power company.
COMP95XX manual.indd 24
23/06/15 14:27