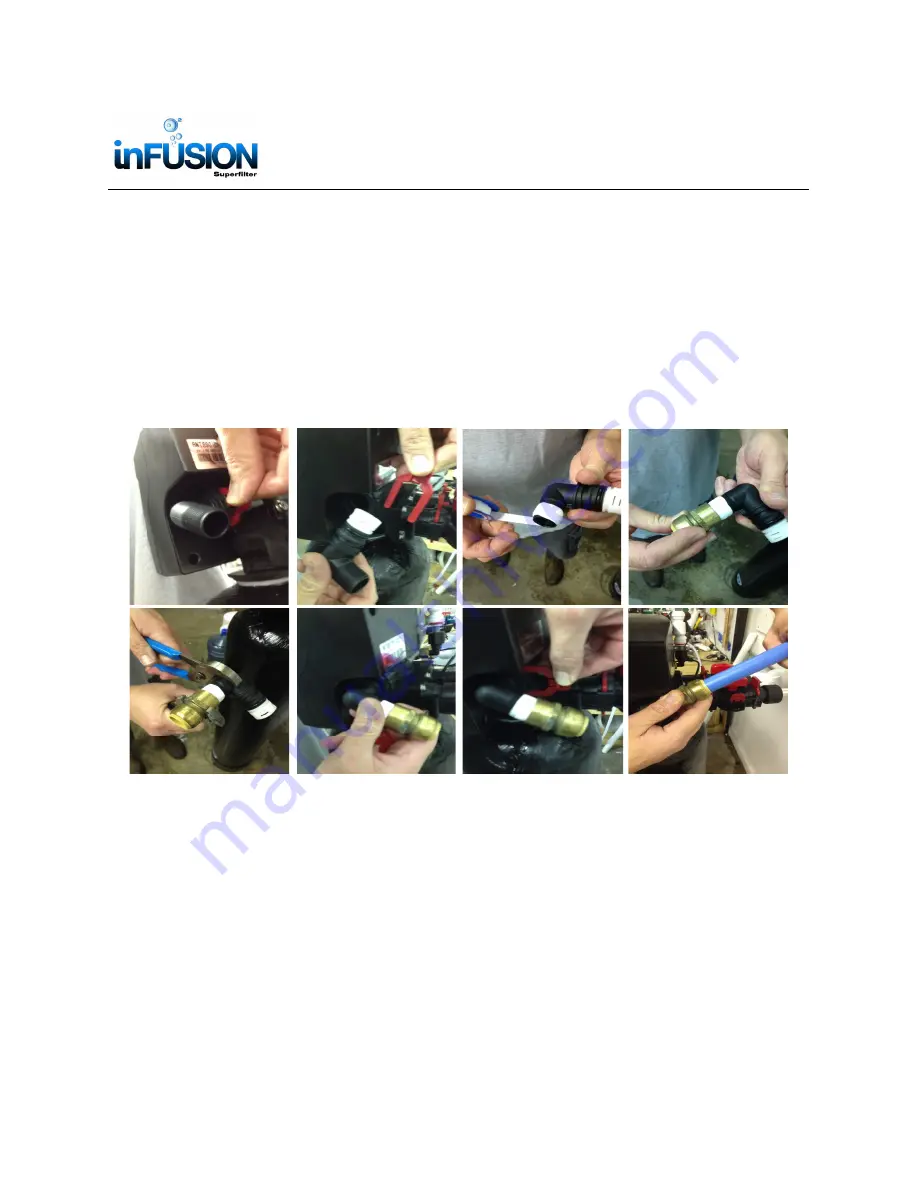
17
13. Install the drain line on the 3/4” threaded elbow This should be a 3/4” solid pipe con-
veyed to a floor drain, sink drain or stand pipe. This drain line can be any material al-
lowed by the local code (photos show PEX but PVC is typically the piping used). An air
gap should be established if the local code requires it. Drain line smaller than 3/4” could
cause a restriction on the system and prevent it from backwashing properly. If the drain
line is reduced to a size smaller than 3/4”
BE SURE
it can provide the backwash flow
rate requirement of the unit being installed. Drain line larger than 3/4” is acceptable.
The system will drain with pressure, so the drain line can be ran vertically for up to 5’. If
the drain line is ran vertically then along the wall horizontally, make sure the horizontal
pipe/tubing has a drop to the final drain point. The system should be plumbed with the
least amount of back pressure on the drain line.
14. The drain elbow can be removed by removing the red clip and pulling the elbow out of
the valve. This will make it easer to connect the plumbing fitting used.
BE CAREFUL
not to cross thread the fitting on the elbow.
There is a small thread tolerance for this fit-
ting to help reduce the potential for a leak so it can be cross threaded easily.
NOTE: It may be necessary to install drain line larger than 3/4” on a linear stretch of
drain line that exceeds 15’.
Installation, Operation and Maintenance Manual
Models: 089-IF-150, 089-IF-250, 089-IF-400,
089-IF-500