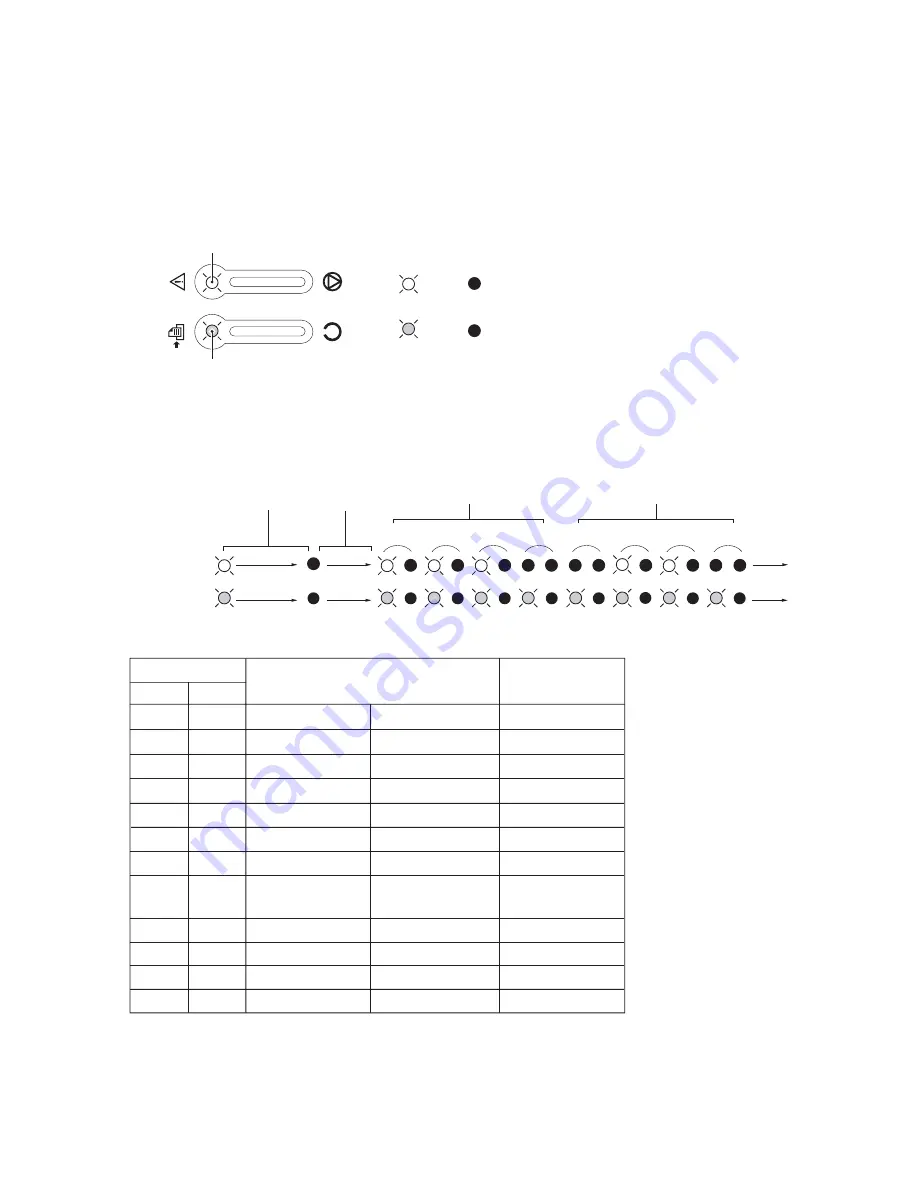
2GL/2FV/2FW
1-5-3
1-5-2 Self-diagnosis
(1) Self-diagnostic function
When a self diagnostics error occurs, the printer halts and displays the appropriate error code using a combination of the
READY and ATTENTION indicators.
Figure 1-5-3 Self-diagnostic code indication
Off
Off
Lit
Lit
LED indicator
Indication example
E
6
1
1
1
1
1
0
0
1
E0
E1
E2
E3
E4
E6
F1
F2
F3
D9
7980
7990
F040
F010
F020
F030
2000
4000
4200
6050
6000
6010
F050
2 digits
4 digits
Self-diagnostic code
DA
1
1
0
0
0
0
0
1
1
1
0
0
1
0
0
1
1
1
0
1
0
0
0
1
1
1
0
1
1
0
0
1
1
1
1
0
0
0
0
1
1
1
1
1
0
0
0
1
1
1
0
0
1
1
0
1
1
1
0
1
0
1
0
1
1
1
0
1
1
1
0
1
1
0
0
0
1
1
1
A0
6400
1
0
1
0
0
0
0
0
1
1
0
0
1
0
1
1
ATTENTION indicator
Interval
(Hexadecimal)
Repeat
Example: self-diagnostic code: E6 (F050)
Self-diagnostic code conversion table
READY indicator (Green)
READY
ATTENTION indicator (Amber)
ATTENTION
0
7.3 s
2.4 s
16/18 ppm printers only
Remark
The ATTENTION indicator means 1 when it flashes in synchronization with the
READY indicator which flashes at the interval of 1.2 second; and it means 0 when it
turns off: This is repeated 8 times. Two digit self diagnostics codes are indicated in 8
bits (2 digits hexadecimal) using the ATTENTION indicator.
Indicates the
occurrence of a self
diagnostics error.
Summary of Contents for LP 3118
Page 1: ...Service Manual Printer LP 3118 22 02 2005 ...
Page 2: ...Service Manual Printer LP 4118 22 02 2005 ...
Page 7: ...This page is intentionally left blank ...
Page 19: ...2GL 2FV 2FW 1 1 10 This page is intentionally left blank ...
Page 21: ...2GL 2FV 2FW 1 2 2 This page is intentionally left blank ...
Page 29: ...2GL 2FV 2FW 1 3 8 This page is intentionally left blank ...
Page 41: ...2GL 2FV 2FW 1 4 12 This page is intentionally left blank ...
Page 65: ...2GL 2FV 2FW 1 5 24 This page is intentionally left blank ...
Page 95: ...2GL 2FV 2FW 1 7 6 This page is intentionally left blank ...
Page 125: ...2GL 2FV 2FW 2 4 6 This page is intentionally left blank ...
Page 126: ......