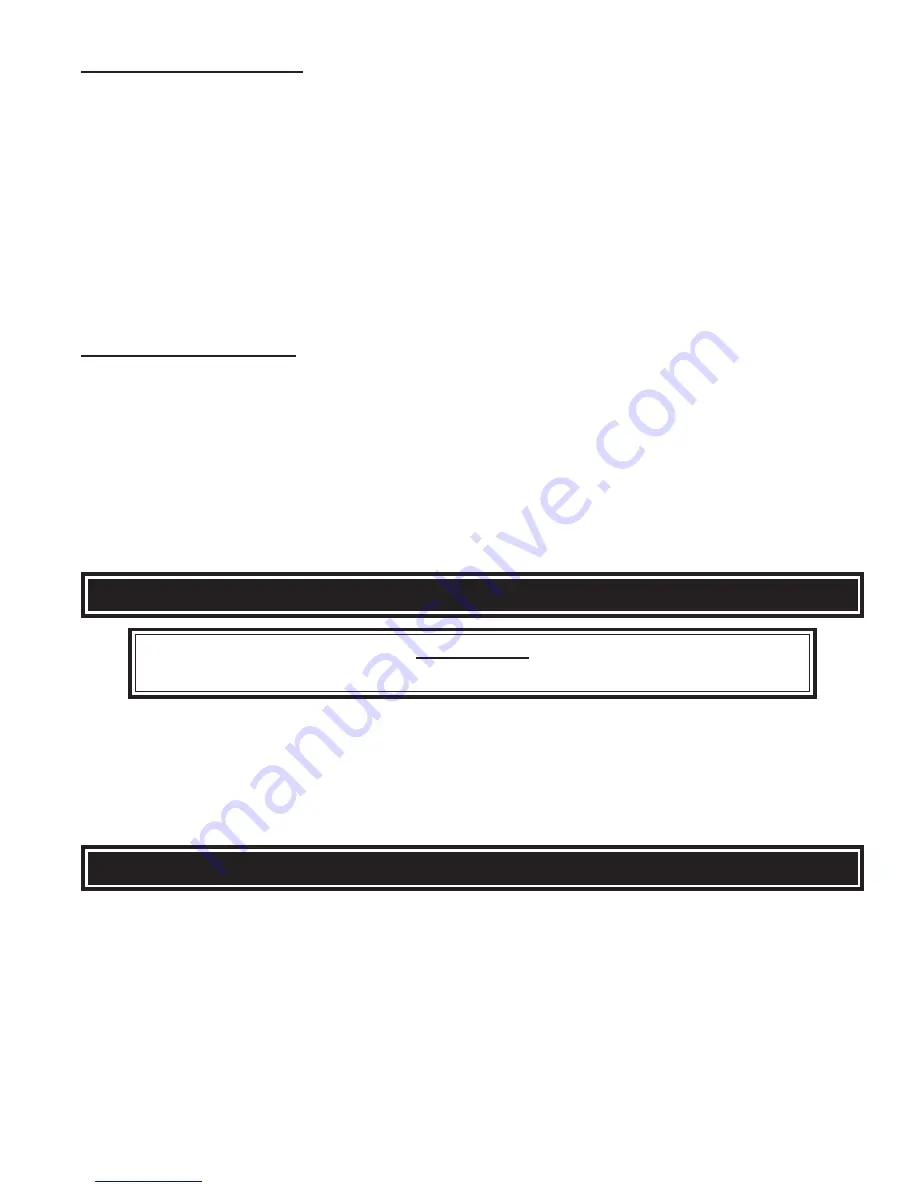
USSC
15
FUEL ADDITIVE
Chicken Scratch for my Corn Burner?
Yes - Crazy as it may sound, ground Oyster Shells, (calcium carbonate) same as fed to chickens, is the ideal additive to
promote clean burning, especially when the Corn Fuel is extra high in starch. And it’s available at your local Feed and Seed.
The “average” mixture is 1/2 pound of Oyster Shells (about 2 handfuls) to 60 pound of Corn, a full hopper. IF the “fingers”
on your agitator (stirrer or rouser) have a noticeable buildup of “clinkers” or stubborn deposits, you have either a high starch
fuel OR are burning with too much air for proper combustion and are reaching the “fusion” temperature of the Potassium
and/or Starch in the Corn. You need Oyster Shells - and maybe more than a couple handfuls.
If you notice a heavy accumulation of “whitish powder” in your burn pot, reduce the amount of Oyster Shell Additive.
Remember, using this additive- as necessary - promotes efficiency (higher heat output), reduces maintenance, clinkers and
ash content.
WARNING
These automatic safety features must not be bypassed
AUTOMATIC SAFETY FEATURES
•
•
Power Outage
During a power outage, the stove will shut down safely. It will not automatically restart when the power returns,
unless
the stove is still above the proper operating temperature.
(see “Lighting Instructions” page 13).
Overheating
A high temperature switch will automatically shut down the stove if it overheats. The stove will need to be manually relit.
Allow 45 minutes before relighting.
Shut down the stove as directed in the operating instructions. Allow the stove to cool to room temperature. Remove the
small clean-out slides in the lower corners of the firebox. Tap the sides of the burn chamber with a wooden stick. Do not
tap the firewall behind the burn box as it may damage the insulation. Scrape the fly ash from the clean-out chambers
toward the front of the burn chamber. Remove the fly ash from the burn chamber and replace the clean-outs.
Remove the ash pan and dump the ash into a metal container.
Cleaning of the exhaust system will depend upon the ash and debris content of your fuel. If your fuel has a high ash
content and/or significant debris in it, your exhaust system will require weekly cleaning. Cleaner fuels will allow for
monthly cleaning of the exhaust system. Remove the exhaust pipe from the back of your stove and remove any ash that
may have collected in the pipes. Replace the pipes to the stove and seal with high temperature seal tape. If you have
installed proper clean out tees you will not have to take the chimney sections apart.
REMEMBER: A clean unit burns efficiently and will remain trouble free!
Weekly Maintenance
SPRING CLEANING:
When the heating season is over make sure that you clean out all of the fuel in the hopper, firebox area, ash pan and firepot
area. Corn and any ash can accumulate moisture over the summer months causing the unit to rust and the fuel to mold.
It is recommended that prior to shutting down the unit in the spring, run the unit on the higher settings for a day to help clean
out the heat exchanger system, venting system and firebox area.
When the unit is cleaned out, take the venting apart, clean out the fly ash, rinse the venting out with a water hose and let dry,
take the draft blower off and clean, clean out all areas such as back heat exchanger and lubricate the auger, auger tube,
firepot area, fuel stirrer shaft and bearings and hopper area with a light oil (something like Pam cooking oil works great to
coat the inside of the unit and the moving parts). Clean the glass, doors and outer cabinet so that you are ready for the next
heating season. Use of a wet/dry vacuum makes all clean out easier and cleaner.
•
•
•
Downloaded from
www.Manualslib.com
manuals search engine