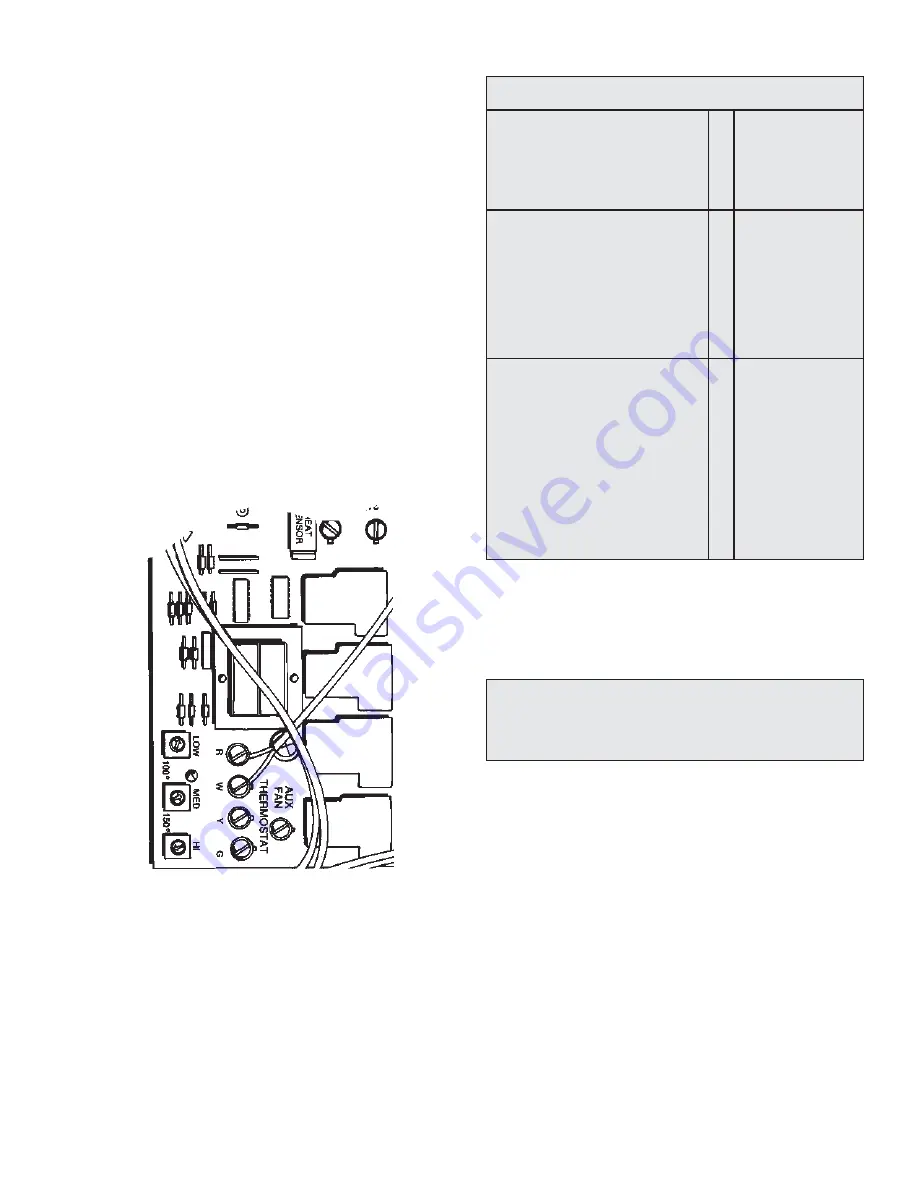
3-SPEED BLOWER ADJUSTMENT
The control center is equipped with three adjustments that
allow you to select the temperature at which the blower starts
operating and automatically switches from one speed to the
next.
With the three controls you can set the blower for single (high
speed operation), two speed operation, or three speed
operation.
The High-Only setting is usually recommended for larger
structures where the maximum air flow is required to achieve
efficient, uniform heating. (Improper adjustment can cause
undesirable cycling.)
The two or three speed settings are more applicable to smaller
or medium sized structures and generally make more efficient
use of the available heat. Because the blower speeds can be
set to automatically change as the plenum temperature
increases or decreases, the heat output can be maintained at a
more uniform level throughout the cycle of the fire.
The temperature range shown on each control corresponds to
the air temperature as measured at the furnace plenum.
INITIAL FACTORY SETTING FOR 3 SPEED OPERATION.
(For any other blower setting see chart)
NOTE: BLOWER MOTOR CFM'S FOR THE 1600/1800 ARE:
BLUE-1250 CFM
BLACK-1400 CFM
RED-1100 CFM
Refer to the following chart to select the blower speed options.
If you find the air from the heat registers is too cool, turn
Control 1 to a higher temperature setting. The setting of
Control 3 for two speed operation and Controls 2 and 3 for
three speed operation may also be adjusted up or down to
maintain a more constant temperature output.
3 Speed Distribution Blower Operation
●
when thermostat calls for heat: L-M-H, H-M-L
●
when thermostat isn't calling forhear: H, H-M-L
LOW 1
MED 2
HIGH 3
BLOWER
ADJUSTMENTS
USE SMALL SCREWDRIVER (SUPPLIED)
TO MAKE FURTHER ADJUSTMENTS
BLOWER OPERATION CONTROL
SETTING
One Speed (HIGH)
1
Turn to temperature
where you wish
All 3 board wires connected to
blower to start.
high speed wire of blower. Tape
off low and medium wires to
2
Set at 150°
avoid accidental shorting.
3
Set at 150°
Two Speed
1
Turn to temperature
(MEDIUM AND HIGH)
where you wish
blower to start.
Connect low speed board wire to
medium speed blower wire. Connect
2
Set at least 5°
medium and high speed board wires
higher than Control 1.
to high speed blower wire. Tape off
low speed blower wire to avoid
3
Set at 150°
accidental shorting.
Three Speed
1
Turn to temperature
(LOW,MEDIUM,
where you wish
AND HIGH)
blower to start.
2
Set at least 5°
higher than Control 1.
3
Set at least 5°
higher than Control 2.
(Initial factory setting:
Control 1 - 110°
Control 2 - 120°
Control 3 - 140°
OPTIONAL
21
Summary of Contents for Clayton 1600
Page 30: ...N o t e s ...
Page 31: ...N o t e s ...