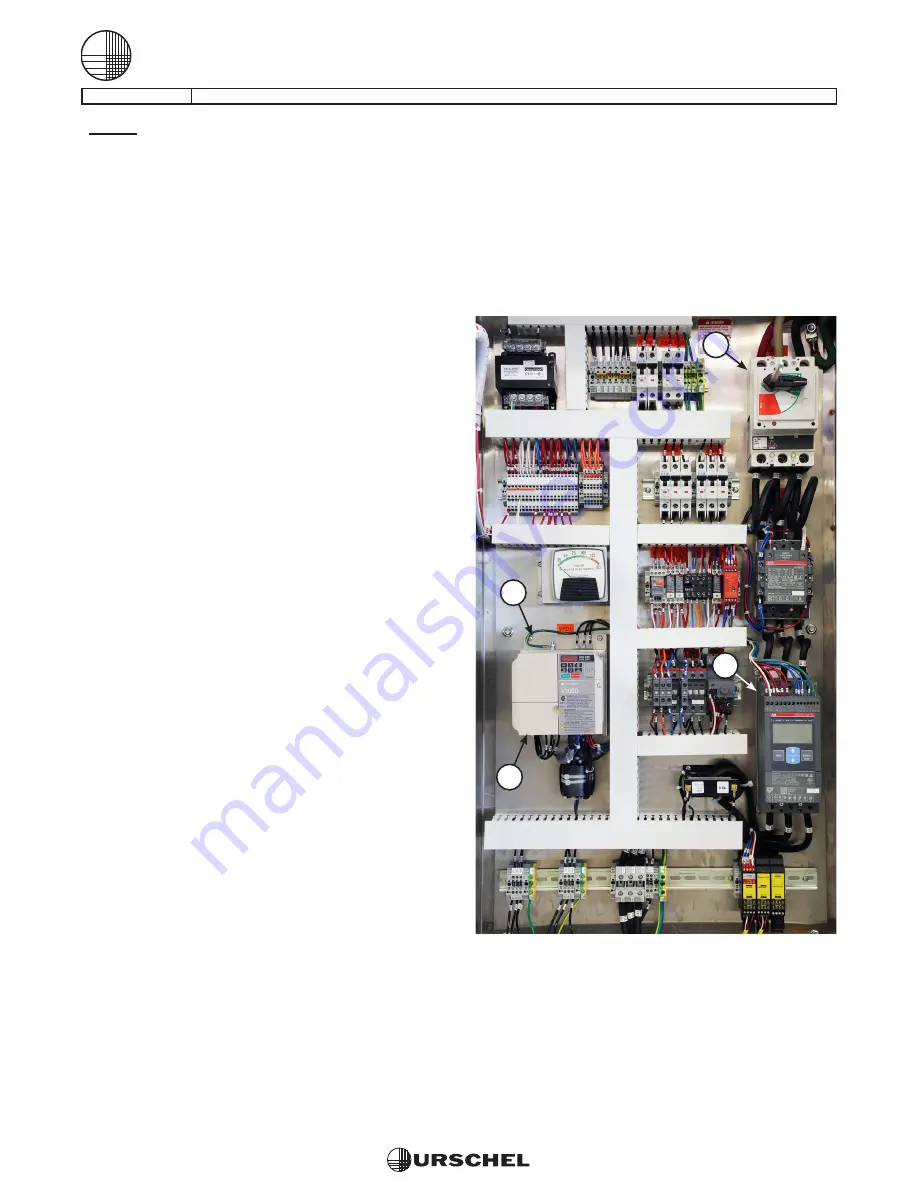
Addendum
A.10
Manual Page Number
Revision
Maintenance, Electrical Assembly: The current electrical enclosure is shown
to the right. Note the
variable frequency drive (1)
for the feed screw motor,
power line filter (2)
, and
main circuit breaker with disconnect switch (3)
.
The machine is supplied with a
soft start controller (4)
. The soft start
controls the inrush of current to the impeller motor when the impeller start
button is pressed. This is intended to reduced stress on the motor and motor
shaft, and prevent a voltage dip in the power supply. See the soft start
manufacturer's information included with the machine for more information.
1
2
3
4
Summary of Contents for COMITROL 2100
Page 2: ......
Page 28: ...Addendum A 26 This page intentionally left blank...
Page 84: ...6 This page intentionally left blank...
Page 94: ...16 This page intentionally left blank...
Page 95: ...17 GENERAL INFORMATION...
Page 101: ...23 INSTALLATION...
Page 104: ...26 This page intentionally left blank...
Page 110: ...32 This page intentionally left blank...
Page 131: ...53 PARTS...
Page 132: ...54 This page intentionally left blank...
Page 134: ...56 PARTS Tools See the Addendum for updated information...
Page 138: ...60 PARTS Agitator Feed Screw See the Addendum for updated information...
Page 146: ...PARTS Motor and Drive Parts 68 See the Addendum for updated information...
Page 148: ...PARTS Electrical Assembly NEMA 70 See the Addendum for updated information...
Page 152: ...PARTS Electrical Assembly CE compliant 74 See the Addendum for updated information...
Page 156: ...78 PARTS Electrical Assembly Switches See the Addendum for updated information...
Page 165: ......