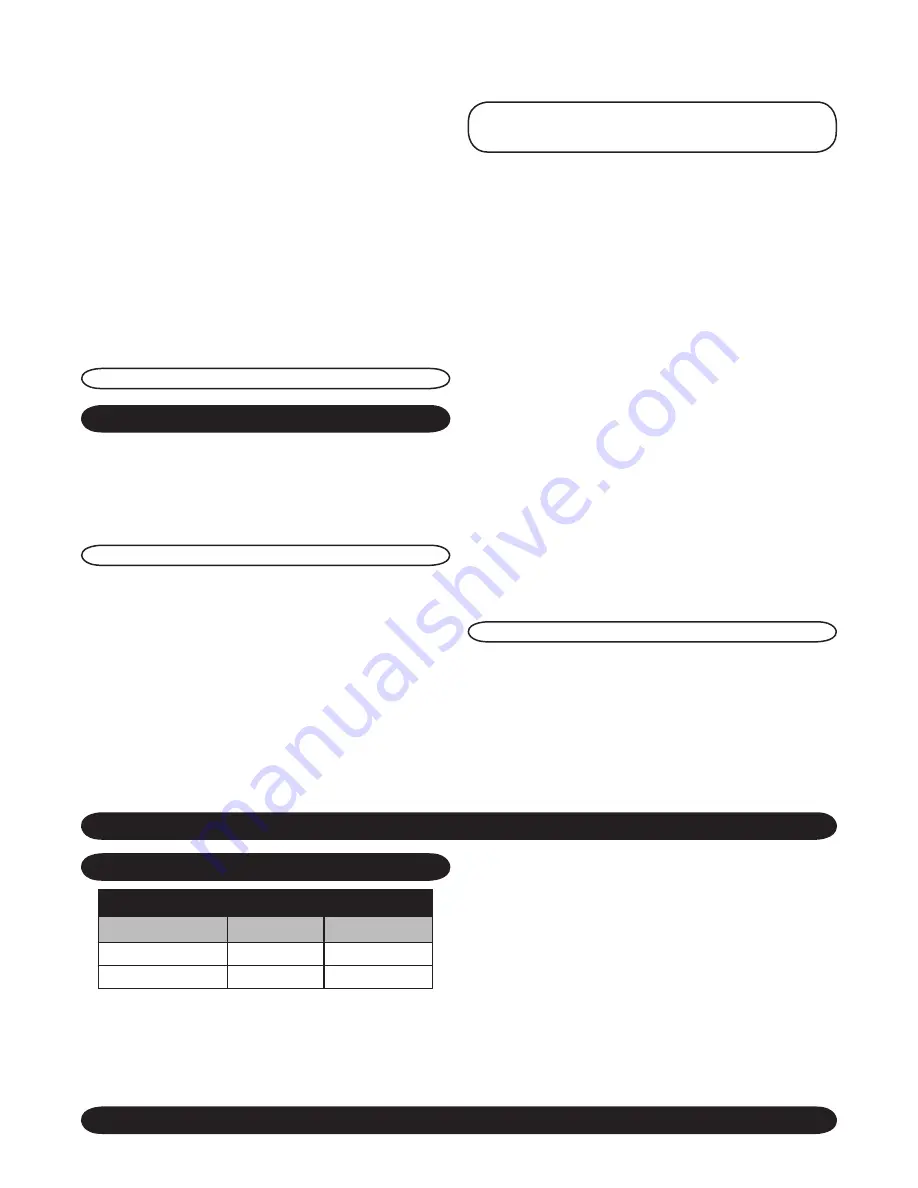
13
above grade. Termination of the vent shall be
not less than 7 feet above an adjacent public
walkway. The vent terminal shall not be installed
closer than 3 feet from the inside corner of an L
shaped structure. Termination of the vent should
be kept at least 3 feet away from vegetation.
The venting system shall terminate at least 4
feet horizontally from, and in no case above or
below electric meters, gas meters, regulators,
and relief equipment.
If multiple terminations are used, there must be
a minimum of 12 inches between the exhaust
of one termination and the air intake of the next
termination. See Figures 1-3 in Section E5 for il-
lustrations.
NOTE:
All field installed vent pipe must be 3”.
INSTALLATION
1. Attach combustion air intake piping to sup-
plied Fernco 2” coupling on CVI gas valve. At-
tach vent piping to furnished 2” CPVC vent tee
on draft inducer outlet.
NOTE:
All pipe joints are to be water tight.
2. Working from the boiler to the outside, cut
pipe to required length(s).
3. Deburr inside and outside of pipe. Remove all
chips and shavings.
4. Chamfer outside edge of pipe for better distri-
bution of primer and cement.
5. Clean and dry all surfaces to be joined.
6. Check dry fit of pipe and mark insertion depth
on pipe.
NOTE:
It is recommended that all pipes be cut, prepared, and
pre-assembled before permanently cementing any joint.
7. After pipes have been cut and pre-assem-
bled, apply cement primer to pipe fitting socket
and end of pipe to insertion mark. Quickly apply
approved cement to end of pipe and fitting sock-
et (over primer). Apply cement in light, uniform
coat on the inside of socket to prevent buildup of
excess cement. Apply second coat.
8. While cement is still wet, insert pipe into sock-
et with a ¼ turn twist. Be sure pipe is fully in-
serted into fitting socket.
9. Wipe excess cement from joint. A continuous
bead of cement will be visible around perimeter
of a properly made joint.
10. Handle pipe joint carefully until cement sets.
11. Support combustion air and vent piping a mini-
mum of every 5 feet using pre-formed metal hang-
ing straps. Do not rigidly support pipes. Allow for
movement due to expansion and contraction.
NOTE:
Rigid supports will cause excess noise in vent piping.
12. Slope combustion air and vent pipes toward
boiler a minimum of ¼” per linear foot with no
sags between hangers.
13. Use appropriate methods to seal open-
ings where vent and combustion air pipes pass
through roof or side wall.
IX. GAS SUPPLY PIPING
CHECK GAS SUPPLY
The gas pipe to your boiler must be the correct size
for the length of run and for the total BTU per hour
input of all gas utilization equipment connected to
it. See Table 6 for proper size. Be sure your gas
TABLE 5 - GAS SUPPLY PRESSURE
Pressure
Natural Gas Propane Gas
Minimum
4” w.c.
10” w.c.
Maximum
10” w.c.
14” w.c.
Please check line pressure while unit is running.
line complies with local codes and gas company
requirements.
The boiler and its individual shutoff valve must be
disconnected from the gas supply piping system
during any pressure testing of that system at test
pressures in excess of ½ psig (3.5kPa).
The boiler must be isolated from the gas supply pip-
ing system by closing its individual manual shutoff
valve during any pressure testing of the gas supply
piping system at test pressures equal to or greater
than ½ psig (3.5kPa).