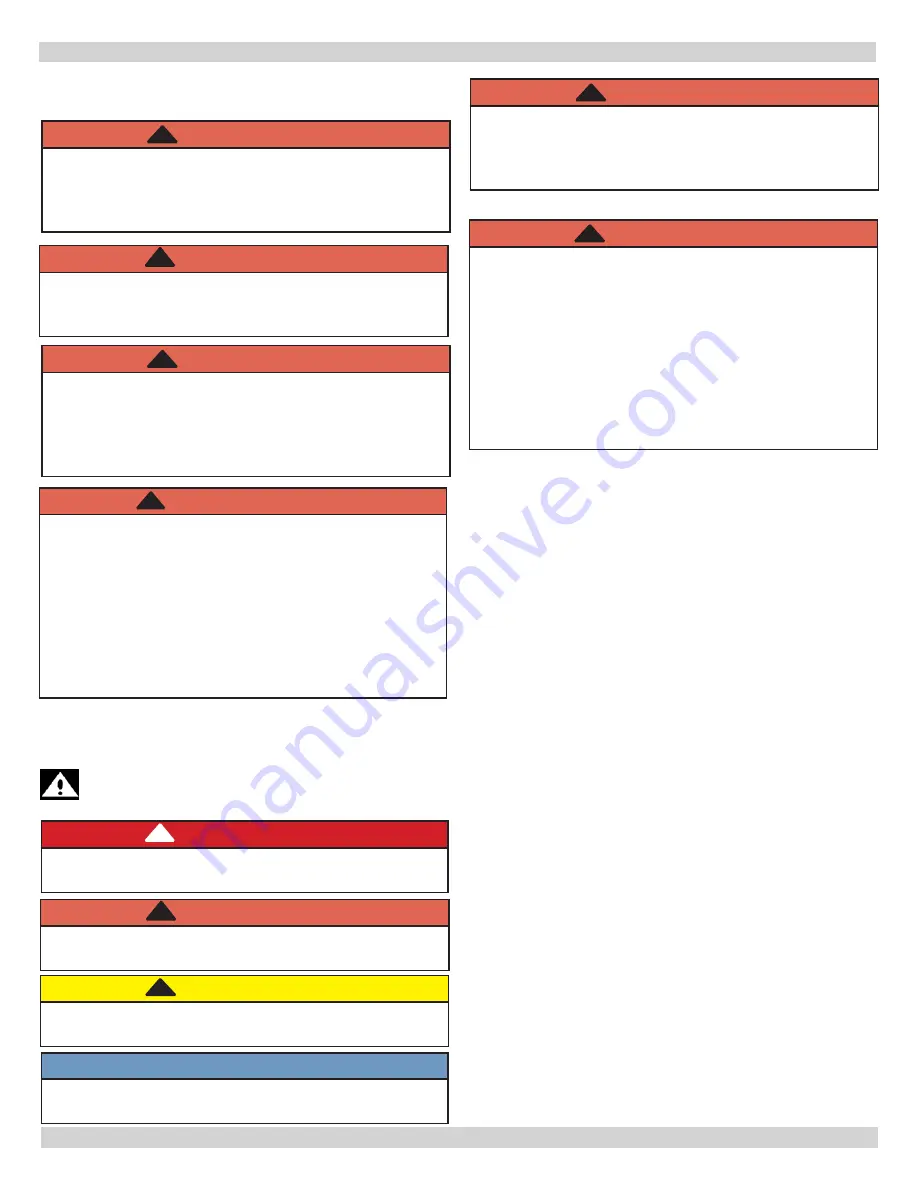
4
NOTICE
Used to address practices not related to personal
injury�
CAUTION
Indicates a hazardous situation which, if not avoided,
could result in minor or moderate injury�
!
!
WARNING
Indicates a hazardous situation which, if not avoided,
could result in death or serious injury�
!
DANGER
Indicates a hazardous situation which, if not
avoided, WILL result in death or serious injury
!
This is the safety alert symbol� Symbol alerts you
to potential personal injury hazards� Obey all safety
messages following this symbol to avoid possible
injury or death�
Become familiar with symbols identifying potential
Become familiar with symbols identifying potential
hazards.
hazards.
WARNING
Modification, substitution or elimination of factory
equipped, supplied or specified components could
result in death or serious injury�
!
3.1 - General
Boiler installation shall be completed by qualified agency.
WARNING
Fire, explosion, asphyxiation and electrical shock
hazard� Improper installation could result in death
or serious injury� Read this manual and understand
all requirements before beginning installation�
!
WARNING
Installation or venting a boiler or any other oil
appliance with improper methods or materials may
result in serious injury or death due to fire or to
asphyxiation from poisonous gases such as carbon
monoxide which is odorless and invisible�
!
3.2
- Installation shall conform to requirements
of authority having jurisdiction or in absence of
such requirements to current edition of ANSI/NFPA
31, “Standard for the Installation of Oil Burning
Equipment”. Such applicable requirements take
precedence over general instructions of this
manual.
3.3
- Installation shall conform to requirements
of authority having jurisdiction or in absence of
such requirements to Current Edition of American
National Standard ANSI/NFPA 211 “Standard
for Chimneys, Fireplaces, Vents and Solid Fuel
Burning Appliances” for venting.
3.4
-
Where required by authority having
jurisdiction, installation shall conform to
Standard for Controls and Safety Devices for
Automatically Fired Boilers, ANSI/ASME CSD-1.
Additional manual reset low water cutoff and manual reset
high limit may be required�
3.5
- Requirements for Commonwealth of
Massachusetts:
Boiler installation must conform to Commonwealth of
Massachusetts code 248 CMR which includes but is not
limited to: Installation by licensed plumber or gas fitter.
3 - SAFETY INFORMATION
WARNING
Construction materials of appliance and products
of combustion and fuel contain alumina, silica,
heavy metals, carbon monoxide, nitrogen
oxides, aldehydes and /or other toxic or harmful
substances which can cause death or serious injury
and which are known to the State of California to
cause cancer, birth defects and other reproductive
harm� Always use proper safety clothing,
respirators and equipment when servicing or
working nearby the appliance�
!
WARNING
Before filling boiler verify heat exchanger is not
hot� Adding water to hot water could result in
heat exchanger failure� Failure to follow these
instructions could result in death or serious injury�
!
WARNING
Fire, Explosion, Asphyxiation, Electrical shock
hazard! Flooding will result in damages such as
electrical problems, corrosion, inoperative parts,
mold and other unforeseen issues which can
occur over time� Any equipment determined by
a professional as damaged by a flood, defined as
excess of water or other liquid, shall be replaced�
Failure to follow these directions will result in a
Hazardous Situation�
!
PN 240013073, Rev. A [08/31/2020]