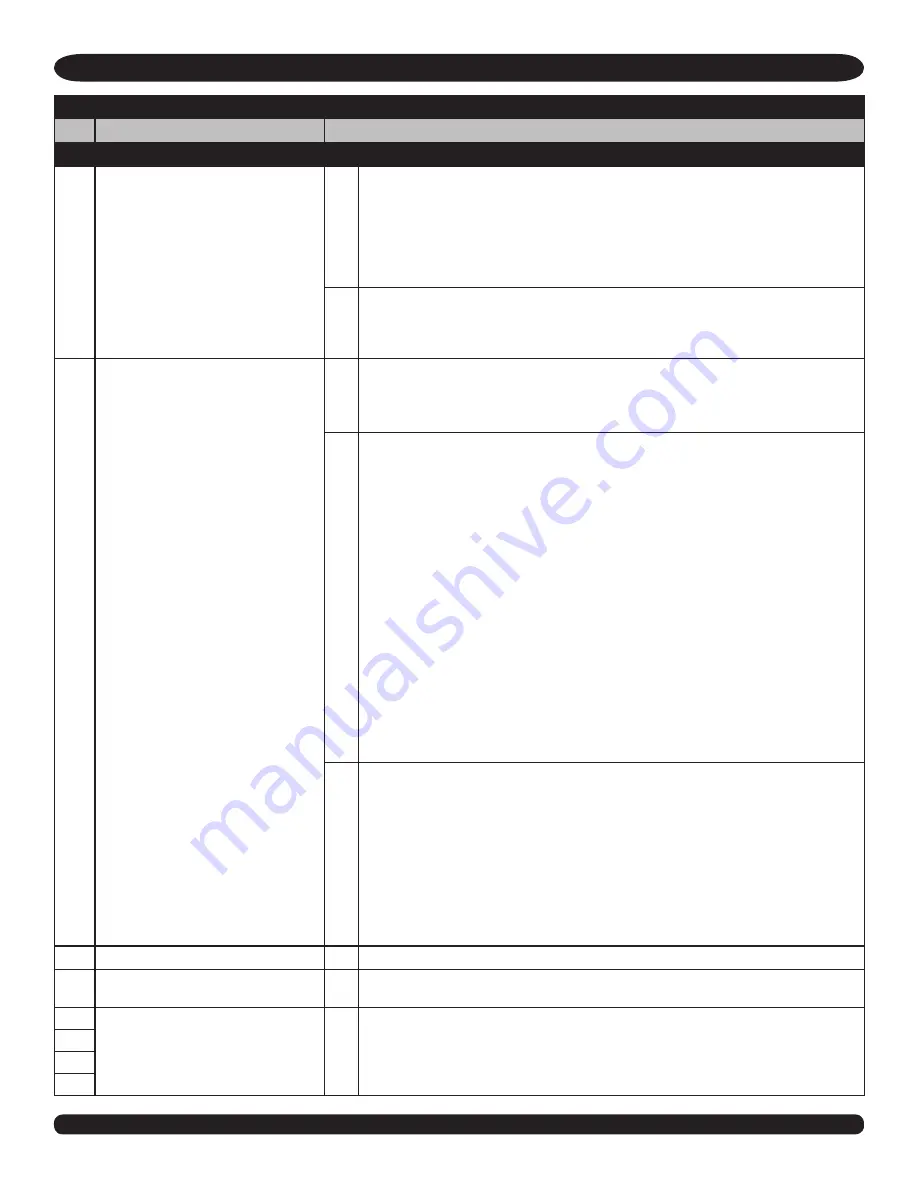
18
VIII - TROUBLESHOOTING
HARD LOCKOUT
(Display flashes first digit “E” and last two digits (code))
Code
Reason For Hard Lockout
Corrective Actions
(pressing RESET should restart boiler immediately):
WARNING:
Electrical shock hazard. Turn off power to boiler when working with wiring or replacing any boiler component.
00
Flame detected on startup.
1
Burner may be operating too hot due to incorrect combustion. Inspect flame during
operation following the procedure in this manual. If flame is acceptable at both high
and low fire, go to step 2. If flame is not acceptable:
For propane boilers, verify propane orifice is correct and properly installed.
•
Obtain and install propane orifice if necessary.
For correctly orificed propane or natural gas boilers, replace gas valve if
•
burner glows excessively.
2
Look into the burner inspection window after the boiler shuts down. If flame is still
present, gas valve may be leaking. Replace gas valve. BEFORE replacing valve,
check gas line pressure coming to boiler. Pressure must not exceed 13” w.c. or
valve damage could occur.
02
Ignition failed through 5 attempts.
1
If no ignition spark occurs:
Check ignition electrode cable, electrode connector, and connections.
•
Inspect ignition electrode cable and electrode for insulation damage.
•
Check ground lead from ground terminal strip to heat exchanger access cover.
•
2
If spark occurs, but no flame:
Verify manual gas valve in boiler is open.
•
Verify plastic line from gas valve to air inlet elbow is connected to gas valve
•
and elbow, and line is unobstructed with no kinks.
Check incoming gas pressure.
•
Verify gas lines are free of obstruction and purge gas lines of air if
•
necessary.
Verify flue gas vent and air supply piping are correctly installed, in good
•
condition, and free of obstructions.
Check voltage to gas valve (it should be approx. 19-21 vdc (24 vrac) during
•
ignition attempt).
Check gas meter to verify gas flows when gas valve is activated.
•
Remove and inspect/clean ignition electrode. Clean white oxides if necessary
•
and replace ignition electrode if in poor condition or unable to be cleaned.
Disconnect gas valve from Venturi. Inspect Venturi gas line to verify there are
•
no obstructions. Replace gas valve.
Check for possible flue gas recirculation at vent/air terminations or inside
•
boiler housing.
If gas valve is powered, gas flows when activated, and above steps have
•
been verified, replace gas valve and retry.
3
Flame occurs but flame signal too low (less than 3 vdc between X1-5 and ground):
Inspect flame at both low and high fire rates. Inspect and clean burner if
•
necessary. Replace burner if not in good condition.
Check gas flow rate at gas meter with boiler at high fire. If input is not within
•
about 10% of boiler rating, replace gas valve. (Length of the vent/air piping will
affect boiler firing rate, with longer piping causing lower inputs.)
Check ground wire and connections from ground terminal screw to X1-6 terminal
•
on wiring harness. Use ground continuity meter to verify good ground path.
Follow procedure to inspect and clean ignition electrode. replace ignition
•
electrode if necessary.
If above does not correct problem, replace control module.
•
03
gas Valve disconnected.
1
Verify gas valve connection.
04
Voltage lost after lockout occurred.
1
Control module will only restart with manual reset, even after power loss (but the
error code information is lost).
05
internal control failure.
1
Reset control and retry. If problem persists, replace control module.
06
07
08