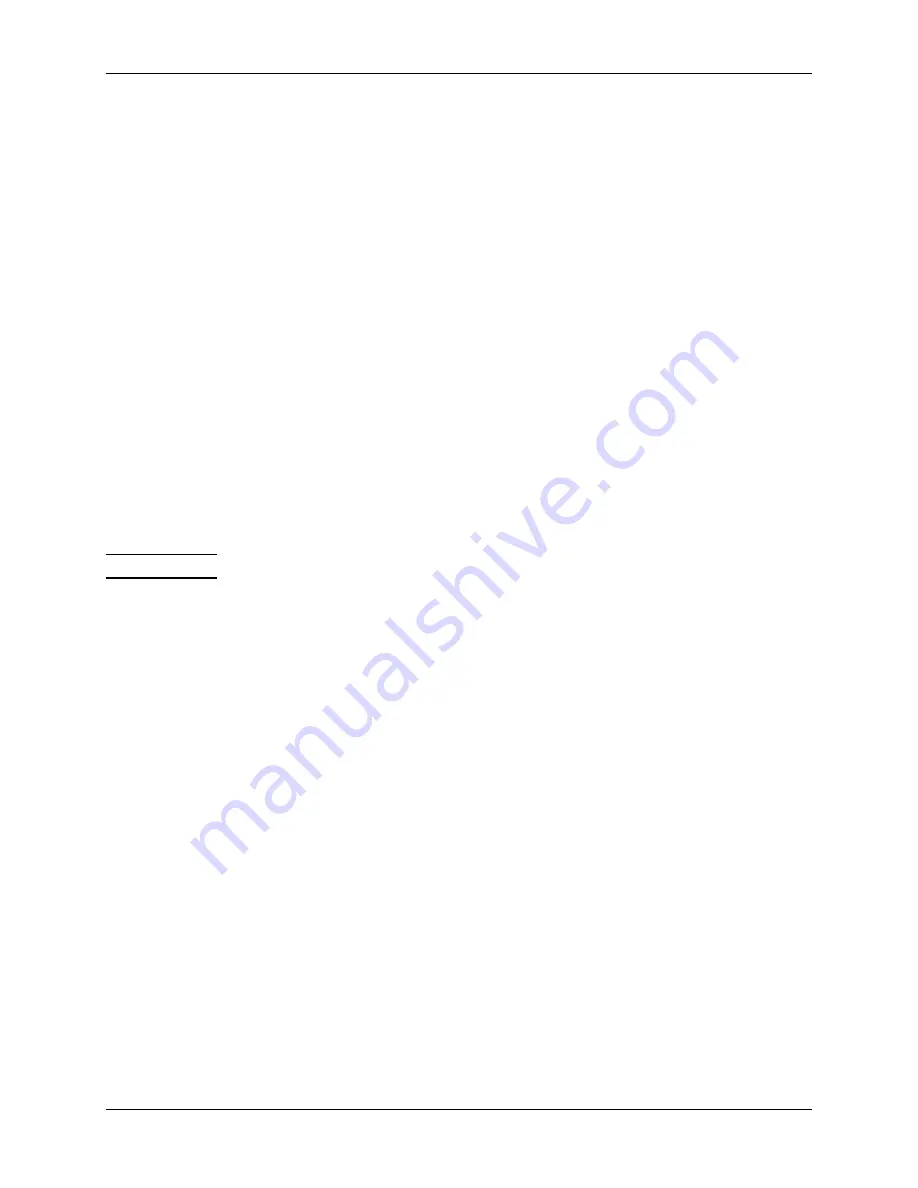
MANOWNROSM
OPERATING INSTRUCTIONS
US Filter
13
C.
Place the controller in the DIRECT FEED mode.
D.
After five minutes of operation to allow the system to stabilize, verify and record
the operating data in the daily log sheet (sample in Appendix). Follow the
procedures outlined in the Maintenance Summary section of this manual.
E.
Set the percent rejection alarm to the limits prescribed by the physician. The
alarm limits for the purposes of monitoring shall be calculated based on the
feedwater analysis and initial rejection characteristics and shall correspond to the
highest rejection coefficient at which contaminants reach unsafe limits. Consult
your US Filter representative for the determination of these limits.
Under no
circumstances is it recommended that the alarm be set at less than 90%.
F.
After performing checks and recording the results reset the MODE SELECTION
SWITCH to the desired location if necessary. If a storage tank is utilized, set the
MODE SELECTOR SWITCH to the TANK FEED position. If no storage tank is
used, set the MODE SELECTION SWITCH to the DIRECT FEED position. The
system is now ready to begin dialysis.
3.5
SHUTDOWN (LESS THAN 4 DAYS)
If the system is not to be run for up to 4 days, the system should be placed in the
STANDBY mode of operation. This will allow the system to return to operation at any
time with no adverse affects on the permeate or membranes.
CAUTION
If the shutdown is due to a malfunction, be sure to disconnect the
electrical power and turn off the water supply before making repairs or
replacements.
3.6
PROLONGED SHUTDOWN (GREATER THAN 4 DAYS)
When the system is going to be inactive for more than 4 days (not in a STANDBY
mode), perform the following steps:
A.
Turn off the feedwater source.
Bisulfite Sanitization (4 days to 1 month shutdown)
Drain water from the system and pump in a 0.5% sodium bisulfite solution
to prevent biological growth in the elements.
or
Formaldehyde Sanitization (shutdowns exceeding 1 month)
Drain water from the system and pump in a solution of 3% formaldehyde
to prevent biological growth and kill residual bacteria.
B.
Remove the prefilter cartridges and discard. Clean the prefilter housing, leaving
the cleaned components to dry during the shutdown period.
C.
Turn off the feedwater and electrical power until the system is to be placed into
operation again.
D.
To resume system operation, first drain the solution from the RO housings,
install new prefilter cartridges, disconnect the permeate line from the reservoir